How to Create Effective Training Programs for Manufacturing Employees

Looking to boost productivity & safety in your manufacturing operations? The key lies in effective employee training. Whether you're in Illinois, Texas, or Pennsylvania, creating tailored training programs can make all the difference. From assessing your workforce’s needs to incorporating hands-on learning & technology, manufacturers can equip their teams with the skills needed to thrive. Prioritizing safety, offering continuous learning opportunities, & recognizing progress are crucial steps toward building a motivated, well-prepared workforce. Want to stay ahead of industry demands & ensure your employees are ready for anything? Discover how strategic training programs can elevate your operations & lead to long-term success in today’s competitive market. Ready to build a stronger, more skilled team? Book your consultation with Resource Employment Solutions today!
In the manufacturing sector, the skills and knowledge of employees are critical to the success of a company. Effective training programs ensure that workers are equipped to handle the demands of their roles, keep up with advancing technology, and follow safety protocols. Whether it’s a new hire onboarding process or continuous development for seasoned employees, creating a structured and practical training program is essential. In states like Illinois, New Jersey, North Carolina, Florida, Ohio, Texas, Georgia, Nevada, and Pennsylvania, manufacturing businesses must focus on building training programs that drive productivity, maintain compliance, and enhance employee satisfaction.
Start with a Needs Assessment
Before creating any training program, it’s crucial to understand the specific needs of your workforce. A needs assessment helps identify gaps in skills, knowledge, and performance. For example, are your employees struggling with new technologies, or are safety violations becoming more frequent? By conducting surveys, reviewing performance metrics, or interviewing employees and supervisors, you can pinpoint areas where training is most needed.
For manufacturers in Ohio or Georgia, where there’s a growing focus on automation, a needs assessment might reveal a need for more technical training on how to operate new machinery. On the other hand, in states like Pennsylvania and Florida, safety training might be prioritized to meet state regulations. Tailoring your program to the specific needs of your business ensures that training is relevant and impactful.
Develop Clear Learning Objectives
Once you’ve identified the areas where training is needed, the next step is to define clear learning objectives. These objectives should be specific and measurable, outlining what employees should be able to do after completing the training. Clear objectives help guide the development of the program and provide employees with a sense of direction.
For instance, if the goal is to improve machine operation efficiency in a Texas-based manufacturing plant, a clear learning objective might be: "Employees will demonstrate the ability to operate X machine with a 20% reduction in downtime." Having such specific goals keeps the training focused and allows you to measure its effectiveness.
Use a Blend of Training Methods
Different employees learn in different ways, so it’s important to offer a variety of training methods. In manufacturing, hands-on learning is often the most effective, allowing employees to practice using machines or equipment in real-world situations. However, supplementing hands-on training with classroom-style learning or e-learning modules can provide a more comprehensive experience.
For example, manufacturers in New Jersey or Nevada, where new compliance laws are introduced regularly, might use a combination of online compliance training and in-person workshops to ensure employees fully understand the changes. A blended approach ensures that all employees, regardless of their learning style, can benefit from the training program.
Prioritize Safety Training
Safety is a top concern in the manufacturing industry, and an effective training program should prioritize it. Whether it’s general workplace safety, machine-specific protocols, or emergency response procedures, comprehensive safety training helps reduce workplace injuries and ensures compliance with state and federal regulations.
In North Carolina and Florida, where safety regulations vary, it’s important to customize training to local requirements. Hands-on simulations, interactive sessions, and regular refresher courses can help ensure that safety becomes second nature to employees. This not only protects workers but also boosts morale by showing that their well-being is a priority.
Make Training Continuous
Training shouldn’t be a one-time event. Continuous training ensures that employees stay updated on the latest technologies, regulations, and best practices. Offering ongoing opportunities for learning helps employees adapt to changes in the industry and improve their skills over time.
Manufacturers in fast-evolving states like Illinois and Texas, where technology is quickly advancing, can benefit from regular workshops, online courses, or mentorship programs that keep employees engaged and constantly learning. Regularly updated training programs prevent skill stagnation and ensure your workforce stays competitive.
Incorporate Feedback and Evaluation
An effective training program is one that evolves based on feedback. After each training session, collect feedback from participants to understand what worked well and what could be improved. Employee surveys, one-on-one discussions, and even performance data can provide valuable insights into how the training program is performing.
In Ohio and Georgia, where manufacturing operations can be highly specialized, feedback might highlight the need for more targeted training in certain areas. Regular evaluations of your program also ensure that it continues to meet the changing needs of your business and industry.
Leverage Technology for Training Efficiency
Incorporating technology into your training program can enhance its effectiveness and efficiency. Online learning platforms, virtual reality (VR) simulations, and mobile apps can provide employees with flexible and engaging ways to complete training. In states like Nevada and Pennsylvania, where manufacturers may be adopting new technology or expanding operations, leveraging tech-based training solutions can help streamline the process.
For example, VR simulations can give employees a safe, hands-on way to practice operating complex machinery without disrupting production. Mobile apps can make it easy for employees to access training materials on the go, ensuring that learning is integrated into their daily routines.
Recognize and Reward Progress
Employee motivation plays a key role in the success of any training program. Recognizing and rewarding progress can encourage employees to engage more deeply in the learning process. Whether it’s verbal recognition, certificates of completion, or incentives like bonuses or promotions, acknowledging employees’ efforts shows that their development is valued.
