Navigating Regulatory Changes in the Manufacturing Sector
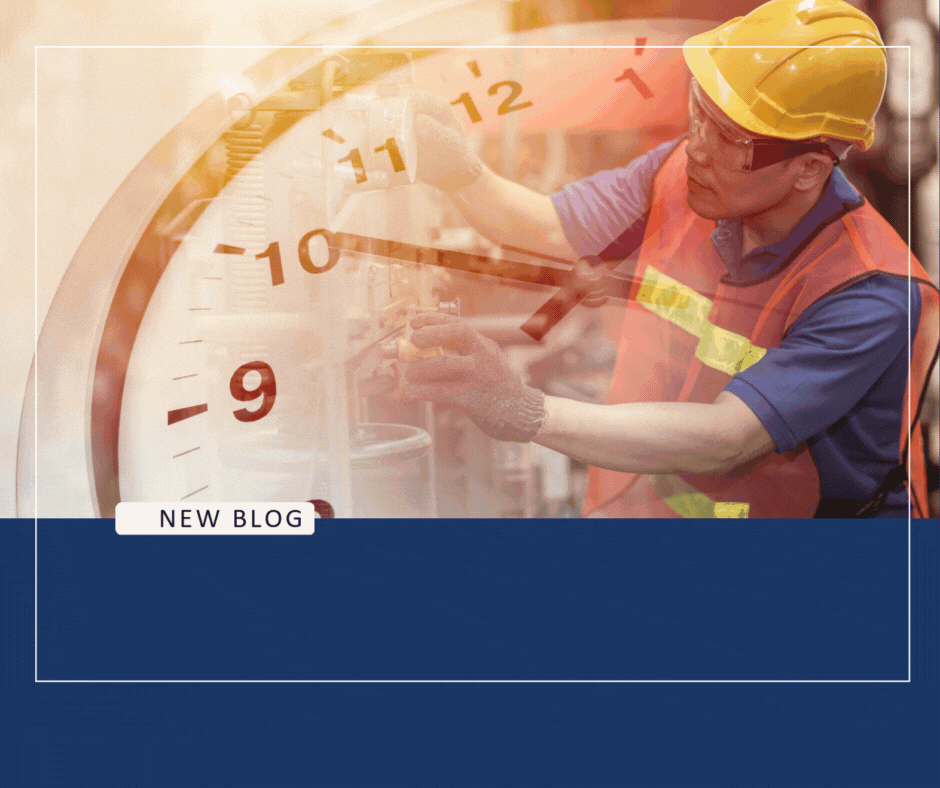
Regulatory changes can be a major challenge for manufacturers, but with the right approach, they don't have to disrupt your business. From environmental regulations to labor laws, staying compliant is critical for avoiding costly penalties. Manufacturers in states like Illinois, Texas, & Florida are finding success by building compliance teams, leveraging technology, & investing in employee training. Whether you’re a small operation or a large facility, navigating these changes with proactive strategies can keep your business running smoothly. Ready to stay ahead of the curve? Learn how you can manage new regulations, protect your business, & foster a culture of compliance in today’s rapidly evolving manufacturing landscape. Don’t let regulatory changes catch you off guard-Book your consultation with Resource Employment Solutions today!
The manufacturing industry is constantly evolving, and with that evolution comes changes in regulations that can impact everything from production processes to workforce management. Navigating these regulatory changes can be challenging for manufacturers, especially in states like Illinois, New Jersey, North Carolina, Florida, Ohio, Texas, Georgia, Nevada, and Pennsylvania, where compliance laws vary. Staying ahead of new regulations is essential for avoiding costly penalties and disruptions to business operations.
Understanding the Impact of Regulatory Changes
Regulatory changes can have far-reaching impacts on the manufacturing sector. These changes may relate to environmental regulations, labor laws, workplace safety, or trade and tariffs. For example, tightening environmental regulations might require manufacturers to modify production processes or adopt new technology to reduce emissions. Labor laws can affect everything from how employees are classified to the number of hours they are allowed to work.
Understanding the impact of these regulations is the first step in navigating them effectively. Manufacturers must be proactive in identifying which regulations apply to their industry and geographic location. This requires staying informed and regularly reviewing any updates to local, state, and federal laws.
