Adapt to Supply Chain Disruption: Staffing Solutions for Manufacturers
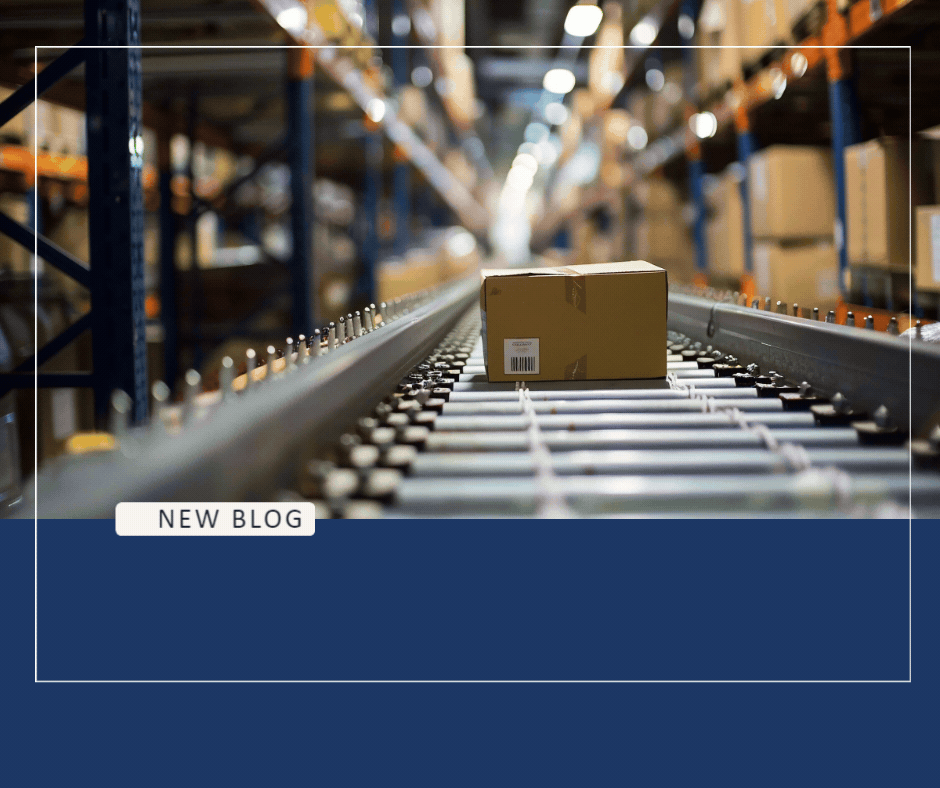
Supply chain disruptions are increasingly common in manufacturing, and staffing solutions play a critical role in minimizing their impact. Key strategies include flexible workforce models, such as temporary or contract workers, which allow manufacturers to adjust staffing levels quickly. Cross-training and upskilling employees provide operational flexibility, enabling workers to fill various roles and reduce downtime. Additionally, recruiting specialized talent, such as logistics experts, can help manufacturers navigate complex supply chain challenges and develop contingency plans. By focusing on these staffing solutions, manufacturers can maintain operational continuity and improve their ability to adapt to disruptions, ensuring that they stay competitive in a rapidly changing environment. A resilient and adaptable workforce is essential for long-term success.
Supply chain disruptions have become an increasing challenge for manufacturers in recent years. Whether due to global events, natural disasters, or shifting market demands, these disruptions can hinder production timelines, delay shipments, and create unforeseen costs. While manufacturers often focus on sourcing alternatives or improving logistics to address these issues, there’s another critical component that plays a major role in navigating supply chain challenges: staffing.
At Resource Employment Solutions, we understand that having the right workforce in place can be a key differentiator when responding to supply chain disruptions. The ability to quickly adjust staffing levels, recruit specialized talent, and cross-train existing employees can help manufacturers maintain operational continuity, even in the face of uncertainty. Below, we explore three staffing solutions that can help manufacturers adapt to supply chain disruptions, along with real-world examples to illustrate their effectiveness.
