How to Enhance Team Collaboration in Manufacturing | RES
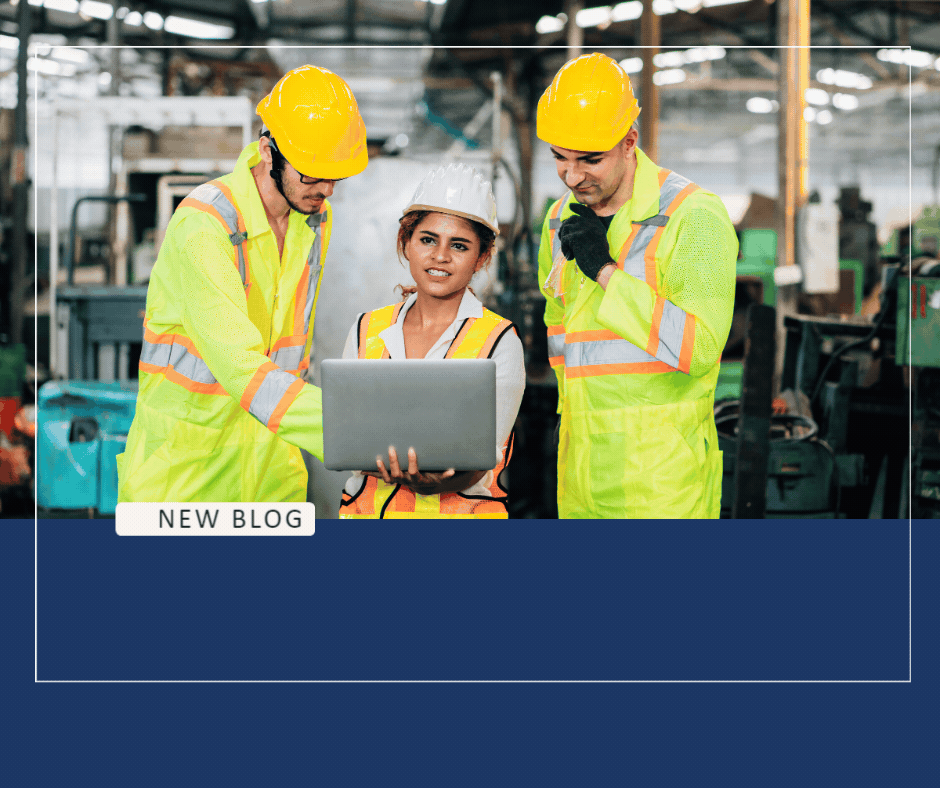
Improving team collaboration in manufacturing is essential for boosting efficiency, reducing errors, and building a more united workforce. To achieve this, companies should focus on establishing clear communication channels that ensure seamless information flow and encourage cross-department collaboration to break down silos. Investing in team-building activities and skill development is another key strategy, helping employees work better together and fostering stronger teamwork. These efforts lead to improved problem-solving, faster decision-making, and increased productivity. Prioritizing collaboration not only enhances business outcomes but also improves employee engagement and satisfaction, which are critical for long-term success in the manufacturing sector. Resource Employment Solutions can help businesses implement these strategies to drive results and create a more cohesive work environment.
In manufacturing, efficiency and productivity are often prioritized, but the importance of team collaboration cannot be overstated. A cohesive and collaborative workforce can solve problems faster, reduce errors, and boost overall operational performance. Yet, achieving high levels of collaboration in the fast-paced, often complex manufacturing environment requires a deliberate strategy.
At Resource Employment Solutions, we understand how essential collaboration is for smooth operations. In this article, we will explore three key strategies for enhancing team collaboration in manufacturing environments, using real-world examples to highlight the benefits of these approaches.
1. Implement Clear Communication Channels
One of the main challenges in any workplace, particularly in manufacturing, is ensuring that communication flows smoothly across departments and shifts. Miscommunication can lead to production errors, wasted resources, and even safety risks. By implementing clear and consistent communication channels, manufacturers can break down silos and ensure that all employees are informed, connected, and able to collaborate effectively.
For example, a large automotive parts manufacturer struggled with production delays due to miscommunication between their design and production teams. The company decided to implement a digital communication platform where teams could share updates, plans, and progress in real-time. This change not only improved communication but also fostered collaboration between the design and production teams, as they were now able to address issues more quickly and work together to optimize designs. The result was a 20% reduction in production delays.
Using digital tools, establishing regular team meetings, and having clear reporting structures can significantly improve collaboration. Clear communication fosters trust and enables teams to make informed, collaborative decisions that positively impact the entire production process.
2. Encourage Cross-Department Collaboration
Manufacturing environments are typically divided into specialized departments, each focused on a specific area of production. While specialization is important, it can also create barriers that hinder collaboration. Encouraging cross-department collaboration allows teams to gain a broader perspective on how their roles contribute to overall success and how they can work more effectively together.
For example, a food processing company experienced inefficiencies in its packaging line due to poor coordination between the production and quality control teams. The company introduced a cross-department collaboration initiative, bringing representatives from both departments into regular joint meetings to identify bottlenecks and brainstorm solutions. The increased collaboration led to streamlined processes and a 15% increase in production efficiency.
Cross-department collaboration not only helps identify areas of improvement but also fosters a culture of teamwork and shared responsibility. Employees feel more connected to the overall mission and are more likely to contribute ideas that enhance performance.
3. Invest in Team Building and Skill Development
Building a culture of collaboration doesn’t happen overnight—it requires ongoing efforts to strengthen team dynamics. Investing in team-building activities and providing opportunities for skill development can significantly enhance collaboration. When employees feel connected to their peers and have the skills needed to work together effectively, they are more likely to communicate openly, share knowledge, and support one another.
