Major Trends and Changes in Manufacturing Staffing | RES
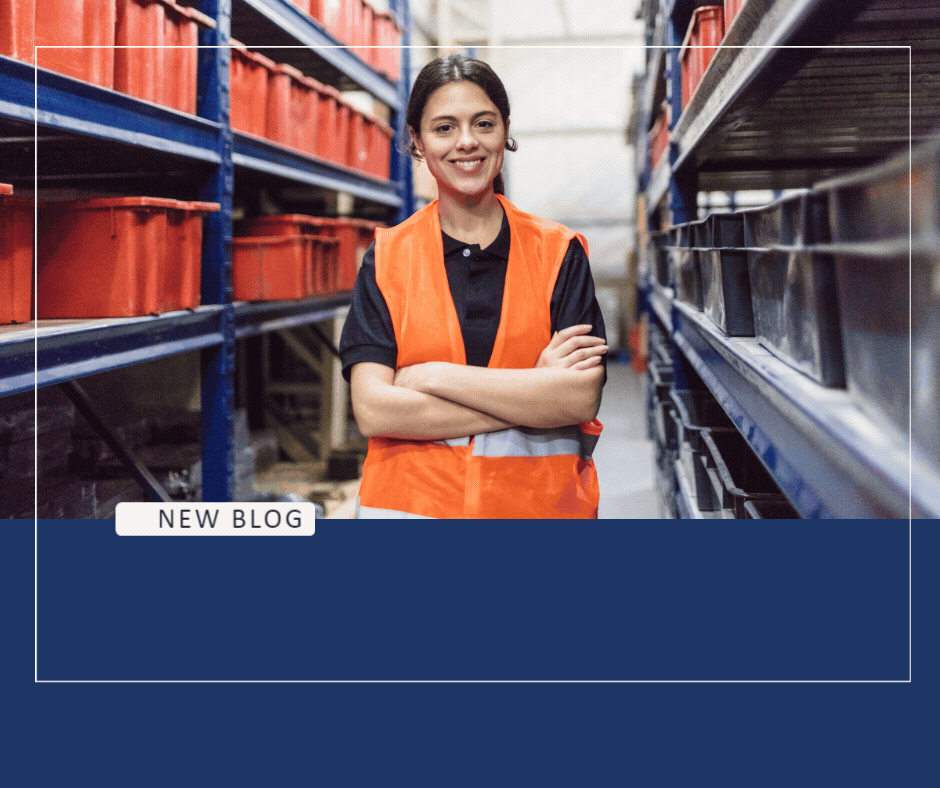
The manufacturing industry is undergoing significant changes driven by automation, the need for specialized roles, and the rise of flexible work arrangements. Automation requires a workforce equipped with technical skills, while complex production processes create demand for specialized positions in areas like data analytics and quality control. Flexible staffing models, such as temporary and contract roles, allow manufacturers to adapt to fluctuating market demands. Companies that invest in ongoing training, recruit specialized talent, and embrace flexible work arrangements are better positioned to navigate these changes. These trends are reshaping the way manufacturers approach staffing, making it essential for organizations to build a skilled, adaptable workforce that can thrive in an increasingly complex and technology-driven environment.
The manufacturing industry has undergone significant transformations over the past few years, with rapid advancements in technology, evolving workforce needs, and changing market demands. These shifts have profoundly impacted how companies approach staffing. To stay competitive, manufacturers need a flexible and skilled workforce that can adapt to new technologies and respond to fluctuating demands.
At Resource Employment Solutions, we understand the unique challenges manufacturers face in recruiting, training, and retaining talent in an increasingly complex landscape. This article will explore three major trends in manufacturing staffing—automation, the growing demand for specialized skills, and the rise of flexible work arrangements—and how companies are adapting to these changes.
1. Automation and the Need for Technical Skills
Automation is reshaping the manufacturing industry, from robotics on the factory floor to AI-driven data analytics. While automation promises greater efficiency, it also requires a workforce with advanced technical skills. The days when manufacturing jobs were mainly focused on manual labor are fading. Today, manufacturers need workers who can operate and maintain complex machinery, program robotics, and analyze data to optimize processes.
