How to Prepare Your Manufacturing Workforce for Technological Changes

Preparing a manufacturing workforce for technological changes requires a comprehensive approach that focuses on training, fostering a culture of innovation, and clear communication. Continuous training and development help employees acquire the necessary skills to work with new technologies, while a culture that encourages change enables workers to view advancements as opportunities rather than threats. Open communication ensures that employees understand the purpose of new technologies and how these changes will impact their roles, reducing anxiety and resistance. By implementing these strategies, companies can help their workforce adapt to the evolving demands of the manufacturing industry, ultimately positioning both employees and the organization for long-term success in an increasingly technology-driven environment.
As technological advancements continue to reshape the manufacturing landscape, companies must adapt to remain competitive. From automation and robotics to data analytics and artificial intelligence, new technologies are transforming how manufacturing operations are conducted. While these innovations bring opportunities for greater efficiency and productivity, they also present challenges—particularly for the workforce. Employees must be prepared to adapt, learn new skills, and embrace the changes that come with technological advancements.
At Resource Employment Solutions, we understand the unique demands that technological transitions place on manufacturing teams. Preparing your workforce for these changes is not just about introducing new tools; it’s about equipping employees with the skills, support, and mindset they need to succeed in an evolving industry. Below, we explore three key strategies for preparing your manufacturing workforce for technological changes, with real-world examples to illustrate their effectiveness.
1. Invest in Ongoing Training and Development
One of the most critical steps in preparing your workforce for technological changes is to provide ongoing training and development opportunities. As new technologies are introduced, employees need to understand how to use them effectively. Training not only equips workers with the technical skills they need but also fosters confidence and reduces the anxiety that often accompanies change.
For example, a global automotive manufacturer implemented a new automation system to streamline assembly line processes. While the system promised to increase productivity, many workers were initially apprehensive about learning how to operate the new technology. To ease the transition, the company offered a comprehensive training program that included hands-on workshops, one-on-one mentoring, and online learning modules. The result was a smooth integration of the new system, with employees quickly gaining the skills they needed to work alongside the automation. This not only improved efficiency but also boosted employee morale, as workers felt more confident in their ability to adapt to new tools.
By investing in continuous training and development, companies can ensure that their employees are not only prepared for current technological changes but also equipped to handle future advancements as the industry continues to evolve.
2. Foster a Culture of Change and Innovation
Technological changes can be daunting, especially for employees who are used to traditional methods of manufacturing. To prepare your workforce, it’s essential to foster a culture of change and innovation within the company. When employees are encouraged to embrace change and experiment with new technologies, they are more likely to see technological advancements as opportunities rather than threats.
For example, a food and beverage manufacturer faced resistance when introducing a new data analytics system to optimize production schedules. Employees were hesitant to adopt the system, fearing that it would add complexity to their workflows. To address this, management took a proactive approach by involving employees in the implementation process. They organized brainstorming sessions, invited feedback on the system’s functionality, and encouraged employees to experiment with the new technology. This collaborative approach not only increased buy-in but also helped employees feel more comfortable with the change. Over time, the workforce began to view the new system as a valuable tool for streamlining operations and improving output.
By creating an environment where innovation is valued and change is seen as an opportunity for growth, companies can help their workforce embrace technological advancements with a positive attitude.
3. Prioritize Communication and Support
Clear and consistent communication is crucial when preparing your workforce for technological changes. Employees need to understand the reasons behind the changes, how the new technologies will impact their roles, and what support will be available to help them through the transition. Transparent communication helps reduce uncertainty and builds trust between management and staff.
For example, a large electronics manufacturer implemented a robotics system to handle repetitive tasks on the production line. To ensure a smooth transition, the company held a series of meetings where management explained the benefits of the new system, including how it would improve safety and reduce physical strain on workers. They also addressed employee concerns about potential job losses, reassuring staff that the robots were intended to complement, not replace, human labor. In addition, the company set up a support system that included dedicated trainers and a help desk for troubleshooting. By prioritizing communication and offering ongoing support, the manufacturer successfully integrated the robotics system with minimal disruption to daily operations.
Open lines of communication, combined with readily available support, help employees feel more secure and informed, reducing resistance to technological changes.
Preparing your manufacturing workforce for technological advancements requires more than just introducing new tools and systems—it involves a holistic approach that includes ongoing training, fostering a culture of innovation, and maintaining clear, supportive communication. By focusing on these strategies, businesses can help their employees adapt more easily to the evolving demands of the industry.