Staying Informed and Engaging with Industry Associations
Staying informed about regulatory changes is crucial for manufacturers to remain compliant. One of the most effective ways to keep up with changing regulations is by engaging with industry associations. These organizations are often at the forefront of policy discussions and can provide valuable insights into upcoming changes.
Industry associations can also offer support and resources, such as webinars, training, and legal advice, to help businesses understand and implement new regulations. Joining such associations can also provide manufacturers with networking opportunities to share best practices with other companies facing similar challenges.
In states like Texas, Georgia, and Ohio, where manufacturing is a major contributor to the economy, industry associations often play a vital role in shaping policy. By staying connected, manufacturers can better anticipate changes and prepare accordingly.
Building a Compliance Team
As regulatory requirements continue to change, manufacturers should consider building a dedicated compliance team to ensure their business stays up to date with new regulations. This team can include legal experts, human resources professionals, and operations managers who work together to ensure that all areas of the business are compliant with relevant laws.
For smaller manufacturers, who may not have the resources for a full-time compliance team, outsourcing compliance responsibilities to a third-party firm can be an effective solution. Companies like Resource Employment Solutions can provide compliance support, helping manufacturers navigate labor laws, safety regulations, and other requirements.
By having a dedicated team in place, manufacturers can better manage regulatory changes and minimize the risk of violations that could lead to fines or legal issues.
Investing in Training and Education
As regulations change, it’s important to ensure that employees are properly trained and educated on new compliance requirements. This applies not only to those in leadership or management roles but also to employees on the factory floor. For example, changes in workplace safety regulations may require workers to adopt new protocols or use additional safety equipment.
Investing in regular training programs helps ensure that all employees understand the regulatory changes and know how to apply them in their daily tasks. Training can be provided through in-house programs, online courses, or external experts.
In states like Florida, New Jersey, and Nevada, where manufacturing spans a wide range of industries, customized training may be necessary to address specific regulatory changes that apply to different sectors.
Implementing Technology to Aid Compliance
Technology can play a crucial role in helping manufacturers stay compliant with new regulations. Implementing automated systems that track production processes, monitor safety standards, and ensure proper record-keeping can reduce the risk of human error and ensure that compliance is maintained.
For example, environmental monitoring systems can help manufacturers meet emissions regulations by providing real-time data on air quality or waste management. Similarly, software solutions can assist with managing labor law compliance, tracking employee work hours, and ensuring that safety protocols are followed.
By leveraging technology, manufacturers can streamline compliance efforts and reduce the administrative burden of tracking and implementing regulatory changes.
Preparing for Future Regulatory Changes
Regulatory environments are constantly evolving, and manufacturers must be prepared for future changes. One way to stay ahead is by conducting regular internal audits to assess current compliance status and identify areas where improvements are needed. This proactive approach can help businesses anticipate changes and implement necessary adjustments before regulations take effect.
In addition, manufacturers should develop a long-term strategy that includes contingency planning for potential regulatory shifts. This might involve diversifying supply chains, investing in more sustainable production methods, or increasing flexibility in workforce management.
For manufacturers in states like Illinois, Pennsylvania, and North Carolina, where regulations may differ at the state and federal levels, preparing for future changes is critical to maintaining competitiveness in the market.
Conclusion
Navigating regulatory changes in the manufacturing sector can be challenging, but it is essential for maintaining compliance and avoiding costly disruptions. By staying informed, engaging with industry associations, building a compliance team, and investing in training and technology, manufacturers can effectively manage new regulations while continuing to grow their businesses.
In an industry that is constantly evolving, preparation and adaptability are key. Manufacturers in states like Texas, Georgia, and Ohio can position themselves for success by taking a proactive approach to regulatory compliance. With the right strategies in place, businesses can not only navigate these changes but also thrive in a competitive landscape. Book your consultation to get started with Resource Employment Solutions.
Written on behalf of RES.
The RES Onboarding Process
Our commitment to you is deeper than just providing a list of potential candidates. We are committed to designing and implementing the most effective staffing strategy for you. Here is what you can expect when you choose Resource Employment Solutions as your recruiting and staffing partner.
