Building a Culture of Innovation in Manufacturing
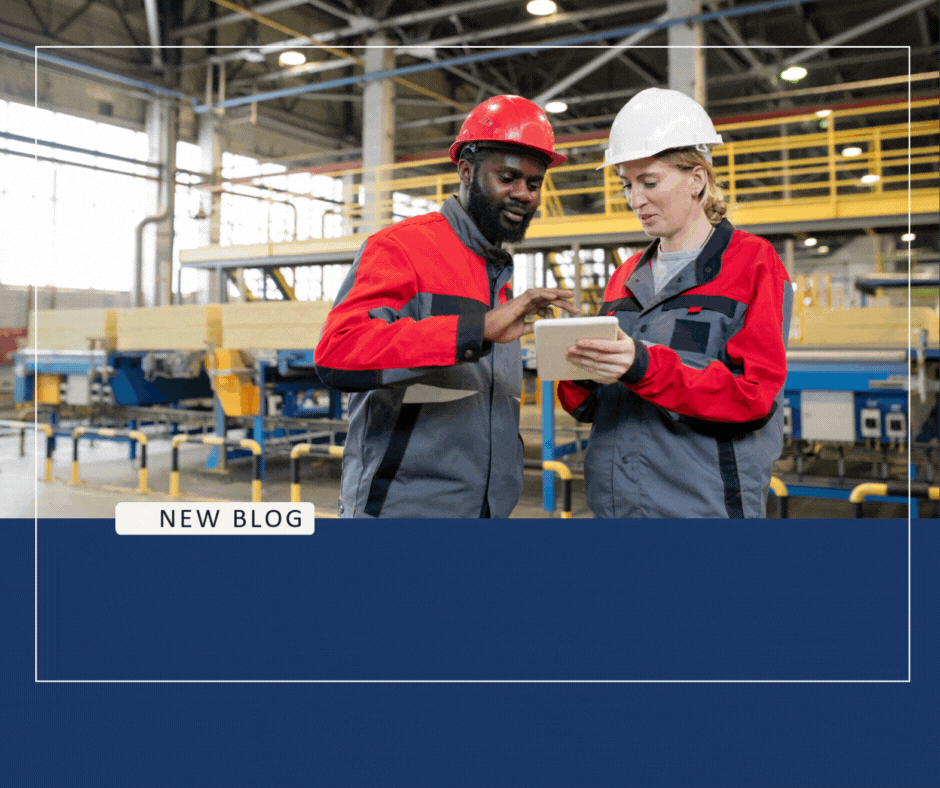
Innovation is the key to staying competitive in today’s manufacturing industry. But how do you create a culture that embraces new ideas and continuous improvement? From Illinois to Texas, manufacturers are discovering that fostering open communication, investing in employee development, and embracing technology are essential to driving innovation. By recognizing creative efforts, encouraging collaboration, and learning from failures, companies can build a thriving environment where employees feel empowered to contribute. Strong leadership and a focus on teamwork help reinforce this culture, ensuring long-term success. Ready to transform your manufacturing operations? Learn how building a culture of innovation can unlock new opportunities for growth and create a more engaged, productive workforce. Book your consultation with Resource Employment Solutions today!
In today’s fast-paced world, innovation is the driving force behind growth and sustainability in the manufacturing sector. As technology advances and market demands shift, manufacturers must embrace innovation not only in their products and processes but also within their workforce and company culture. A strong culture of innovation is essential to remain competitive, reduce operational costs, and meet customer expectations. Companies across key states like Illinois, New Jersey, North Carolina, Florida, Ohio, Texas, Georgia, Nevada, and Pennsylvania are recognizing the importance of fostering an environment that encourages creativity, continuous improvement, and forward-thinking.
Encouraging Open Communication and Idea Sharing
The foundation of any culture of innovation starts with open communication. Employees at all levels should feel comfortable sharing ideas, suggestions, and feedback. In manufacturing, where efficiency and productivity are key, it’s important to recognize that employees working on the production floor often have valuable insights into potential improvements. Creating an open-door policy where workers can voice their thoughts without fear of judgment encourages creative problem-solving.
One practical way to encourage communication is by holding regular team meetings or brainstorming sessions specifically focused on innovation. This provides employees with the space to propose new ideas, identify areas for improvement, and collaborate on solutions. Encouraging a dialogue between management and frontline workers ensures that all perspectives are heard and considered, which can lead to more successful innovation efforts.
