Evaluating the Impact of Remote Work on Manufacturing Efficiency | RES
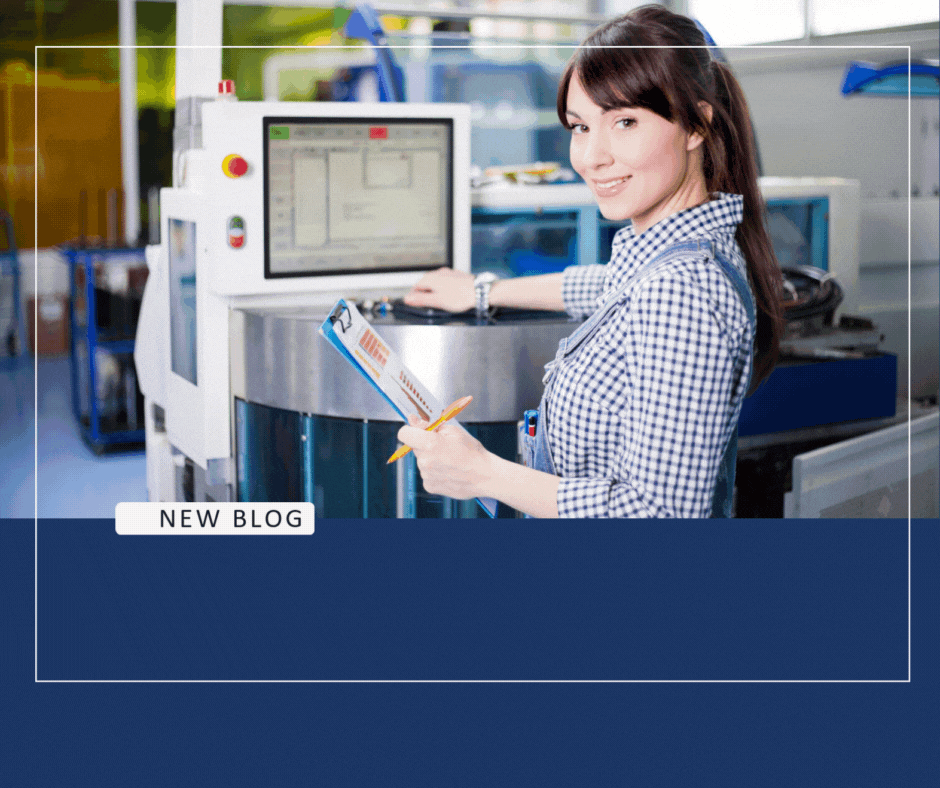
The article explores the impact of remote work on manufacturing efficiency, highlighting both its benefits and challenges. It discusses how remote teams can improve maintenance and reduce downtime through the use of real-time monitoring and predictive maintenance tools. The article also covers how remote work enables better production planning and data-driven decision-making, enhancing overall efficiency. However, it also addresses the challenges of maintaining team cohesion and ensuring effective communication between remote and on-site staff. Solutions include setting up clear communication protocols and using collaborative platforms to keep everyone aligned. Ultimately, a thoughtful approach is essential to harness the full potential of remote work in manufacturing while mitigating potential drawbacks. Book your consultation with Resource Employment Solutions today!
The manufacturing sector, historically characterized by its need for on-site, hands-on operations, has faced a rapid shift in recent years. With the rise of remote work, companies are exploring how flexible working arrangements can be integrated into an industry that was once considered incompatible with such a model. From remote supervision and equipment monitoring to production planning, manufacturers are finding new ways to leverage remote capabilities to maintain, and even improve, efficiency. However, remote work also brings unique challenges that need to be carefully managed to ensure that productivity and quality are not compromised.
At Resource Employment Solutions, we understand the complexities of balancing traditional and remote work models in manufacturing. With thoughtful implementation, remote work can support manufacturing efficiency, reduce operational costs, and improve employee satisfaction. Below, we evaluate the impact of remote work on three critical areas of manufacturing efficiency.
