Implementing Performance Metrics for Manufacturing Staff | RES
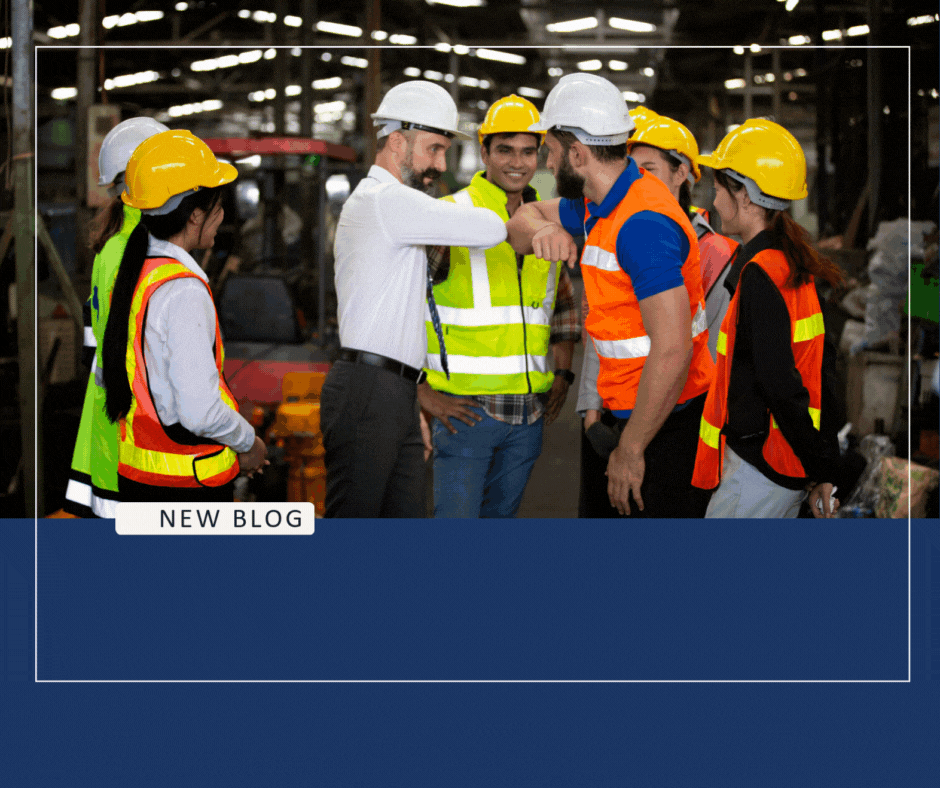
Implementing effective performance metrics for manufacturing staff is essential for aligning employee efforts with organizational goals. This article outlines three key steps: setting clear and relevant goals, balancing quantitative and qualitative measurements, and using metrics to drive positive change. By setting specific goals tied to production, quality, and safety, companies can provide direction and motivation for their teams. Incorporating both quantitative and qualitative metrics ensures a holistic view of performance, capturing efficiency and employee engagement. Finally, using metrics to identify bottlenecks and support improvement fosters a positive work environment. When thoughtfully applied, performance metrics can enhance productivity and promote a culture of continuous development. Book your consultation with Resource Employment Solutions today!
Measuring employee performance in manufacturing is critical to ensuring operational efficiency and driving continuous improvement. However, implementing effective performance metrics goes beyond just tracking outputs. It’s about establishing a framework that captures productivity, quality, safety, and employee engagement—ultimately aligning staff performance with the organization’s overall goals.
For manufacturing companies, where even small inefficiencies can significantly impact profitability, selecting the right metrics can help identify strengths, uncover improvement areas, and create a data-driven path to success. At Resource Employment Solutions, we’ve seen how the right performance measures can transform the workplace, boosting both productivity and employee morale. In this article, we’ll explore three key aspects of implementing effective performance metrics: setting clear, relevant goals, balancing qualitative and quantitative measurements, and using metrics to drive positive change.
