Future Trends in Manufacturing Staffing | RES
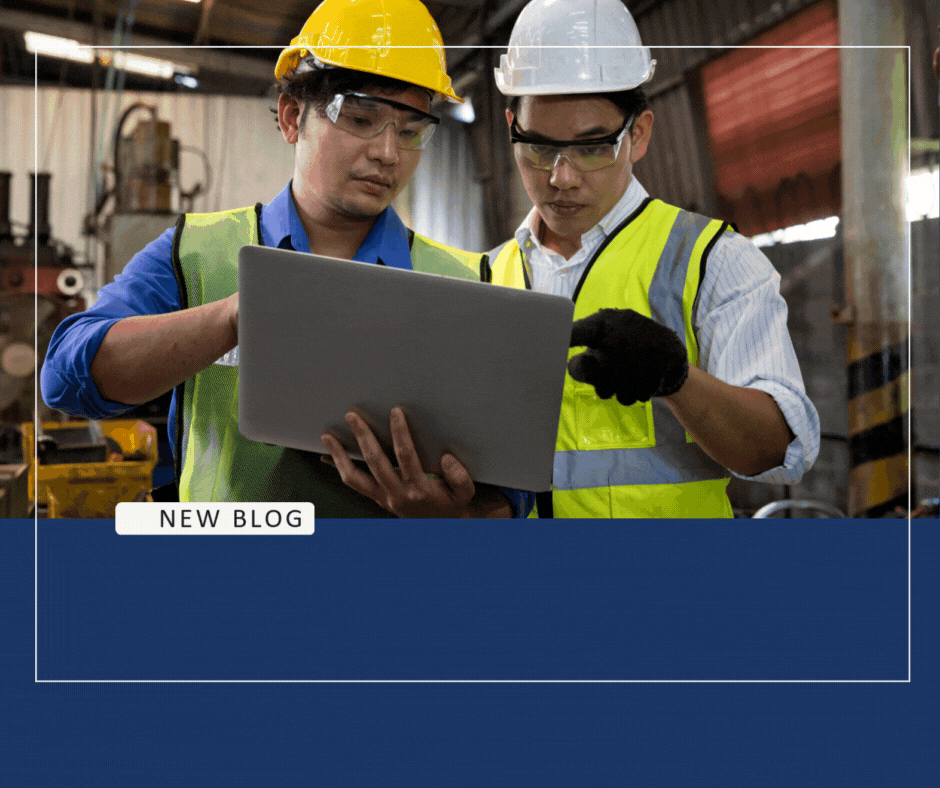
The future of manufacturing staffing is being shaped by emerging trends such as automation, the need for specialized skills, and increased demand for flexible work arrangements. As companies integrate smart factory technologies, they will require employees with technical expertise to manage automated systems and interpret complex data. Additionally, roles like automation engineers and data analysts are becoming critical as manufacturing becomes more complex. Meanwhile, digital tools and remote monitoring are enabling more flexibility in traditionally shift-based environments. To adapt to these changes, companies must focus on upskilling, proactive recruitment, and exploring new ways of working to stay ahead in an evolving industry landscape. Book your consultation with Resource Employment Solutions today!
The manufacturing industry is on the cusp of significant transformation, driven by advancements in technology, changing workforce demographics, and shifting market demands. As a result, the future of manufacturing staffing is evolving rapidly, and businesses must be prepared to adapt to these emerging trends to stay competitive. For manufacturing companies, building a resilient and future-ready workforce requires more than simply filling positions—it’s about strategic planning, embracing innovation, and anticipating changes in the labor market.
At Resource Employment Solutions, we have seen firsthand how proactive workforce planning can make the difference between thriving in a changing landscape and struggling to keep up. This article will explore three major trends shaping the future of manufacturing staffing: the rise of automation and smart factories, the growing demand for specialized skill sets, and the shift towards flexible work arrangements. By understanding and preparing for these trends, companies can better position themselves for long-term success.