Providing Ongoing Training and Development
Innovation doesn’t happen in a vacuum; it requires a workforce that is continually learning and growing. To build a culture of innovation, manufacturers need to invest in ongoing training and development programs. This might include training on new technologies such as automation, AI, or machine learning, as well as upskilling employees in areas like leadership, problem-solving, and project management.
When employees have the opportunity to develop new skills, they are more likely to feel empowered to think creatively and contribute to innovation initiatives. Training programs also signal to employees that the company is invested in their professional growth, which can improve morale and foster a sense of loyalty.
Embracing Technology and Automation
In today’s manufacturing landscape, technology is a critical component of innovation. Companies that adopt and integrate new technologies into their processes are better positioned to improve efficiency, reduce costs, and increase output. Automation, AI, and data analytics tools are transforming the way manufacturers operate, allowing for real-time decision-making, predictive maintenance, and more precise production techniques.
However, technology should not be viewed as a replacement for human input. Instead, it should complement the skills and expertise of the workforce. By integrating technology thoughtfully and involving employees in the process, manufacturers can drive innovation while also creating a more collaborative and future-focused environment.
Rewarding and Recognizing Innovative Efforts
To sustain a culture of innovation, manufacturers must recognize and reward those who contribute to creative problem-solving and process improvements. When employees see that their ideas are valued and rewarded, they are more likely to continue participating in innovation efforts. This recognition doesn’t always have to be financial; public acknowledgment, additional responsibilities, or opportunities for professional growth can also be highly motivating.
Creating formal programs or innovation challenges can help stimulate employee engagement. For example, manufacturers might implement a “suggestion box” system where employees can submit ideas, with the best ones receiving rewards or even being implemented company-wide. Such initiatives not only incentivize innovation but also foster a sense of ownership among employees.
Fostering a Collaborative Work Environment
Innovation thrives in collaborative environments. In manufacturing, different departments often operate in silos, which can stifle creativity and limit the potential for cross-functional innovation. To build a culture of innovation, manufacturers need to break down these barriers and encourage collaboration across teams, from engineering and production to sales and marketing.
Cross-functional collaboration allows employees to gain new perspectives and combine different areas of expertise, resulting in more innovative solutions. For instance, engineers working alongside production teams may identify ways to optimize machinery for greater efficiency, while sales teams may provide insights into market trends that can guide product development.
Building a Tolerance for Failure
Innovation requires taking risks, and with risk comes the possibility of failure. To foster a culture of innovation, manufacturers must build a tolerance for failure and view it as a learning opportunity rather than a setback. Employees should feel confident experimenting with new ideas, knowing that failure is part of the innovation process.
Encouraging experimentation and learning from mistakes helps employees refine their ideas and push boundaries. Leaders in manufacturing companies can set an example by being open about their own failures and demonstrating how to turn setbacks into valuable lessons for future success.
Leadership’s Role in Driving Innovation
Leadership plays a crucial role in establishing and maintaining a culture of innovation. Company leaders must not only talk about innovation but actively participate in and support innovative initiatives. Leaders who are visible, approachable, and open to new ideas can inspire their teams to think creatively and pursue new opportunities.
In states like Ohio, Florida, and Georgia, where manufacturing plays a significant role in the economy, leadership that fosters innovation is essential for maintaining competitiveness in a global market. By setting clear goals, allocating resources, and creating an environment that nurtures creativity, leaders can help ensure that innovation becomes a core part of the company’s culture.
Conclusion
Building a culture of innovation in manufacturing is essential for long-term success. By encouraging open communication, providing ongoing training, embracing technology, and fostering collaboration, manufacturers can create an environment where creativity thrives. Recognizing and rewarding innovative efforts, building a tolerance for failure, and having strong leadership are key components of sustaining this culture.
In competitive markets like Illinois, Texas, and New Jersey, manufacturers that prioritize innovation not only improve their operations but also create a more engaged and satisfied workforce. A culture of innovation doesn’t happen overnight, but with commitment and the right strategies, manufacturers can build a foundation that supports continuous improvement and growth. Book your consultation to get started with Resource Employment Solutions.
Written on behalf of RES.
The RES Onboarding Process
Our commitment to you is deeper than just providing a list of potential candidates. We are committed to designing and implementing the most effective staffing strategy for you. Here is what you can expect when you choose Resource Employment Solutions as your recruiting and staffing partner.