Technological change can be a challenge, but it also presents opportunities for growth, efficiency, and innovation. When employees feel prepared and supported, they are more likely to embrace these changes and contribute to the overall success of the organization. Creating an environment that encourages learning and flexibility is key to ensuring that both the workforce and the company can thrive in the face of technological advancements.
Written on behalf of RES.
The RES Onboarding Process
Our commitment to you is deeper than just providing a list of potential candidates. We are committed to designing and implementing the most effective staffing strategy for you. Here is what you can expect when you choose Resource Employment Solutions as your recruiting and staffing partner.
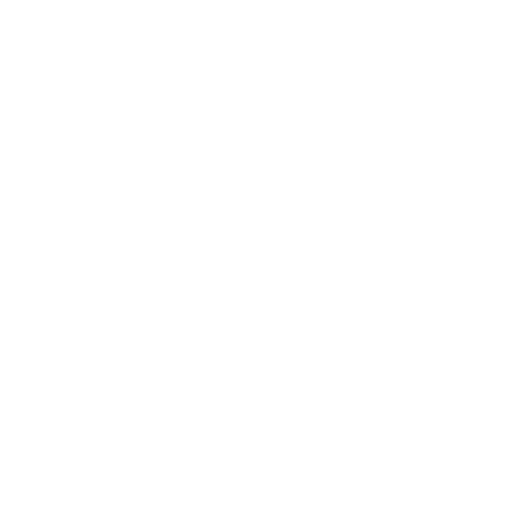
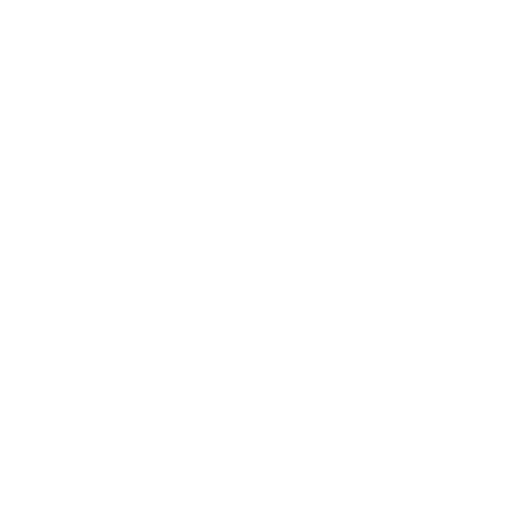
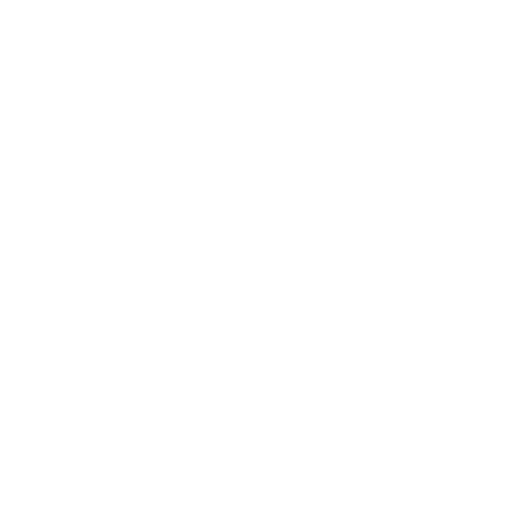
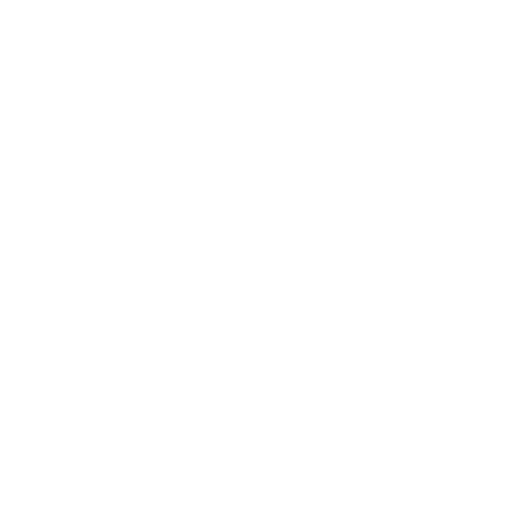
When you connect with Resource Employment Solutions, you will be matched with an account management team who specializes in placing top talent within your industry. You will have a dedicated recruiter or recruiting team assigned and they will remain your point of contact to understand your business and address all your staffing needs.
Frequently Asked Questions
A culture of innovation encourages employees to embrace new technologies and view change as an opportunity for growth, reducing resistance and making adaptation easier.
Clear and consistent communication helps employees understand the reasons for the changes, how it affects their roles, and what support is available, reducing uncertainty and fear.