Comprehensive Safety Plan for Manufacturing & Warehousing | RES
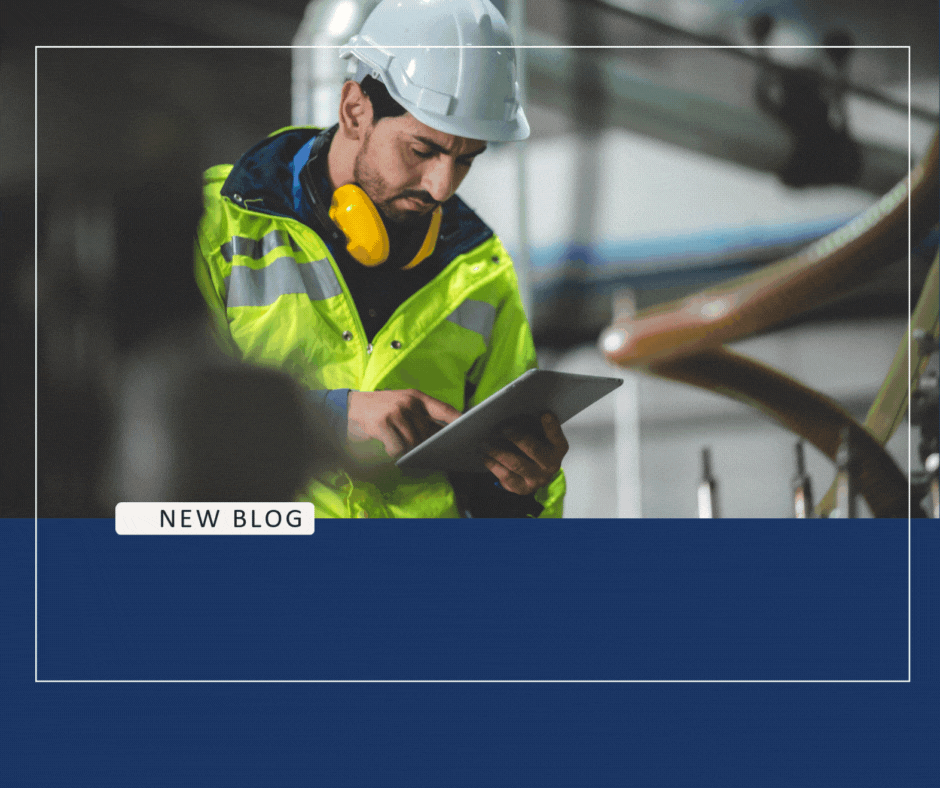
A comprehensive safety plan for manufacturing and warehousing is crucial for protecting employees and maintaining smooth operations. This article outlines three key components: risk assessment and hazard identification, robust training and education, and continuous safety monitoring and improvement. It highlights the importance of involving employees in hazard identification, providing engaging training formats, and using technology for ongoing safety evaluation. Effective safety programs not only meet regulatory requirements but also contribute to a safer, more efficient, and positive work environment. By prioritizing these elements, companies can reduce accidents, enhance employee morale, and create a culture of safety. Book your consultation with Resource Employment Solutions today!
Safety is the foundation of productivity and success in manufacturing and warehousing. For organizations operating in these high-stakes environments, a comprehensive safety plan isn’t just a regulatory obligation—it’s an essential strategy for protecting your workforce, maintaining operational continuity, and fostering a culture of trust and excellence. However, creating an effective safety program requires more than a one-size-fits-all approach; it demands careful planning, a deep understanding of industry-specific risks, and the ongoing commitment of all stakeholders.
At Resource Employment Solutions, we’ve seen firsthand the impact that a strong safety culture can have on workforce morale, retention, and performance. In this article, we’ll outline three key elements of a successful safety plan: risk assessment and hazard identification, robust training and education, and continuous safety monitoring and improvement. By implementing these strategies, companies can create safer environments that benefit both employees and the bottom line.
