Emerging Trends in Warehouse Automation: What You Need to Know | RES
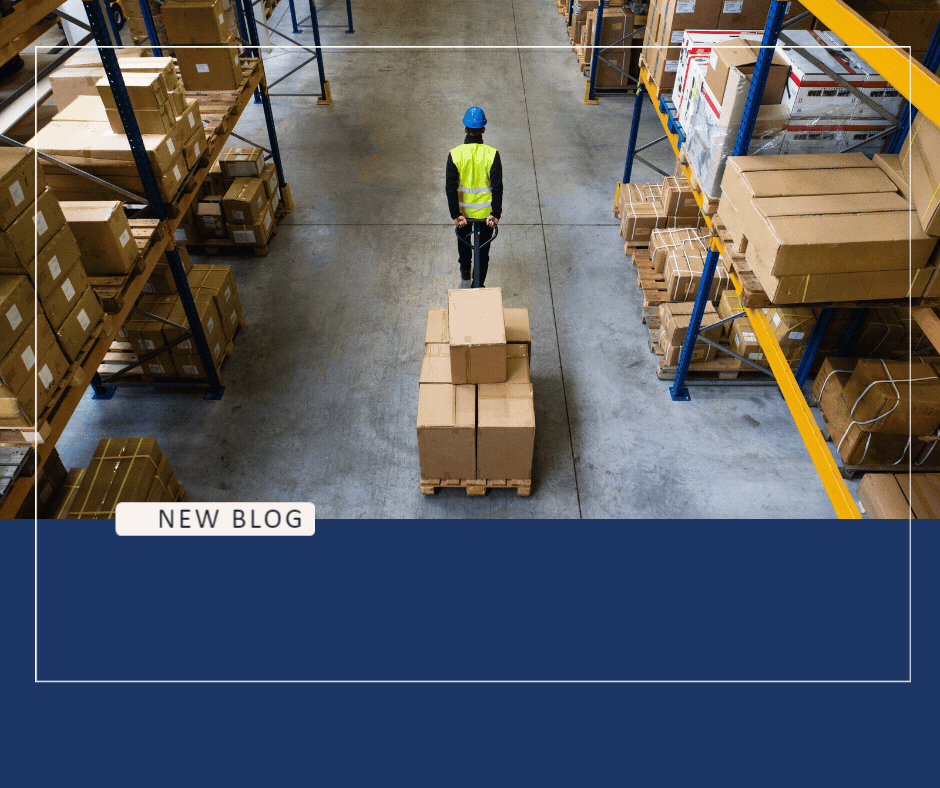
Warehouse automation is advancing rapidly, influenced by trends like Autonomous Mobile Robots (AMRs), Artificial Intelligence (AI), Machine Learning (ML), and Collaborative Robots (Cobots). AMRs enhance flexibility and efficiency, while AI and ML optimize operations by predicting demand and managing inventory. Cobots work alongside human employees, handling repetitive tasks to boost productivity. These technologies offer significant opportunities for increased efficiency, cost reduction, and scalability in warehouse operations. However, successful automation requires effective integration with a skilled workforce that can adapt to and collaborate with these innovations. Resource Employment Solutions can help businesses seamlessly incorporate these advanced technologies while ensuring their workforce is trained and ready to maximize the benefits of automation in the warehouse environment.
The rapid growth of e-commerce, increased consumer expectations, and global supply chain challenges have accelerated the adoption of automation in warehouses. Warehouse automation is no longer just about speeding up processes; it’s about transforming operations to be more efficient, scalable, and adaptive to future demands. By leveraging new technologies, companies can meet the increasing complexities of modern logistics while reducing costs and improving accuracy.
At Resource Employment Solutions, we understand that navigating these changes requires a skilled and adaptable workforce. In this article, we will explore three emerging trends in warehouse automation and how they are reshaping the industry. Each trend highlights the need for both advanced technology and a workforce that can work alongside these innovations.