For example, a plastics manufacturer noticed that many of their newer employees were struggling to integrate with their more experienced colleagues, leading to communication gaps and slowdowns in production. To address this, the company organized team-building workshops and introduced peer mentoring programs where experienced employees could guide newer workers. These efforts not only improved collaboration but also fostered a sense of community within the workforce, leading to a more efficient and harmonious production environment.
By fostering strong relationships and providing ongoing skill development, manufacturers can create teams that work cohesively, leading to improved problem-solving, faster decision-making, and a more productive workplace
Enhancing team collaboration in manufacturing environments is key to improving efficiency, reducing errors, and fostering a smoother operational process. By focusing on clear communication, encouraging cross-departmental collaboration, and investing in team-building efforts, manufacturers can create a more cohesive and effective workforce.
As manufacturing continues to evolve, prioritizing teamwork and open communication will be crucial for navigating complexities and maintaining a competitive edge. A workplace where collaboration thrives leads to better decision-making, increased engagement, and more productive teams. By cultivating a culture of collaboration, manufacturers can ensure long-term success while also enhancing the work experience for their employees. A focus on teamwork ultimately benefits both the business and the people driving it.
Written on behalf of RES.
The RES Onboarding Process
Our commitment to you is deeper than just providing a list of potential candidates. We are committed to designing and implementing the most effective staffing strategy for you. Here is what you can expect when you choose Resource Employment Solutions as your recruiting and staffing partner.
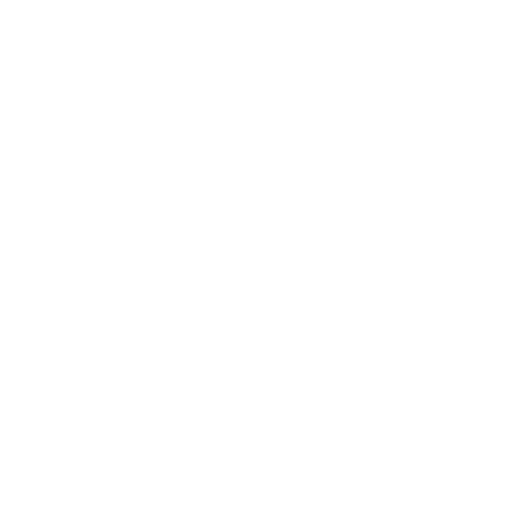
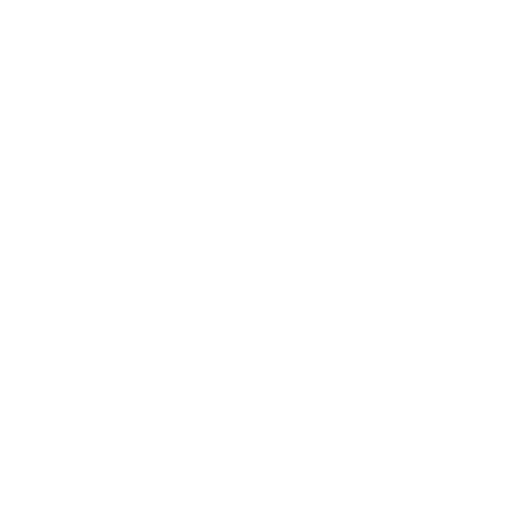
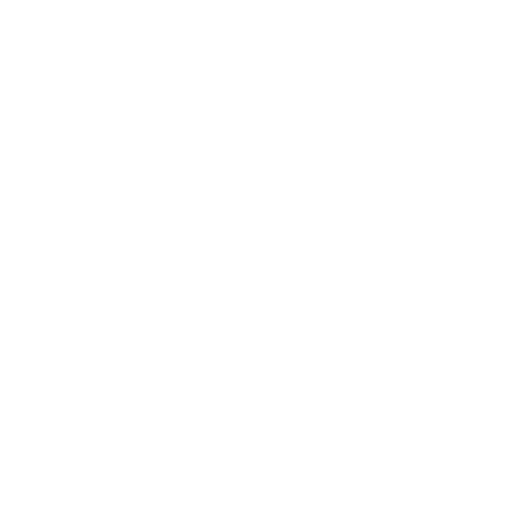
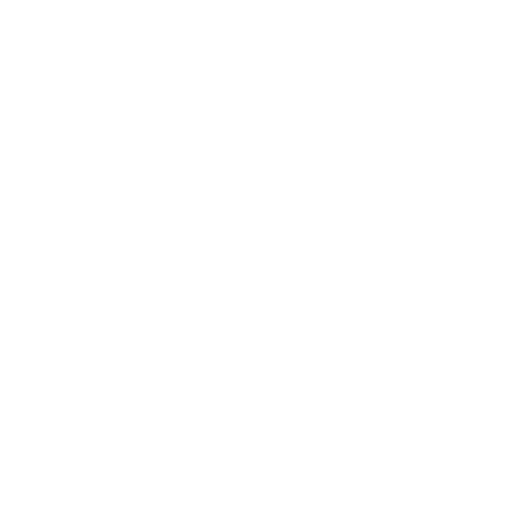
When you connect with Resource Employment Solutions, you will be matched with an account management team who specializes in placing top talent within your industry. You will have a dedicated recruiter or recruiting team assigned and they will remain your point of contact to understand your business and address all your staffing needs.
Frequently Asked Questions
Team collaboration improves efficiency, reduces errors, and fosters a more cohesive and productive workforce.
Clear communication ensures that information flows smoothly across teams, reducing miscommunication and production errors.
Cross-department collaboration helps break down silos, allowing teams to work together more effectively and identify process improvements.