1. Risk Assessment and Hazard Identification
The first step in developing a comprehensive safety plan is to identify and assess potential hazards within the workplace. This process involves conducting thorough risk assessments to pinpoint both obvious and hidden dangers, such as heavy machinery, electrical equipment, ergonomic risks, and hazardous materials. An effective risk assessment should include input from employees who are intimately familiar with daily operations, as well as safety professionals who can provide an objective perspective.
For example, in a warehousing setting, forklifts are a well-known hazard. But beyond the risk of collisions, there may be additional dangers related to improper stacking, inadequate lighting, or congested aisles that aren’t immediately apparent. Similarly, in a manufacturing plant, routine processes like machine maintenance can pose serious safety threats if the proper lockout/tagout procedures aren’t in place.
To address these issues, companies should develop detailed safety checklists tailored to their specific operations and regularly update them as new processes, equipment, or personnel changes are introduced. Engaging employees in hazard identification not only helps capture a more comprehensive view of risks but also reinforces the message that safety is a shared responsibility.
2. Robust Training and Education
Once hazards are identified, the next critical element is to provide robust training and education tailored to the specific needs of the workforce. Effective training goes beyond a one-time onboarding session; it should be ongoing, interactive, and adapted to cover new safety protocols, evolving industry standards, and any changes in job responsibilities.
A common pitfall we’ve observed is the tendency for safety training to become repetitive and uninspired. To keep training engaging and impactful, companies should consider incorporating different formats, such as hands-on workshops, digital simulations, and scenario-based learning, which allow employees to practice responding to real-world situations in a controlled environment.
For example, a manufacturing company could implement a training program focused on safe equipment handling through the use of virtual reality (VR) technology. Employees can simulate operating heavy machinery and troubleshoot potential safety issues without the risk of injury. This kind of experiential learning not only improves knowledge retention but also boosts confidence and preparedness among the workforce.
3. Continuous Safety Monitoring and Improvement
Even the most comprehensive safety plans require ongoing evaluation and refinement. Continuous monitoring allows organizations to track the effectiveness of safety measures, identify new risks, and implement corrective actions before accidents occur. This can be achieved through regular safety audits, employee feedback mechanisms, and leveraging technology such as wearable devices and automated reporting systems.
For example, a company might use safety observation software to track trends in near-miss incidents, identify areas of concern, and develop targeted interventions. Similarly, implementing wearable technology like smart helmets or vests equipped with sensors can provide real-time data on employee movements and alert supervisors to potentially unsafe behaviors, such as improper lifting techniques or prolonged exposure to hazardous conditions.
Establishing a culture of continuous improvement means encouraging open communication about safety concerns and rewarding proactive behavior. A safety committee comprising representatives from different departments can serve as a central body for reviewing safety performance, addressing employee suggestions, and updating policies as needed.
Developing a comprehensive safety plan for manufacturing and warehousing is not just about meeting regulatory requirements—it’s about protecting the workforce, ensuring operational stability, and fostering a positive workplace culture. A strong safety program begins with thorough risk assessment, supported by robust training, and sustained through continuous monitoring and improvement. By focusing on these critical elements, companies can create safer, more efficient work environments where employees feel valued and empowered to perform at their best. Book your consultation to get started with Resource Employment Solutions.
Written on behalf of RES.
The RES Onboarding Process
Our commitment to you is deeper than just providing a list of potential candidates. We are committed to designing and implementing the most effective staffing strategy for you. Here is what you can expect when you choose Resource Employment Solutions as your recruiting and staffing partner.