For example, a large electronics manufacturer invested heavily in automation to increase production efficiency. However, they soon realized that their existing workforce did not have the technical skills required to operate the new machinery. To address this gap, the company implemented a comprehensive upskilling program, offering employees the opportunity to learn about advanced robotics and automation systems. By investing in their workforce, the company not only improved operational efficiency but also increased employee retention, as workers felt more valued and equipped to grow alongside technological advancements.
The shift toward automation has highlighted the need for ongoing training and development. Companies that provide opportunities for skill development can build a workforce capable of adapting to the latest technologies, ensuring long-term success.
2. The Growing Demand for Specialized Roles
As manufacturing becomes more complex, the demand for specialized roles is increasing. Manufacturers need employees with expertise in areas like data analytics, supply chain management, quality control, and advanced engineering. These specialized roles are essential for managing increasingly sophisticated production processes, optimizing efficiency, and ensuring quality standards are met.
For example, a pharmaceutical manufacturing company sought to improve its quality control processes to meet stringent regulatory standards. The company found that its existing staff lacked the specialized knowledge needed to oversee these processes effectively. To solve this problem, they partnered with a staffing firm to recruit candidates with expertise in pharmaceutical quality control and compliance. By filling these specialized roles, the company was able to improve product quality, reduce waste, and meet regulatory requirements more efficiently.
Manufacturers are now competing for talent in highly specialized fields, and this trend is expected to continue as the industry grows more complex. Recruiting and retaining top talent with specialized skills is becoming a key priority for manufacturers looking to maintain a competitive edge.
3. The Rise of Flexible Work Arrangements
Flexible work arrangements, including part-time, temporary, and contract roles, are becoming increasingly common in manufacturing. Seasonal fluctuations, project-based work, and the need for cost-effective staffing solutions have driven companies to adopt more flexible staffing models. This allows manufacturers to scale their workforce up or down based on demand without committing to long-term employment contracts.
For example, a furniture manufacturer experienced a spike in demand during the holiday season but did not have the capacity to hire full-time employees for such a short-term need. To solve this problem, the company turned to temporary staffing solutions, bringing in skilled workers on a seasonal basis. This allowed the company to meet the surge in demand without the financial strain of long-term hiring. Moreover, several temporary workers demonstrated excellent performance and were later offered permanent positions once demand stabilized.
This trend toward flexible staffing is particularly beneficial for manufacturers who face fluctuating production needs. Temporary staffing solutions provide the agility needed to respond to short-term demands while maintaining operational efficiency.
The manufacturing industry is evolving rapidly, driven by technological advancements, the need for specialized skills, and the rise of flexible work arrangements. As automation becomes more prevalent, manufacturers are faced with the challenge of ensuring their workforce is equipped with the necessary technical skills. The increasing complexity of manufacturing processes has also created a demand for specialized roles, while flexible staffing models offer the agility to adapt to fluctuating market demands.
By recognizing and addressing these trends, manufacturers can position themselves for continued success. Investing in skill development, attracting specialized talent, and adopting flexible staffing solutions are key strategies for navigating the future of manufacturing staffing. As the industry continues to evolve, maintaining a dynamic, skilled workforce will be essential for staying competitive in the global market.
Written on behalf of RES.
The RES Onboarding Process
Our commitment to you is deeper than just providing a list of potential candidates. We are committed to designing and implementing the most effective staffing strategy for you. Here is what you can expect when you choose Resource Employment Solutions as your recruiting and staffing partner.