1. Autonomous Mobile Robots (AMRs)
One of the most significant trends in warehouse automation is the use of Autonomous Mobile Robots (AMRs). Unlike traditional conveyor belts or fixed automation systems, AMRs are flexible, mobile, and can navigate around the warehouse independently. These robots are equipped with sensors and artificial intelligence (AI) to map out the warehouse environment and move goods from one location to another with precision.
For example, a large online retailer implemented AMRs to streamline order picking and inventory management. Previously, workers spent a significant portion of their time walking across the warehouse to retrieve items. By introducing AMRs, the retailer was able to reduce the walking distance for employees and improve order fulfillment times. Employees now focus on more complex tasks, while the robots handle repetitive movements and item transportation. This change led to a 30% increase in overall warehouse productivity.
AMRs are particularly beneficial for warehouses with fluctuating demand, as they can be easily scaled up or down based on operational needs. They also allow for more efficient use of space, making it easier to adapt to changing inventory levels without the need for large-scale infrastructure changes.
2. Artificial Intelligence and Machine Learning
Artificial Intelligence (AI) and Machine Learning (ML) are increasingly being integrated into warehouse management systems (WMS). These technologies enable warehouses to predict demand, optimize routes, manage inventory levels, and even automate decision-making processes. AI-powered systems can analyze large datasets and make adjustments in real-time to ensure that operations run smoothly and efficiently.
For example, a global logistics company incorporated AI and ML algorithms into its warehouse management system to optimize inventory placement. By analyzing historical data on order patterns, shipping times, and seasonal trends, the system was able to predict which products would be in high demand and adjust the layout of the warehouse accordingly. As a result, picking times were reduced by 25%, and stockouts decreased significantly, as the system proactively managed inventory levels.
AI and ML can also improve labor management by predicting labor needs based on historical patterns and real-time data, allowing warehouses to optimize staffing levels and reduce operational costs.
3. Collaborative Robots (Cobots)
Collaborative robots, or "cobots," are designed to work alongside human employees, enhancing their productivity rather than replacing them. Cobots can handle repetitive and physically demanding tasks, such as lifting heavy items or packaging products, allowing employees to focus on more complex and value-added activities. Unlike traditional robots, cobots are equipped with advanced sensors to safely operate in the same workspace as humans, making them ideal for warehouses with diverse operational needs.
For example, a manufacturing company introduced cobots to assist with packing and sorting products. The cobots worked alongside employees, taking over repetitive tasks like stacking boxes and organizing items for shipment. This reduced the physical strain on workers and allowed them to concentrate on quality control and process improvement. The introduction of cobots led to a significant reduction in employee injuries and a 15% increase in overall output.
Cobots are highly adaptable and can be easily programmed to perform various tasks. Their collaborative nature allows them to be deployed in environments where human workers and automation need to coexist seamlessly.
Warehouse automation is transforming how companies manage operations, with technologies like Autonomous Mobile Robots (AMRs), Artificial Intelligence (AI), Machine Learning (ML), and Collaborative Robots (Cobots) leading the way. These innovations offer the potential to significantly improve efficiency, reduce costs, and create more flexible and scalable operations. However, the success of these technologies depends on effectively integrating them with a skilled and adaptable workforce.
As warehouses adopt more advanced automation, the balance between human expertise and technology will become increasingly important. Employees will need to collaborate with robots and AI systems, ensuring that operations remain smooth and efficient. By focusing on both technological advancements and workforce readiness, companies can position themselves for long-term success in an evolving industry.
Written on behalf of RES.
The RES Onboarding Process
Our commitment to you is deeper than just providing a list of potential candidates. We are committed to designing and implementing the most effective staffing strategy for you. Here is what you can expect when you choose Resource Employment Solutions as your recruiting and staffing partner.