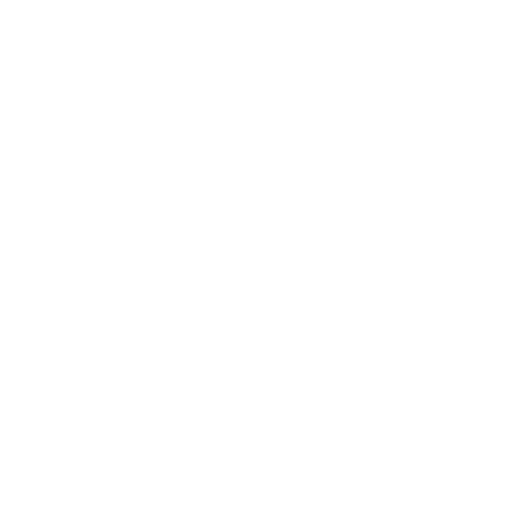
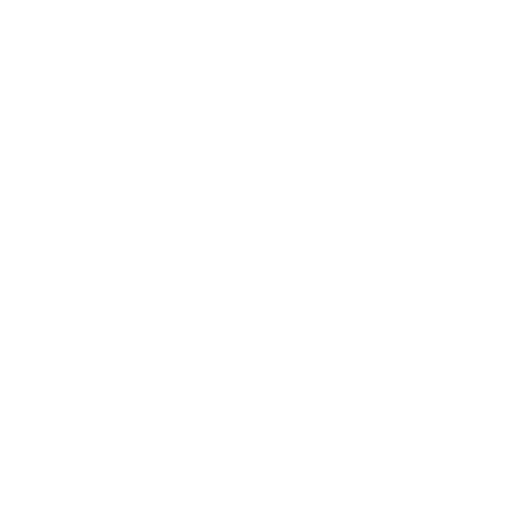
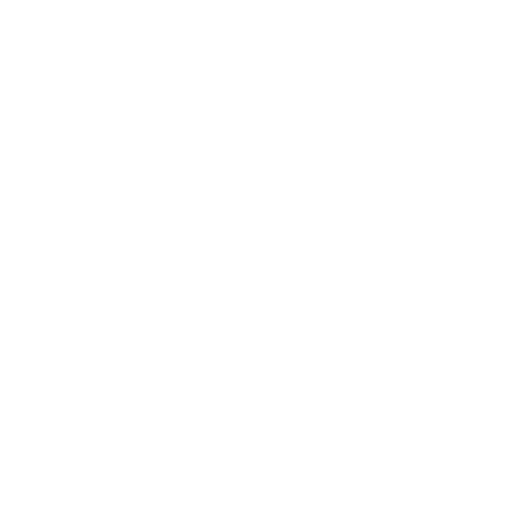
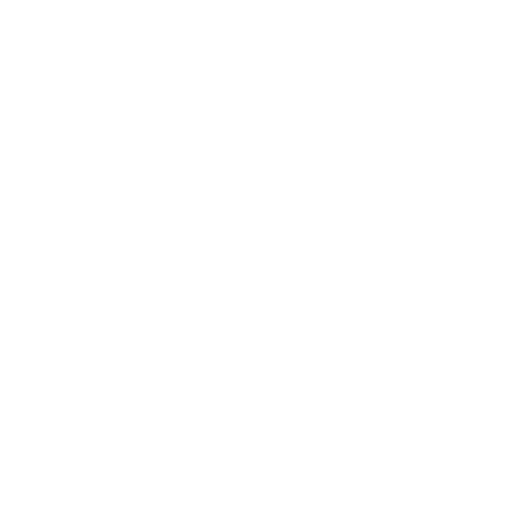
When you connect with Resource Employment Solutions, you will be matched with an account management team who specializes in placing top talent within your industry. You will have a dedicated recruiter or recruiting team assigned and they will remain your point of contact to understand your business and address all your staffing needs.
Frequently Asked Questions
Key areas include labor laws, workplace safety, environmental regulations, and trade policies, all of which can directly affect production processes and workforce management.
Outsourcing compliance responsibilities to third-party firms or consulting agencies can help smaller manufacturers manage regulations without needing in-house staff. Book a consultation to learn more!
Training ensures employees understand and adhere to new regulations, especially those impacting safety protocols, operational procedures, and compliance standards.