1. Improved Maintenance and Downtime Management
One of the greatest benefits of remote work in manufacturing is the ability to enhance equipment maintenance and minimize downtime. Remote teams can now leverage technology such as IoT sensors, predictive maintenance software, and real-time monitoring systems to keep a constant eye on equipment performance. This allows maintenance technicians to identify potential issues before they become costly problems and, in some cases, resolve them without being physically present.
For example, a heavy machinery manufacturer implemented a remote monitoring system that allowed technicians to assess machine performance from anywhere. By setting up alerts for unusual vibrations or temperature changes, the remote team could proactively address issues before a breakdown occurred. This reduced equipment downtime by 30% over the course of a year, saving the company significant costs associated with unplanned maintenance and production halts.
In this scenario, remote work not only increased efficiency but also contributed to better resource utilization, as fewer technicians were needed on-site for constant supervision. This model can also be extended to multi-site operations, where remote teams can oversee maintenance for several facilities simultaneously.
2. Enhanced Production Planning and Data-Driven Decision Making
Remote work has opened up new opportunities for integrating advanced data analytics and production planning tools into manufacturing operations. By enabling key team members to work remotely, companies can leverage data insights more effectively, making informed decisions that enhance overall production efficiency.
For example, a mid-sized electronics manufacturer transitioned its production planning team to a remote setup using a cloud-based Enterprise Resource Planning (ERP) system. The remote team could access real-time production data, monitor inventory levels, and adjust schedules to optimize output based on demand fluctuations. As a result, the manufacturer saw a 15% reduction in production lead times and a 20% decrease in excess inventory costs.
The ability to perform data analysis remotely and adjust production strategies in real time gives manufacturers a competitive advantage. Remote work allows companies to access a broader talent pool, bringing in specialized data analysts who can work from anywhere, enhancing the decision-making process.
3. Challenges in Maintaining Team Cohesion and On-Site Coordination
Despite the benefits, remote work in manufacturing comes with challenges, particularly in maintaining team cohesion and ensuring effective on-site coordination. Unlike other industries, manufacturing often requires close collaboration between remote and on-site staff. Miscommunication or delays in relaying information can lead to disruptions, impacting both efficiency and safety.
For example, a food processing company that had partially transitioned to remote management faced challenges in synchronizing its remote quality assurance team with on-site production supervisors. Initial lapses in communication led to minor quality control issues and slower response times. To address this, the company introduced daily video check-ins, shared digital logs, and a collaborative platform to streamline communication between remote and on-site staff. These changes led to improved response times and a smoother production workflow, ultimately increasing efficiency by 10%.
This example highlights the importance of establishing clear communication protocols and using the right technology to bridge the gap between remote and on-site teams. For remote work to contribute positively to efficiency, it’s crucial to ensure that remote employees have the same level of visibility and access to information as those on the shop floor.
The impact of remote work on manufacturing efficiency varies depending on how well it’s integrated into existing processes. While it offers significant benefits, such as minimizing equipment downtime and enabling better data-driven decision-making, it also presents challenges in communication and coordination. Successful implementation requires a thoughtful approach that considers the unique demands of the manufacturing environment. With careful planning, manufacturers can balance on-site operations with remote capabilities to create a more resilient and efficient workforce, allowing them to stay competitive in an increasingly flexible work landscape. As the industry continues to evolve, understanding how to best leverage remote work will be key to maintaining operational excellence. Book your consultation to get started with Resource Employment Solutions.
Written on behalf of RES.
The RES Onboarding Process
Our commitment to you is deeper than just providing a list of potential candidates. We are committed to designing and implementing the most effective staffing strategy for you. Here is what you can expect when you choose Resource Employment Solutions as your recruiting and staffing partner.