1. Setting Clear, Relevant Goals
The foundation of any effective performance metric is having clear and relevant goals that are tied to the overall business objectives. In manufacturing, this often means defining specific targets related to production output, quality standards, and safety. Without clear goals, metrics can become arbitrary and disconnected from what truly matters to the organization.
For example, if a company wants to increase its monthly production output by 10%, it needs to establish specific metrics such as machine utilization rates or employee cycle times. These metrics should be communicated clearly to all team members, ensuring that everyone understands how their individual contributions affect the broader business outcomes.
It’s also important to differentiate between long-term strategic goals and short-term operational targets. Strategic goals, such as reducing defect rates by 20% over the next year, help guide broader initiatives and resource allocation. On the other hand, short-term targets, like achieving a daily production quota, provide immediate focus and motivation for employees. Ensuring that these goals are both challenging and attainable will help keep employees engaged and invested in their performance.
2. Balancing Quantitative and Qualitative Metrics
While quantitative metrics such as production output, cycle time, and downtime are essential for measuring efficiency, they don’t tell the whole story. To get a complete picture of employee performance, companies should incorporate qualitative metrics that assess factors like teamwork, problem-solving abilities, and adherence to safety protocols.
For instance, a common quantitative metric in manufacturing is the number of units produced per shift. However, focusing solely on output can lead to unintended consequences, such as employees cutting corners or neglecting quality to meet quotas. By pairing output metrics with qualitative measures like quality control scores and peer feedback, companies can ensure that performance is well-rounded and aligned with broader values.
An effective qualitative metric example could be tracking how often employees contribute suggestions for process improvements. This can indicate engagement and a proactive approach to problem-solving, which are critical for fostering a culture of continuous improvement.
Balancing these two types of metrics not only provides a fuller understanding of employee performance but also helps in identifying training needs and development opportunities, contributing to a more supportive and growth-oriented workplace.
3. Using Metrics to Drive Positive Change
The ultimate goal of implementing performance metrics is to use them as a tool for driving positive change, not just as a means of evaluation. When used correctly, metrics can provide actionable insights that help managers support employees, optimize processes, and make data-driven decisions that benefit the entire organization.
For example, if a particular team consistently falls short of their production targets, managers can delve deeper into the metrics to identify potential bottlenecks, such as machine downtime or inadequate training. Instead of using the data solely to highlight underperformance, managers can then take corrective action, such as scheduling additional maintenance or providing targeted training.
Additionally, metrics can be used to recognize and reward high-performing employees. For instance, if a team consistently meets its safety and production goals, acknowledging their efforts can reinforce positive behaviors and motivate other teams to strive for similar results. This approach turns metrics into a source of empowerment, making employees feel more engaged and valued.
A key consideration is to ensure that employees see performance metrics as a pathway to development rather than a punitive measure. Regular feedback sessions, where metrics are reviewed collaboratively, can help employees understand where they stand and what steps they can take to improve. This creates a sense of ownership and accountability, which is crucial for long-term success.
Implementing effective performance metrics for manufacturing staff requires more than just focusing on numbers. It’s about establishing a comprehensive system that supports productivity, employee development, and long-term success. By setting clear goals, balancing quantitative and qualitative measures, and using metrics to identify areas for positive change, companies can create a well-rounded performance management framework. When approached thoughtfully, performance metrics become tools for understanding and supporting the workforce, helping to build a more engaged and motivated team. In this way, organizations can cultivate a culture that values both individual contributions and collective achievements, fostering a positive and productive working environment that benefits everyone involved. Book your consultation to get started with Resource Employment Solutions.
Written on behalf of RES.
The RES Onboarding Process
Our commitment to you is deeper than just providing a list of potential candidates. We are committed to designing and implementing the most effective staffing strategy for you. Here is what you can expect when you choose Resource Employment Solutions as your recruiting and staffing partner.
