Balancing Productivity and Employee Well-Being in Manufacturing | RES
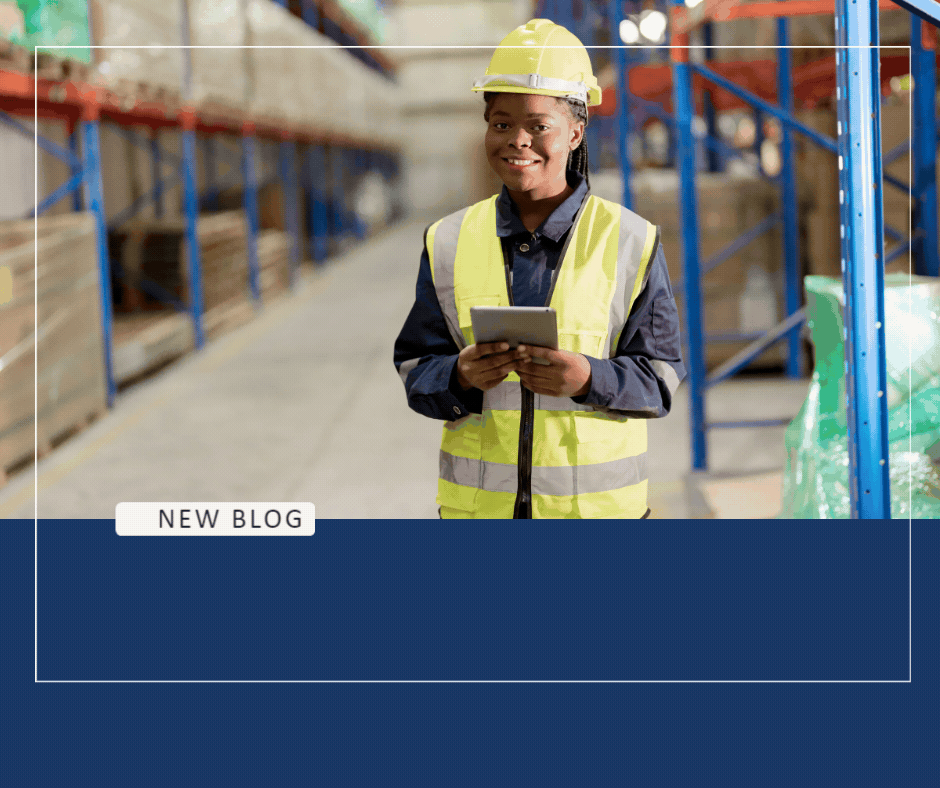
Balancing productivity and employee well-being in the manufacturing sector is crucial for maintaining a motivated and efficient workforce. Key strategies for achieving this balance include offering flexible work arrangements, enabling employees to better manage their work-life balance, and ensuring that health and safety remain a top priority to create a secure and supportive work environment. Additionally, investing in employee development and providing regular recognition for their efforts fosters a sense of job satisfaction and loyalty. These approaches not only boost employee morale but also lead to increased productivity, reduced absenteeism, and lower turnover rates. By prioritizing both operational efficiency and employee well-being, manufacturers build a resilient workforce, contributing to long-term growth and success in a competitive industry.
In the manufacturing industry, maintaining high levels of productivity is essential to meet business goals and remain competitive. However, the increasing focus on employee well-being has made it clear that a purely productivity-driven approach can lead to burnout, high turnover, and reduced job satisfaction. Striking the right balance between productivity and employee well-being is not only beneficial for workers but also essential for long-term business success.
At Resource Employment Solutions, we understand the importance of nurturing a healthy and engaged workforce while maintaining productivity. In this article, we will explore three strategies that can help manufacturers achieve this balance, each backed by real-world examples illustrating their effectiveness.
1. Implementing Flexible Work Arrangements
In manufacturing, where shifts and schedules are often rigid, offering flexibility may seem challenging, but it can greatly benefit both productivity and employee well-being. Flexible work arrangements—such as adjustable shifts, compressed workweeks, or hybrid roles that combine production and administrative tasks—can reduce stress and improve morale. When employees have a say in their schedules or are offered alternatives, they are more likely to be engaged and motivated, which translates into higher productivity.
For example, a furniture manufacturing company faced high absenteeism and declining morale among its production workers. In response, the company implemented a flexible shift system that allowed employees to swap shifts with one another and adjust their hours within reason to accommodate personal commitments. The company also introduced a compressed workweek option, allowing employees to work longer hours over fewer days. As a result, employee engagement improved, absenteeism decreased, and overall productivity rose by 15%.
Offering flexibility helps create a supportive work environment where employees feel empowered to balance their work and personal lives, leading to increased satisfaction and sustained productivity.
2. Prioritizing Health and Safety
In manufacturing, ensuring the health and safety of employees is paramount. A safe work environment not only protects employees from physical harm but also fosters a sense of security and well-being. When workers feel safe, they are more focused, less stressed, and more productive. Companies that actively invest in safety programs and promote a culture of well-being can enhance both productivity and employee loyalty.
An example can be a chemical manufacturing plant with a history of workplace accidents decided to overhaul its safety protocols and invest in new safety training programs for all employees. The company also implemented ergonomic improvements on the production floor, reducing strain on workers. In addition, they offered mental health resources and stress management workshops. These changes led to a 40% reduction in workplace accidents, as well as increased employee satisfaction. Over time, the company saw a noticeable improvement in productivity, as workers felt more secure and were able to perform their tasks more efficiently.
By prioritizing safety and health, manufacturers can create a positive work environment that boosts productivity while ensuring employees feel valued and cared for.