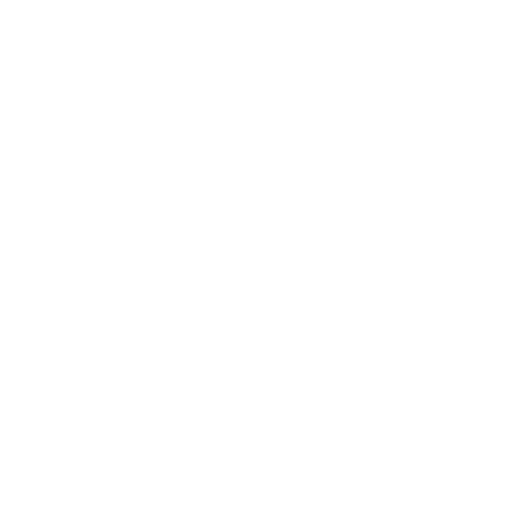
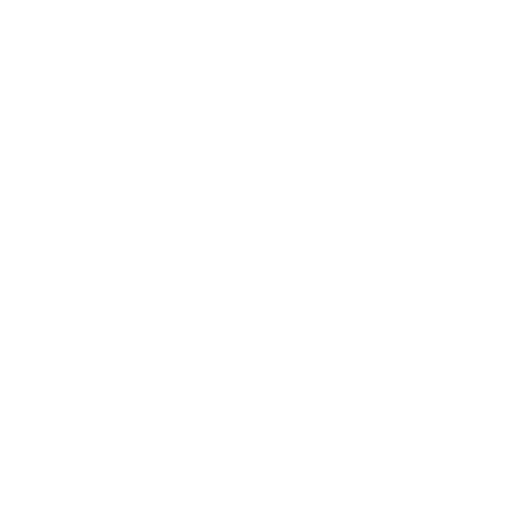
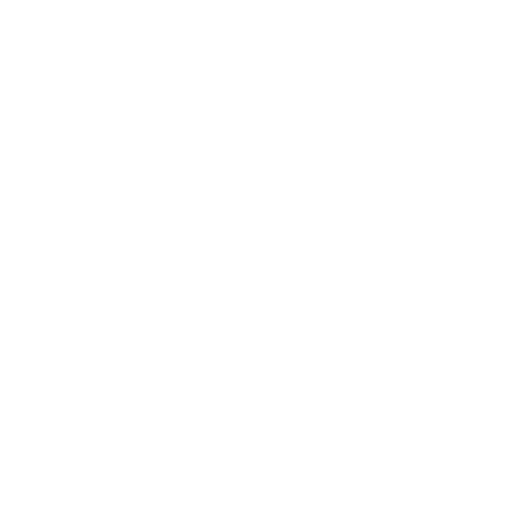
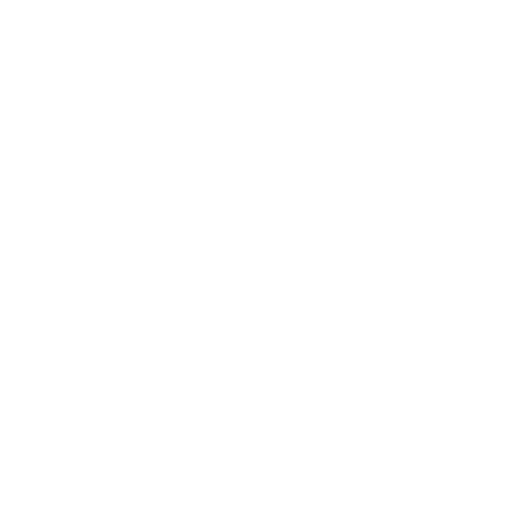
When you connect with Resource Employment Solutions, you will be matched with an account management team who specializes in placing top talent within your industry. You will have a dedicated recruiter or recruiting team assigned and they will remain your point of contact to understand your business and address all your staffing needs.
Frequently Asked Questions
AMRs are robots that navigate warehouses independently, transporting goods and improving efficiency.
AI optimizes operations by predicting demand, managing inventory, and automating decision-making.
Machine Learning analyzes data patterns to optimize inventory placement, predict demand, and streamline workflows.