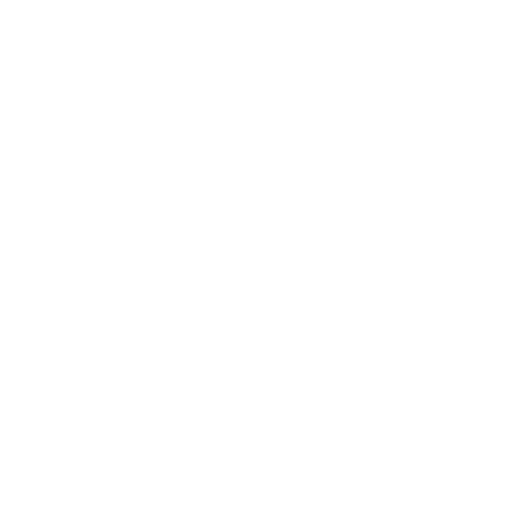
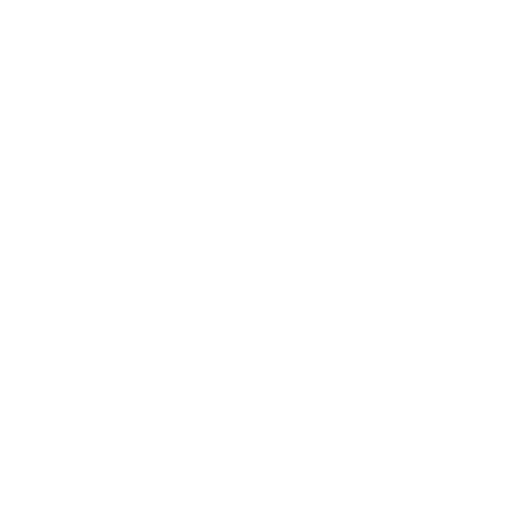
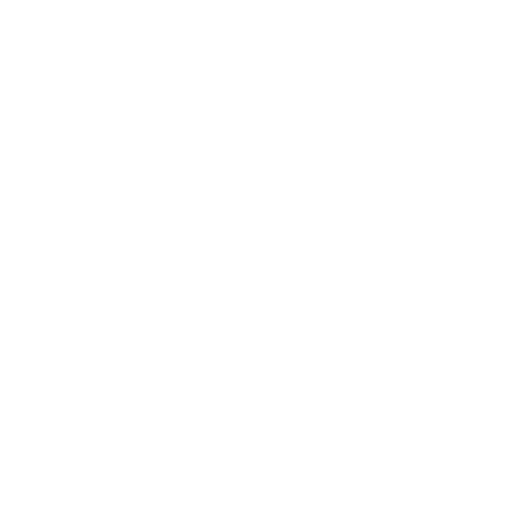
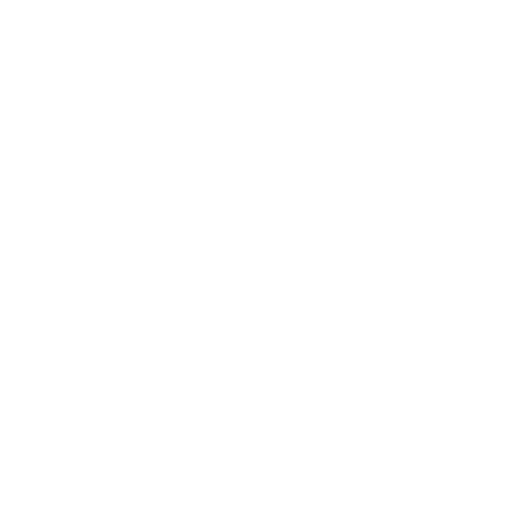
When you connect with Resource Employment Solutions, you will be matched with an account management team who specializes in placing top talent within your industry. You will have a dedicated recruiter or recruiting team assigned and they will remain your point of contact to understand your business and address all your staffing needs.
Frequently Asked Questions
Performance metrics are measurable indicators used to evaluate staff productivity, efficiency, quality, and safety in a manufacturing setting.
Clear goals ensure that employees understand what is expected of them and how their performance contributes to the overall business objectives.
Quantitative metrics measure numerical data like production output, while qualitative metrics assess non-numeric factors such as teamwork, problem-solving, and safety compliance.