Key Metrics to Track for Optimal Warehouse Performance and Efficiency
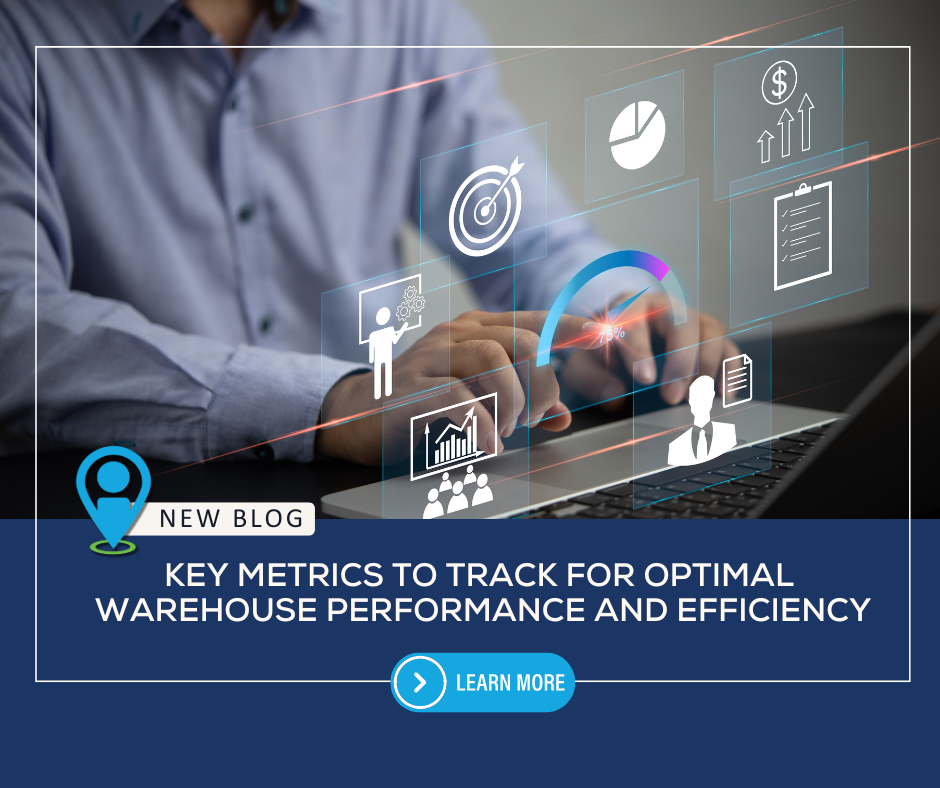
Tracking key performance metrics is essential for optimizing warehouse operations. Key metrics like order accuracy, inventory turnover, and labor productivity provide insights into how efficiently a warehouse is functioning. High order accuracy ensures customer satisfaction, while inventory turnover helps manage stock levels effectively and improve cash flow. Labor productivity measures workforce efficiency and highlights areas for process improvements. By monitoring and acting on these metrics, businesses can enhance efficiency, reduce costs, and boost overall performance. However, alongside these metrics, a well-trained and supported workforce is crucial to achieving long-term success. Regularly reviewing these indicators allows organizations to continuously improve and adapt to changing demands in the warehouse environment.
In today’s fast-paced business landscape, the efficiency and performance of warehouse operations are crucial to an organization’s overall success. Warehouses that track and optimize key performance metrics can not only enhance productivity but also reduce costs, improve customer satisfaction, and boost profitability. At Resource Employment Solutions,, we understand the critical role that skilled labor and well-managed teams play in achieving these outcomes. By closely monitoring the right metrics, businesses can maintain a smooth, efficient warehouse operation.
In this article, we will explore three essential metrics that every warehouse should track for optimal performance: order accuracy, inventory turnover, and labor productivity. Each of these metrics provides valuable insights into how well a warehouse is functioning and highlights areas for improvement.