1. The Rise of Automation and Smart Factories
One of the most impactful trends in manufacturing is the rise of automation and the adoption of smart factory technologies. As industries continue to integrate robotics, AI, and Internet of Things (IoT) systems into their production processes, the demand for traditional manufacturing roles is shifting. Instead of primarily manual roles, companies are seeking individuals who can work alongside these new technologies, manage automated systems, and leverage data to optimize production.
For example, in a smart factory, machines equipped with sensors can automatically adjust production parameters based on real-time data, reducing waste and increasing efficiency. This technological shift means that many manufacturing roles now require a blend of technical expertise and critical thinking skills. Workers need to be comfortable using digital tools, interpreting complex data, and troubleshooting automated systems.
To prepare for this trend, companies should focus on upskilling their existing workforce and hiring candidates with strong technical backgrounds. Investing in training programs for current employees can help bridge the gap between traditional manufacturing skills and the competencies needed in an automated environment. Additionally, partnering with educational institutions to create specialized programs can help develop a talent pipeline equipped for the demands of smart manufacturing.
2. The Growing Demand for Specialized Skill Sets
As manufacturing processes become more complex and technologically advanced, the need for specialized skill sets is increasing. While automation handles repetitive tasks, humans are still required for roles that involve creativity, strategic planning, and high-level problem-solving. Positions such as automation engineers, data analysts, and robotics specialists are becoming crucial in the manufacturing sector.
For instance, a manufacturing plant that introduces predictive maintenance systems needs data analysts who can interpret equipment performance data and identify potential issues before they result in downtime. Similarly, the rise of custom manufacturing and 3D printing requires engineers with expertise in digital design and production planning.
To address this growing demand, companies should adopt a proactive approach to talent acquisition, focusing on attracting individuals with these niche skills. This may involve expanding recruitment efforts beyond traditional sources, such as targeting candidates from tech industries or providing internship opportunities to students specializing in engineering and data science. Creating a strong employer brand that emphasizes innovation and career development can also help attract top talent in these areas.
3. The Shift Towards Flexible Work Arrangements
The nature of work itself is changing, and manufacturing is no exception. Traditionally seen as a rigid, shift-based industry, manufacturing is beginning to embrace more flexible work arrangements in response to employee expectations and broader societal trends. The rise of remote monitoring technologies and digital collaboration tools has made it possible for some manufacturing roles, such as production planning or quality assurance, to be conducted partially or fully remotely.
For example, during the COVID-19 pandemic, many manufacturers implemented remote management systems to monitor equipment performance and production metrics without requiring on-site presence. This experience demonstrated that certain tasks could be performed outside the physical factory floor, paving the way for more flexible work options.
Companies that offer flexible schedules, part-time roles, or remote work options for suitable positions can better attract and retain talent, especially among younger workers who prioritize work-life balance. Implementing flexibility where possible also helps mitigate the impact of workforce shortages by making roles more appealing to a broader range of candidates, including those who may not be able to commit to traditional shift work.
The landscape of manufacturing staffing is undergoing significant change, driven by technological advancements, evolving skill requirements, and shifting workplace expectations. By recognizing trends such as the rise of automation and smart factories, the growing demand for specialized skill sets, and the movement toward flexible work arrangements, companies can gain a clearer understanding of where the industry is headed. Preparing for these changes means not just adapting to new technologies, but also rethinking traditional approaches to recruitment, training, and employee engagement. As the industry continues to transform, having a forward-looking staffing strategy will help manufacturing organizations remain agile and responsive to whatever the future holds. Book your consultation to get started with Resource Employment Solutions.
Written on behalf of RES.
The RES Onboarding Process
Our commitment to you is deeper than just providing a list of potential candidates. We are committed to designing and implementing the most effective staffing strategy for you. Here is what you can expect when you choose Resource Employment Solutions as your recruiting and staffing partner.