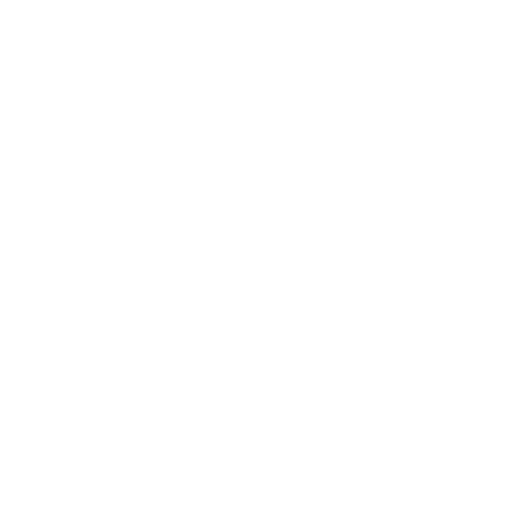
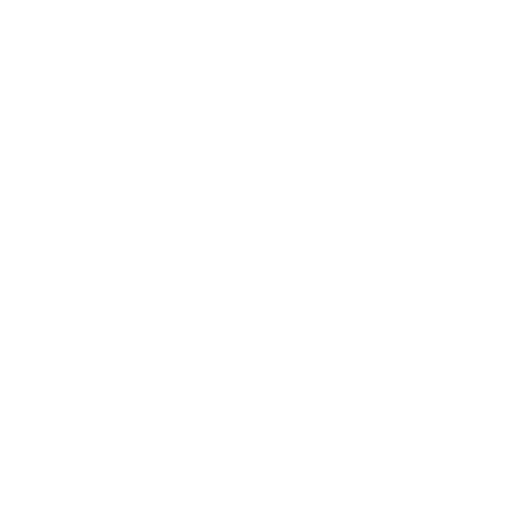
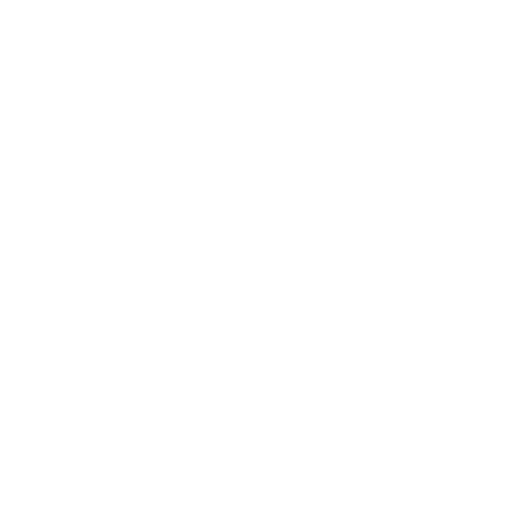
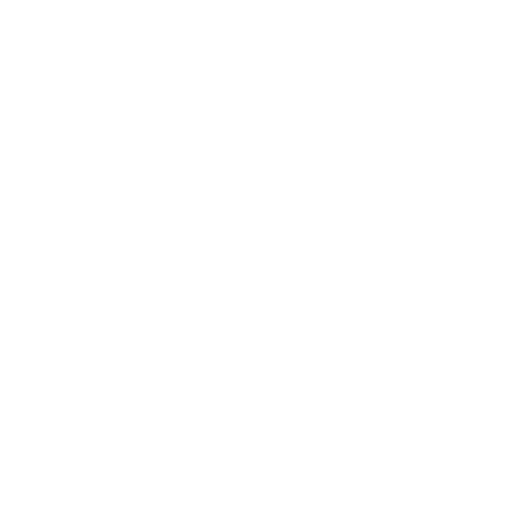
When you connect with Resource Employment Solutions, you will be matched with an account management team who specializes in placing top talent within your industry. You will have a dedicated recruiter or recruiting team assigned and they will remain your point of contact to understand your business and address all your staffing needs.
Frequently Asked Questions
Yes, remote work can be effective for certain functions, such as maintenance monitoring, production planning, and data analysis. With the right technology and communication strategies, remote teams can contribute to overall efficiency and productivity.
Remote work can help reduce equipment downtime through predictive maintenance, enhance production planning through real-time data analysis, and allow access to specialized talent regardless of location. It also promotes flexibility and can reduce operational costs.
Maintaining effective communication, ensuring real-time collaboration between remote and on-site staff, and keeping remote employees engaged and connected to the team are some of the main challenges in a manufacturing setting.