1. Order Accuracy
Order accuracy measures the percentage of orders that are picked, packed, and delivered without errors. A high order accuracy rate is essential for ensuring customer satisfaction, as incorrect orders can lead to returns, delays, and dissatisfaction. This metric reflects how well a warehouse is managing its fulfillment process, including inventory management, picking accuracy, and packing processes.
Consider a retail company that struggled with a 90% order accuracy rate, leading to increased customer complaints and return shipments. After auditing their processes, they found that outdated picking systems were causing errors in fulfillment. By investing in more efficient technology and retraining their staff on best practices, they were able to improve order accuracy to 98%, reducing returns and increasing customer satisfaction.
Tracking order accuracy allows businesses to quickly identify problems in their fulfillment process. Regularly monitoring this metric enables management to implement process improvements, staff training, or technology upgrades to ensure a higher rate of successful deliveries.
2. Inventory Turnover
Inventory turnover measures how many times a warehouse’s inventory is sold and replaced over a specific period. This metric is crucial for understanding how well a company is managing its inventory levels. A high inventory turnover rate indicates efficient use of storage space and better cash flow management, while a low rate could suggest overstocking, poor demand forecasting, or slow-moving goods.
For example, a warehouse handling consumer electronics noticed a decline in their inventory turnover rate, which led to increased storage costs and tied-up capital in unsold stock. Upon reviewing their demand forecasting and inventory management systems, they discovered that they were overstocking outdated products that were no longer in high demand. By adjusting their stock levels and improving their demand forecasting, the warehouse was able to increase inventory turnover and reduce excess stock, improving overall profitability.
Monitoring inventory turnover helps businesses avoid issues like overstocking or stockouts, both of which can disrupt warehouse efficiency. By keeping an eye on this metric, companies can better align their inventory levels with demand and ensure optimal use of resources.
3. Labor Productivity
Labor productivity measures how efficiently warehouse employees are performing their tasks. This metric is often expressed as the number of orders or units processed per hour per employee. It is a critical indicator of workforce efficiency and can reveal whether staffing levels are adequate or if additional training or process improvements are needed.
For example, a food distribution center experienced delays in order fulfillment due to labor productivity issues. After analyzing the data, they found that employees were spending too much time traveling between pick locations due to poor warehouse layout. By redesigning the layout and introducing a more streamlined workflow, they were able to increase labor productivity by 20%, resulting in faster order processing and reduced overtime costs.
Tracking labor productivity enables management to assess the efficiency of their workforce and identify any bottlenecks in workflow. It also helps ensure that staff are adequately supported with the right tools, training, and resources to perform their jobs effectively.
Optimizing warehouse performance relies heavily on tracking and analyzing key metrics such as order accuracy, inventory turnover, and labor productivity. By keeping a close eye on these indicators, businesses can make data-driven decisions that lead to improved efficiency, cost savings, and better customer outcomes.
While these metrics provide valuable insights, it’s equally important to ensure that the workforce has the right tools, training, and support to maintain high performance. A well-run warehouse is not just about numbers—it’s about empowering the team to do their best work. As businesses continue to evolve, consistently reviewing and refining these metrics can foster an environment of continuous improvement, helping warehouses remain adaptable and competitive in an ever-changing landscape.
Written on behalf of RES.
The RES Onboarding Process
Our commitment to you is deeper than just providing a list of potential candidates. We are committed to designing and implementing the most effective staffing strategy for you. Here is what you can expect when you choose Resource Employment Solutions as your recruiting and staffing partner.