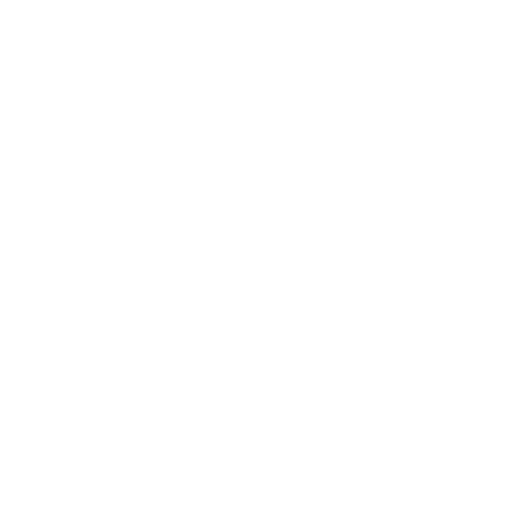
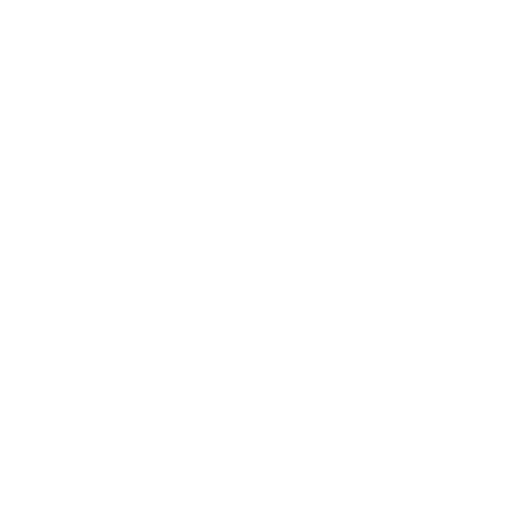
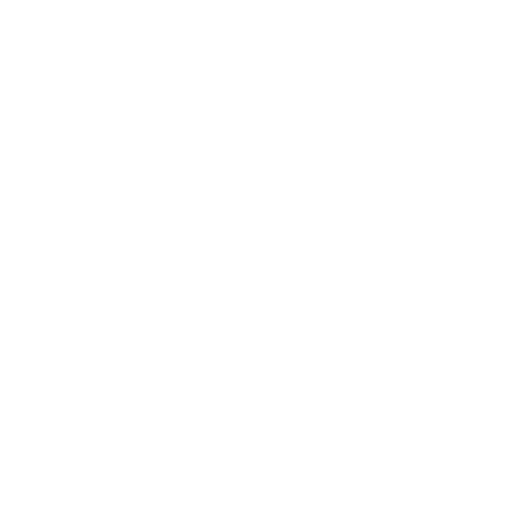
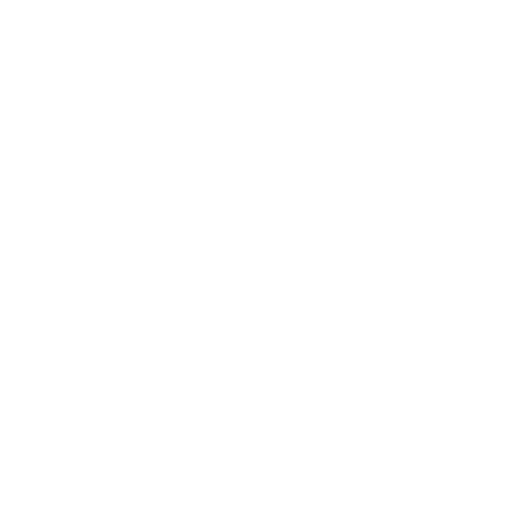
When you connect with Resource Employment Solutions, you will be matched with an account management team who specializes in placing top talent within your industry. You will have a dedicated recruiter or recruiting team assigned and they will remain your point of contact to understand your business and address all your staffing needs.
Frequently Asked Questions
Key drivers include automation, advanced technologies, and shifting workforce expectations for flexibility and specialized skill sets.
Smart factories integrate technologies like AI, IoT, and robotics, requiring workers with technical skills to manage, maintain, and optimize these systems.
As manufacturing processes become more complex, roles that involve data analysis, robotics, and digital design are crucial for innovation and efficiency.