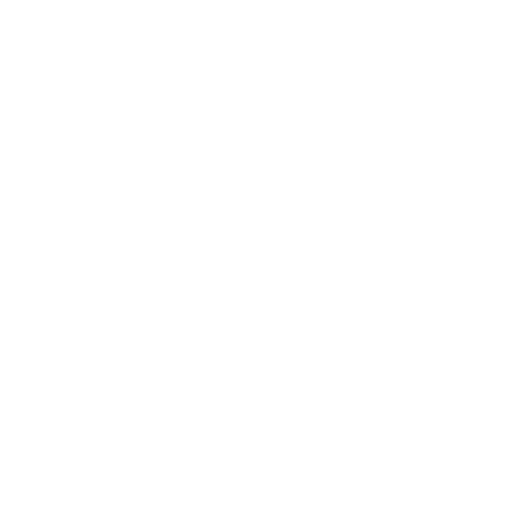
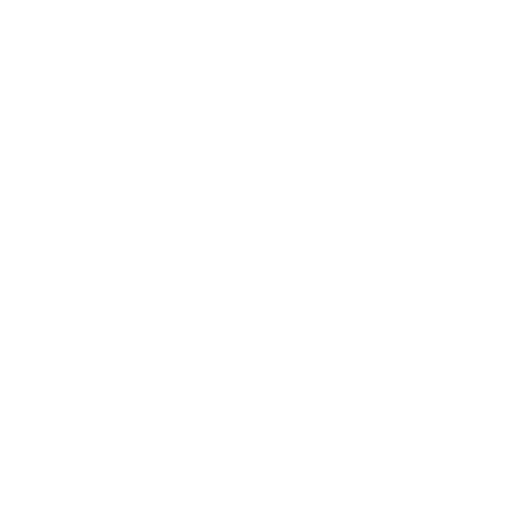
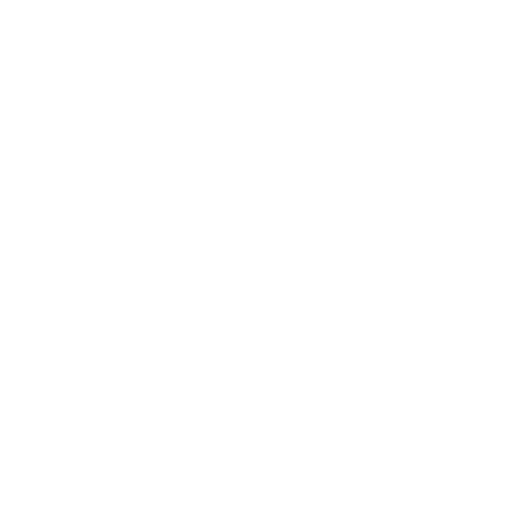
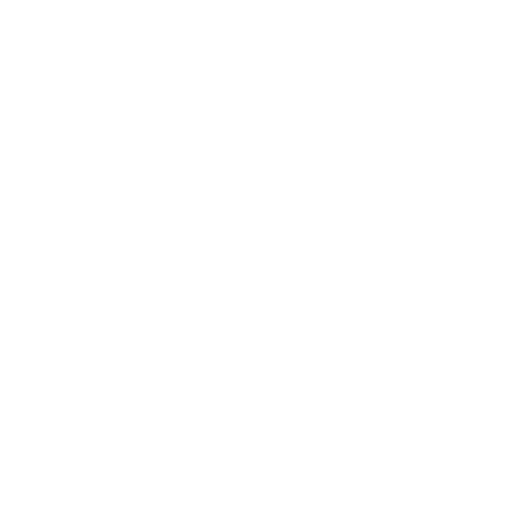
When you connect with Resource Employment Solutions, you will be matched with an account management team who specializes in placing top talent within your industry. You will have a dedicated recruiter or recruiting team assigned and they will remain your point of contact to understand your business and address all your staffing needs.
Frequently Asked Questions
Leadership sets the tone for innovation by supporting new ideas, providing resources, and creating an environment where employees feel empowered to experiment and take risks.
Manufacturers should encourage experimentation, view failures as learning opportunities, and support employees as they refine ideas, fostering a safe environment for innovation. Book a consultation to learn more!
Open idea-sharing allows for diverse perspectives, helps identify potential improvements, and encourages employees to contribute to the company’s growth and success.