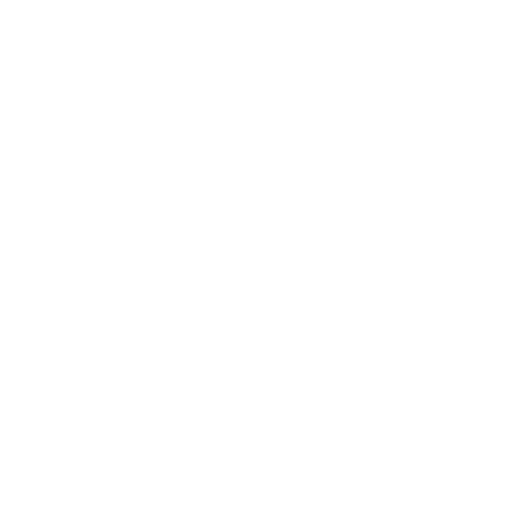
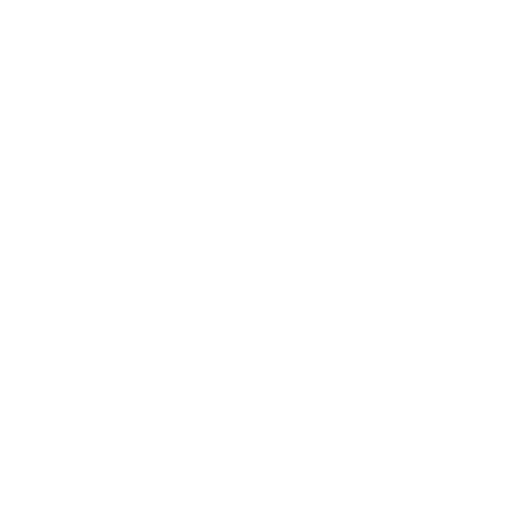
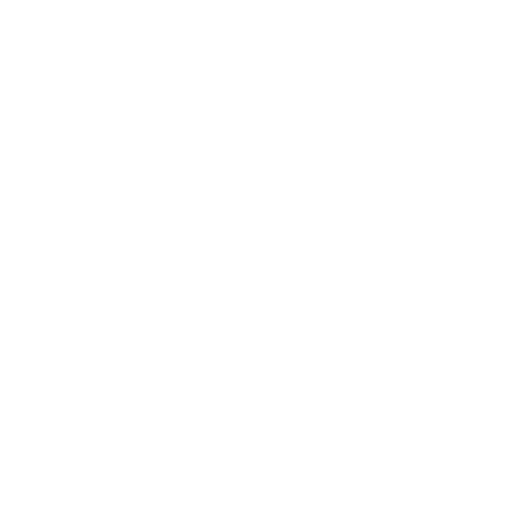
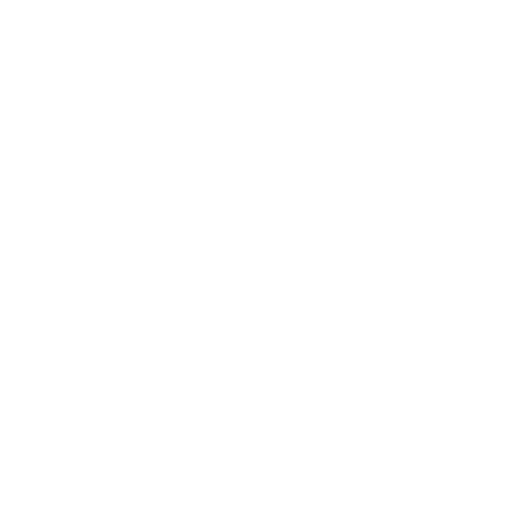
When you connect with Resource Employment Solutions, you will be matched with an account management team who specializes in placing top talent within your industry. You will have a dedicated recruiter or recruiting team assigned and they will remain your point of contact to understand your business and address all your staffing needs.
Frequently Asked Questions
All three metrics—order accuracy, inventory turnover, and labor productivity—are crucial. Each provides different insights, but order accuracy directly impacts customer satisfaction, making it particularly important.
Improving order accuracy reduces errors, lowers return rates, and increases customer satisfaction, ultimately saving the business time and money.
Inventory turnover helps monitor how quickly products are sold and replaced. A high turnover rate indicates efficient inventory management, while a low rate may signal overstocking or poor demand forecasting.