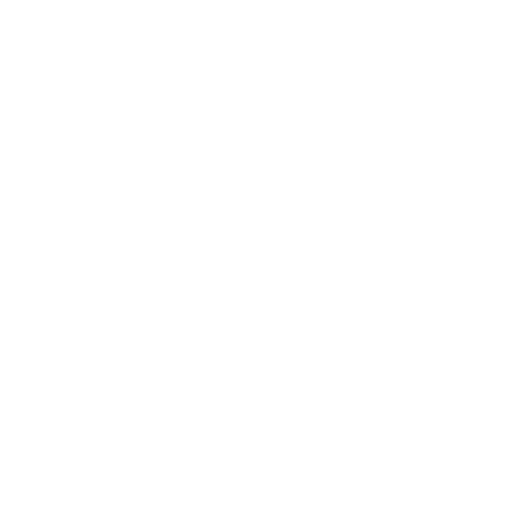
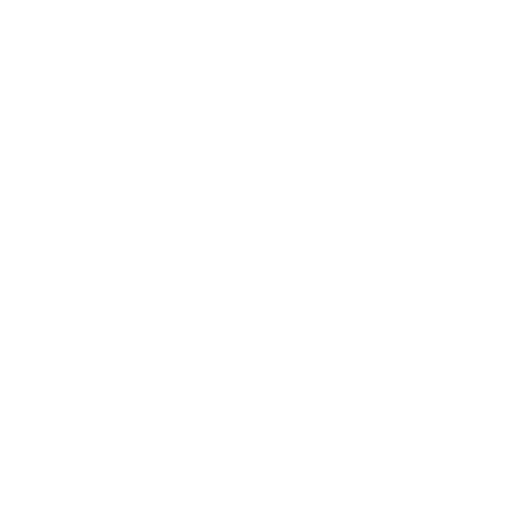
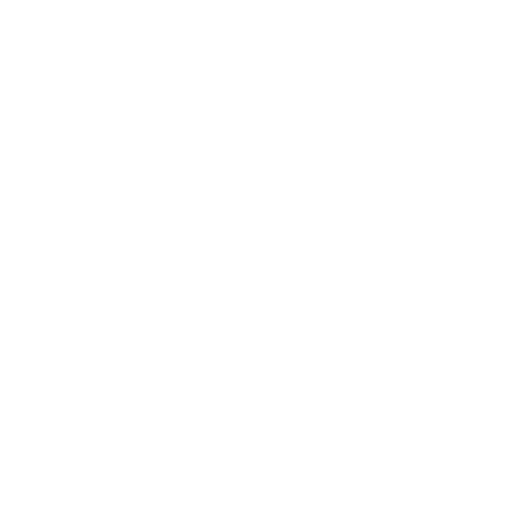
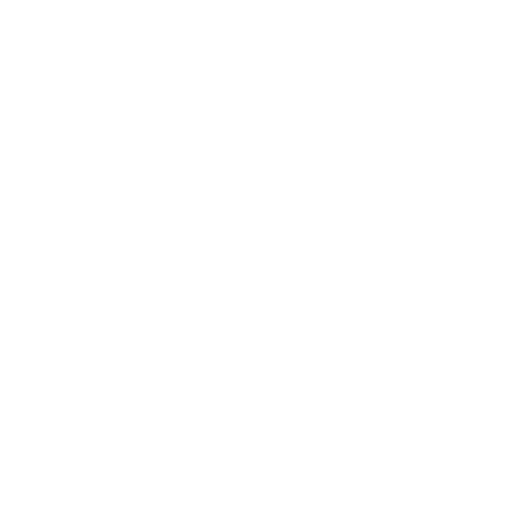
When you connect with Resource Employment Solutions, you will be matched with an account management team who specializes in placing top talent within your industry. You will have a dedicated recruiter or recruiting team assigned and they will remain your point of contact to understand your business and address all your staffing needs.
Frequently Asked Questions
Automation is increasing the demand for workers with advanced technical skills, such as operating and maintaining complex machinery, robotics, and data analytics. This shift requires companies to invest in upskilling their workforce to adapt to new technologies.
As manufacturing processes become more complex, specialized roles in areas like quality control, data analytics, and supply chain management are essential for optimizing efficiency and meeting regulatory standards. These positions require expertise beyond traditional manufacturing skills.
Flexible staffing models, such as part-time, temporary, and contract work, allow manufacturers to adjust their workforce based on seasonal demand or project needs. This approach reduces long-term hiring costs while maintaining operational flexibility.