1. Flexible Workforce Solutions
One of the most effective ways to adapt to supply chain disruptions is by implementing flexible workforce solutions. Disruptions often lead to fluctuating production demands, where companies may need to scale their workforce up or down at short notice. Flexible staffing models, such as temporary or contract workers, can help manufacturers respond to these changes without committing to long-term hires.
For example, a global electronics manufacturer faced a significant supply chain disruption due to a component shortage. With production schedules impacted, they had to reduce workforce hours temporarily. However, when a new supplier was secured, the company needed to ramp up production quickly. By leveraging a staffing agency to bring in temporary workers, they were able to meet the sudden demand spike without the financial burden of full-time hires. This flexibility allowed the company to stay on track with delivery timelines while keeping operational costs under control.
In unpredictable environments, the ability to scale staffing levels based on immediate needs provides manufacturers with a critical competitive advantage. Temporary staffing helps bridge gaps during disruptions and ensures production can quickly return to full capacity when the situation stabilizes.
2. Cross-Training and Upskilling Employees
Supply chain disruptions often result in bottlenecks, where certain parts of the production line may be slowed or stopped altogether. During these times, it’s essential that manufacturers maximize the productivity of their existing workforce. Cross-training employees to perform multiple roles allows companies to shift workers to areas of need, reducing downtime and improving operational resilience.
For example, a food packaging company experienced a delay in receiving essential materials, causing parts of its production line to grind to a halt. Rather than sending workers home, the company utilized cross-training programs implemented months prior. Employees from the affected departments were temporarily reassigned to areas like quality control, warehousing, and maintenance, keeping operations running smoothly and reducing downtime. Once the materials arrived, the company was able to seamlessly transition workers back to their original roles.
By investing in cross-training and upskilling programs, manufacturers not only increase workforce flexibility but also enhance employee engagement, as workers are equipped with more diverse skill sets. This adaptability becomes invaluable when facing supply chain challenges, as it allows businesses to redeploy labor where it’s needed most.
3. Recruiting Specialized Talent
Supply chain disruptions often expose gaps in the workforce, particularly in areas that require specialized knowledge or expertise. Whether it’s managing complex logistics, implementing advanced technologies, or overseeing quality assurance, having the right experts in place is essential for navigating disruptions effectively.
For example, a medical device manufacturer faced severe shipping delays and supply shortages due to global trade issues. To mitigate the disruption, the company needed to optimize its supply chain strategy quickly. They partnered with a staffing agency to bring in a logistics specialist with experience in alternative sourcing strategies and supply chain optimization. This expert helped the company identify new suppliers, streamline their logistics, and develop contingency plans for future disruptions. Within weeks, the manufacturer was back on track with minimal impact on production timelines.
In times of disruption, specialized talent can make a significant difference in finding creative solutions and maintaining business continuity. Partnering with a staffing company to recruit experts as needed ensures that manufacturers have the right skills on hand to adapt to unexpected challenges.
Supply chain disruptions are a reality that manufacturers must navigate in today’s complex global environment. Having a flexible, well-trained, and adaptable workforce is key to mitigating the impact of these disruptions. By employing flexible staffing models, cross-training employees, and recruiting specialized talent when needed, manufacturers can maintain operational continuity and reduce downtime during periods of uncertainty.
While supply chain challenges are often unpredictable, focusing on workforce resilience helps manufacturers stay prepared and agile. Developing these staffing strategies ensures that businesses can respond more effectively to disruptions and continue to meet production goals, even in the face of unforeseen challenges. Building a workforce that can adapt to change is critical to long-term success in the manufacturing industry.
Written on behalf of RES.
The RES Onboarding Process
Our commitment to you is deeper than just providing a list of potential candidates. We are committed to designing and implementing the most effective staffing strategy for you. Here is what you can expect when you choose Resource Employment Solutions as your recruiting and staffing partner.