3. Encouraging Employee Development and Recognition
Investing in employee development not only improves workforce skills but also enhances well-being by providing opportunities for growth and job satisfaction. When employees feel that their work is recognized and that they have opportunities to advance, they are more engaged and productive. Recognition programs that celebrate both individual and team achievements can foster a positive work culture and drive performance.
For example, a large electronics manufacturer introduced a new employee development initiative focused on upskilling its workforce. Employees were offered on-site training and opportunities to enroll in external certifications. The company also launched a recognition program that rewarded both individual contributions and team successes, with awards given for creativity, problem-solving, and leadership. Over the course of a year, the company reported a 20% increase in productivity, accompanied by higher employee satisfaction scores and lower turnover rates.
Employee development and recognition are powerful tools that can simultaneously enhance productivity and well-being by creating an environment where employees feel valued, engaged, and supported in their professional growth.
alancing productivity and employee well-being in manufacturing is crucial for maintaining a motivated and efficient workforce. By adopting flexible work arrangements, prioritizing health and safety, and promoting employee development and recognition, manufacturers can create an environment that supports both operational goals and employee satisfaction.
While achieving this balance requires consistent effort, the benefits are clear: a more engaged workforce, improved retention rates, and sustained productivity. When employees feel valued and supported, they are more likely to contribute positively to the company’s long-term success. By focusing on both productivity and well-being, manufacturers can build a resilient workforce that thrives in a demanding and ever-evolving industry.
Written on behalf of RES.
The RES Onboarding Process
Our commitment to you is deeper than just providing a list of potential candidates. We are committed to designing and implementing the most effective staffing strategy for you. Here is what you can expect when you choose Resource Employment Solutions as your recruiting and staffing partner.
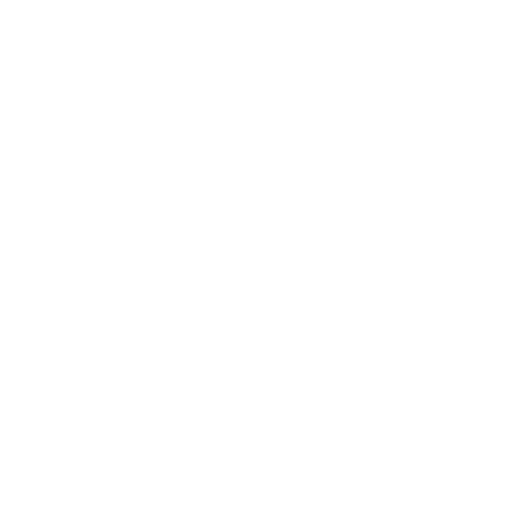
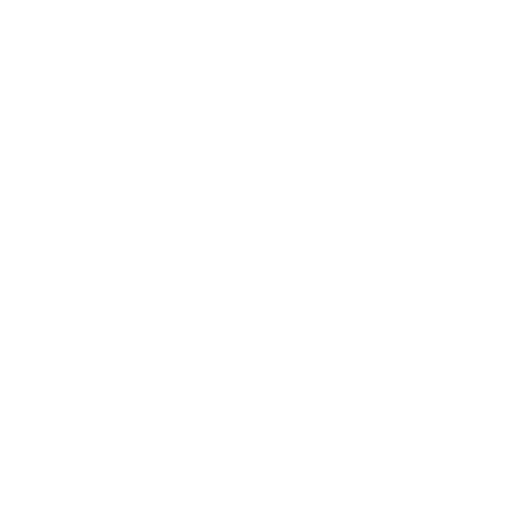
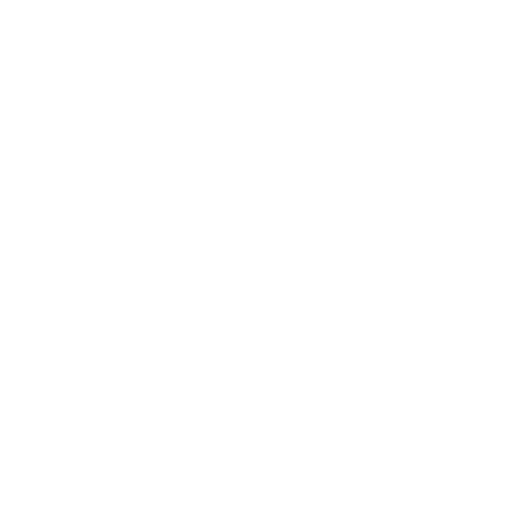
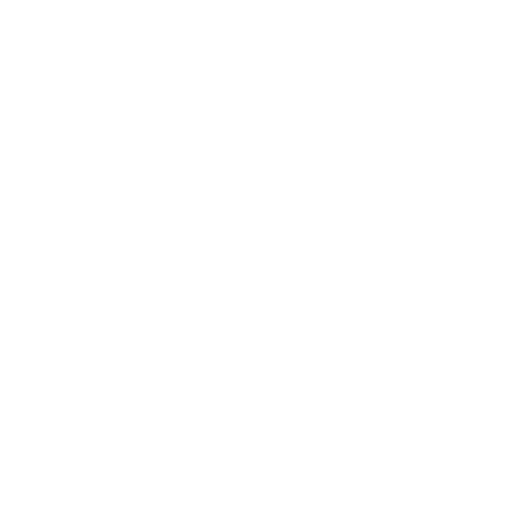
When you connect with Resource Employment Solutions, you will be matched with an account management team who specializes in placing top talent within your industry. You will have a dedicated recruiter or recruiting team assigned and they will remain your point of contact to understand your business and address all your staffing needs.
Frequently Asked Questions
It helps create a motivated workforce, reduces turnover, and enhances long-term operational efficiency.
Flexible work arrangements allow employees to manage their personal commitments, reducing stress and absenteeism, which leads to improved engagement and productivity.
A safe work environment fosters a sense of security, reducing workplace accidents and stress, which in turn boosts focus and productivity.