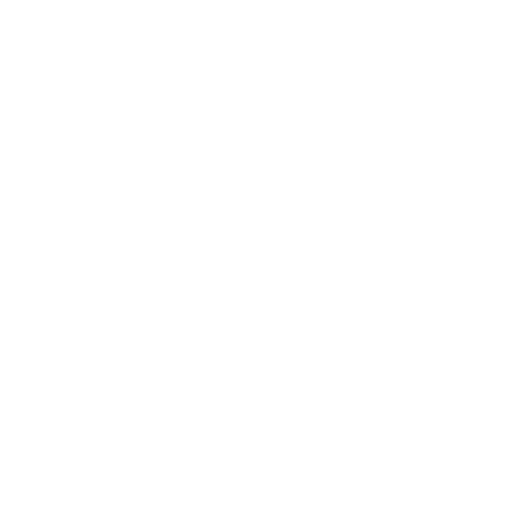
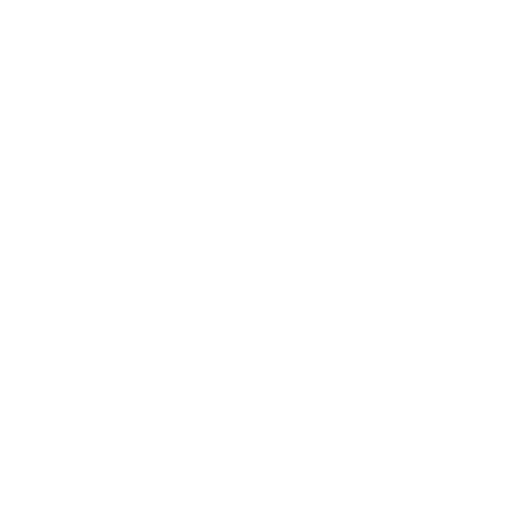
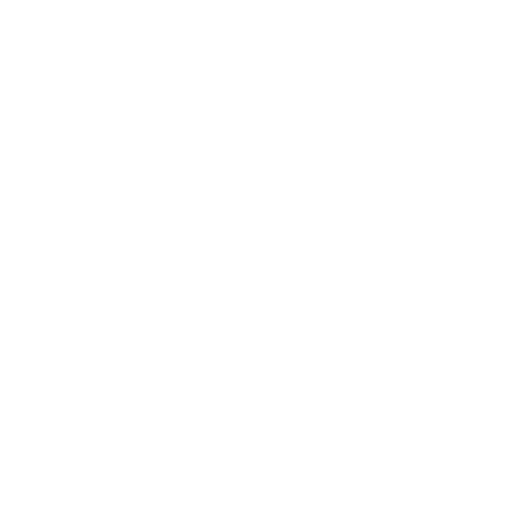
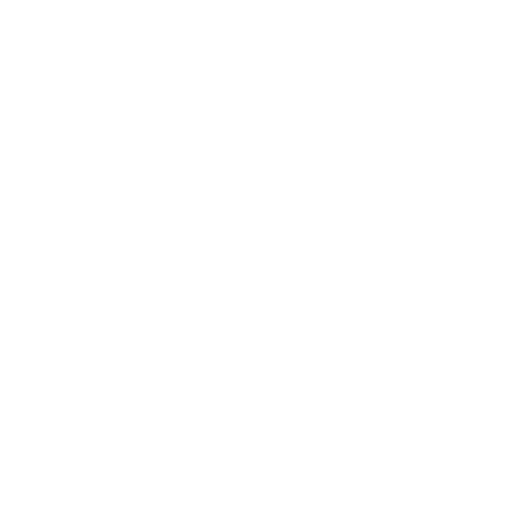
When you connect with Resource Employment Solutions, you will be matched with an account management team who specializes in placing top talent within your industry. You will have a dedicated recruiter or recruiting team assigned and they will remain your point of contact to understand your business and address all your staffing needs.
Frequently Asked Questions
The first step is conducting a thorough risk assessment and hazard identification to understand potential dangers in the workplace.
Safety training should be ongoing, not limited to onboarding. It should be refreshed regularly to address new protocols, equipment, and industry standards.
Interactive methods such as workshops, scenario-based learning, and digital simulations can make safety training more engaging and impactful.