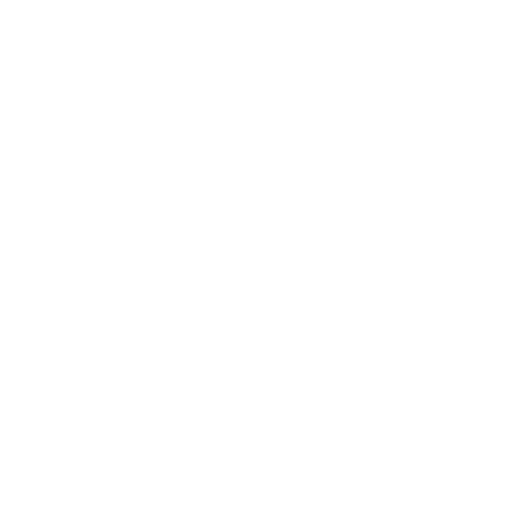
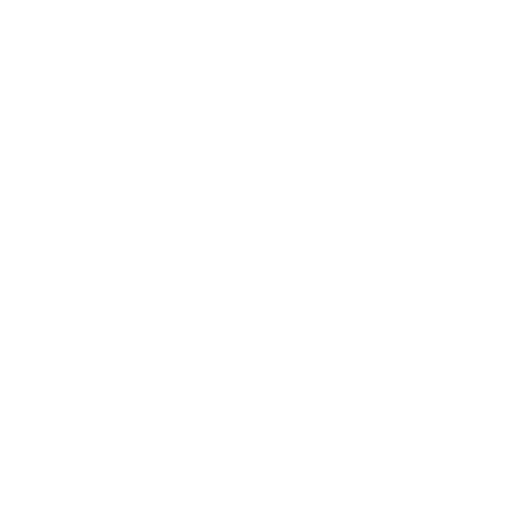
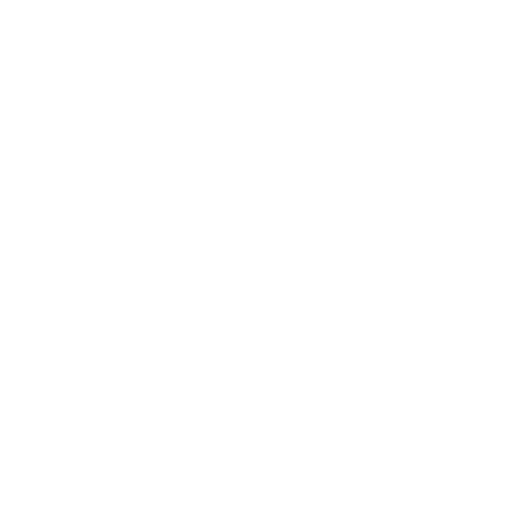
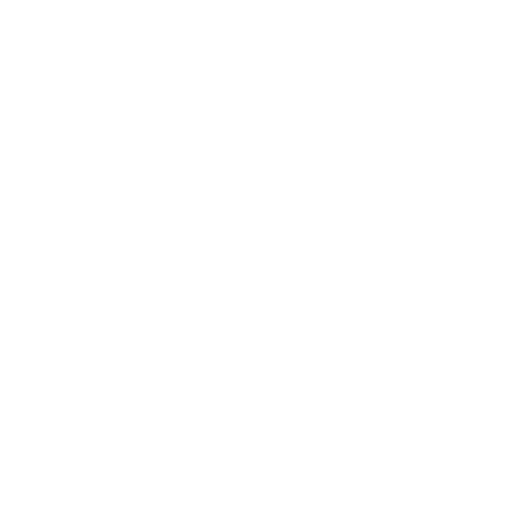
When you connect with Resource Employment Solutions, you will be matched with an account management team who specializes in placing top talent within your industry. You will have a dedicated recruiter or recruiting team assigned and they will remain your point of contact to understand your business and address all your staffing needs.
Frequently Asked Questions
Flexible staffing solutions, such as temporary or contract workers, allow manufacturers to quickly scale their workforce up or down based on immediate needs. This flexibility helps maintain production efficiency without the long-term commitment of permanent hires, ensuring manufacturers can adapt to sudden changes in demand.
Cross-training employees equips them with the ability to perform multiple roles. During supply chain disruptions, this allows manufacturers to redeploy workers to areas of need, reducing downtime and ensuring continued productivity.
Specialized talent, such as logistics experts, can offer valuable expertise in areas like sourcing, supply chain management, and contingency planning. Bringing in experts ensures manufacturers can develop effective strategies to minimize disruption and maintain production timelines.