For manufacturers in Texas, New Jersey, or Florida, incorporating rewards into the training program can boost participation and create a positive learning environment. When employees feel appreciated, they’re more likely to take ownership of their learning and apply their new skills on the job.
Conclusion
Creating effective training programs for manufacturing employees is an ongoing process that requires careful planning, clear objectives, and continuous improvement. By understanding the unique needs of your workforce, using a blend of training methods, prioritizing safety, and leveraging technology, manufacturers across states like Illinois, Texas, and Ohio can ensure their employees are well-prepared to succeed.
Continuous training, regular feedback, and recognition are essential for keeping employees engaged and motivated. With the right strategies in place, your training program can lead to a safer, more skilled, and more productive workforce, helping your business thrive in a competitive market. Book your consultation to get started with Resource Employment Solutions.
Written on behalf of RES.
The RES Onboarding Process
Our commitment to you is deeper than just providing a list of potential candidates. We are committed to designing and implementing the most effective staffing strategy for you. Here is what you can expect when you choose Resource Employment Solutions as your recruiting and staffing partner.
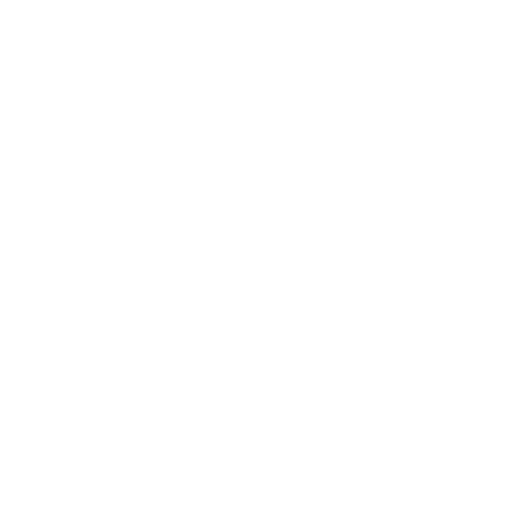
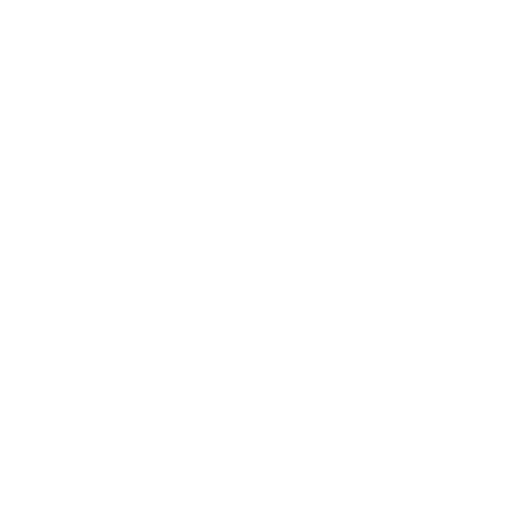
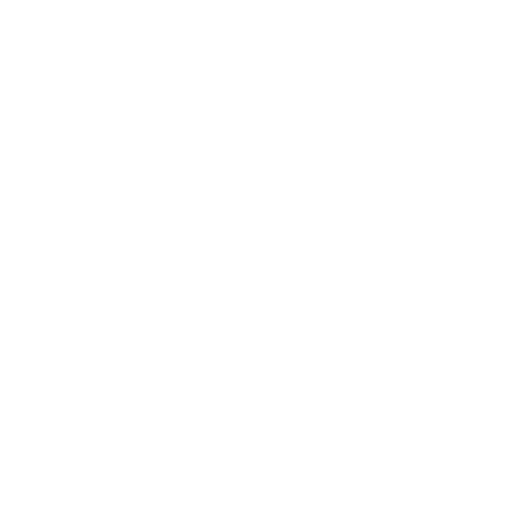
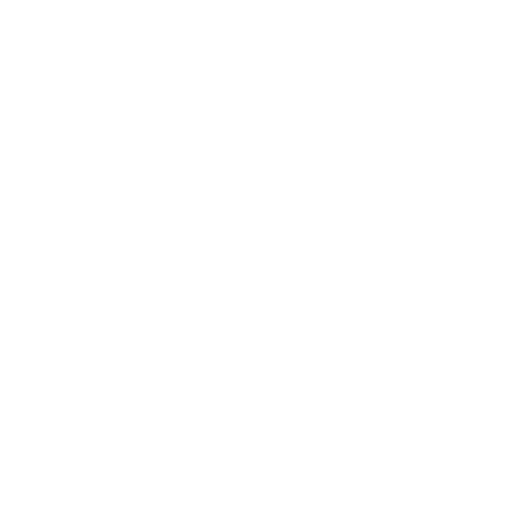
When you connect with Resource Employment Solutions, you will be matched with an account management team who specializes in placing top talent within your industry. You will have a dedicated recruiter or recruiting team assigned and they will remain your point of contact to understand your business and address all your staffing needs.
Frequently Asked Questions
A needs assessment, using surveys, performance reviews, and feedback from supervisors, helps identify skill gaps and areas for improvement within the workforce.
Hands-on learning, classroom-style education, e-learning modules, and virtual reality simulations can all be used to provide comprehensive training. Book a consultation to learn more!
By offering regular workshops, online courses, and mentorship opportunities, manufacturers can keep employees updated on new skills and technologies.