Optimize Manufacturing Staffing with Data Analytics | RES
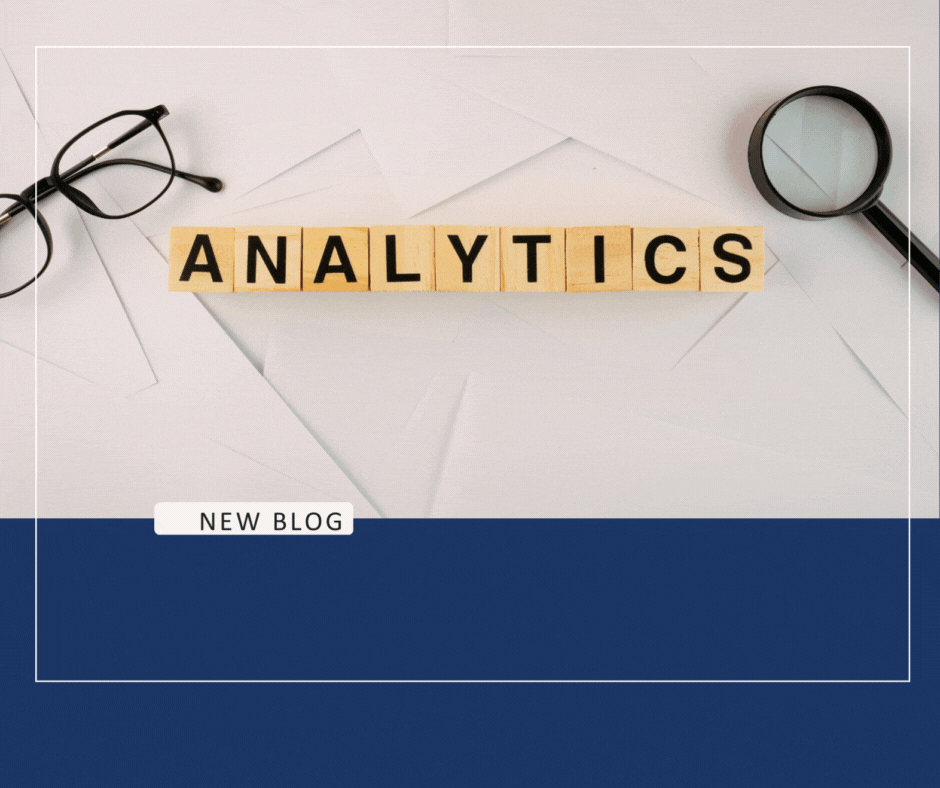
Data analytics is revolutionizing manufacturing staffing by significantly boosting efficiency and productivity. It enables precise prediction of staffing needs based on production schedules, market trends, and other critical factors. This approach also helps reduce turnover by identifying factors impacting employee satisfaction and retention. Understanding retention patterns allows manufacturers to implement targeted career development and recognition programs. We recognize the transformative potential of data-driven strategies and are dedicated to helping manufacturers leverage these insights to optimize workforce management, streamline operations, and achieve greater success in today’s competitive market. Embracing these advanced analytics can drive substantial improvements across all aspects of manufacturing staffing and operations.
In today's rapidly evolving manufacturing landscape, the need for efficiency and precision has never been more critical. As production demands fluctuate, and the pressure to minimize costs while maximizing output intensifies, the role of effective staffing becomes paramount. At the heart of this challenge lies data analytics—a powerful tool that can transform how manufacturing companies approach staffing. By harnessing the insights gleaned from data, businesses can optimize their workforce, ensuring the right people are in the right roles at the right time.
At Resource Employment Solutions, we understand the intricate balance required in manufacturing environments. Our expertise lies in not just filling positions, but in strategically aligning talent with business objectives. With data analytics at the forefront, we empower manufacturing companies to optimize their staffing processes, driving both operational excellence and financial performance.
Predictive Analytics for Workforce Planning
One of the most significant benefits of data analytics in staffing is its ability to predict future workforce needs. Predictive analytics leverages historical data, industry trends, and advanced algorithms to forecast staffing requirements. For instance, if a manufacturing plant experiences seasonal spikes in production, predictive analytics can anticipate these trends, allowing management to proactively adjust staffing levels.
Example: Consider a company that produces consumer electronics. Historically, the demand for their products increases significantly during the holiday season. By using predictive analytics, the company can analyze past sales data, market trends, and supply chain variables to forecast the exact number of temporary workers needed for the peak season. This approach not only prevents understaffing or overstaffing but also ensures that the company can meet demand without compromising on quality or delivery times.
Enhancing Employee Retention through Data-Driven Insights
Employee turnover is a significant challenge in manufacturing, leading to increased costs, production delays, and loss of institutional knowledge. Data analytics can play a crucial role in identifying the factors that contribute to employee dissatisfaction and turnover, enabling companies to implement targeted interventions.
Example: A large automotive parts manufacturer noticed a high turnover rate among its assembly line workers. By analyzing employee data, including tenure, performance reviews, and exit interview feedback, the company identified a pattern: workers with less than a year of experience were leaving at a disproportionately high rate. Further analysis revealed that inadequate onboarding and lack of career development opportunities were primary drivers of dissatisfaction. Armed with this insight, the company revamped its onboarding process and introduced a mentorship program, significantly improving employee retention.
Real-Time Data for Agile Decision-Making
In the fast-paced world of manufacturing, real-time data is invaluable for making agile staffing decisions. Whether it’s responding to an unexpected surge in production or addressing a sudden shortage of skilled labor, having access to up-to-the-minute data allows managers to make informed decisions quickly.
Example: Imagine a situation where a manufacturer of medical devices experiences an unexpected increase in demand due to a global health crisis. With real-time data analytics, the company can monitor production rates, absenteeism, and overtime hours in real-time. This immediate access to data enables management to quickly identify bottlenecks, reallocate resources, and, if necessary, bring in additional staff to ensure uninterrupted production.
Integrating data analytics into manufacturing staffing strategies offers a powerful way to enhance efficiency and effectiveness in today’s competitive environment. By leveraging data to accurately predict staffing needs, optimize workforce allocation, and address turnover challenges, manufacturers can achieve significant improvements in both productivity and employee satisfaction.
We understand the complexities involved in navigating these changes and are committed to supporting manufacturers in harnessing the full potential of data analytics. Embracing these insights can lead to more informed decisions and better alignment of your workforce with your operational goals, ultimately driving greater success in your manufacturing processes.
Written on behalf of RES.
The RES Onboarding Process
Our commitment to you is deeper than just providing a list of potential candidates. We are committed to designing and implementing the most effective staffing strategy for you. Here is what you can expect when you choose Resource Employment Solutions as your recruiting and staffing partner.
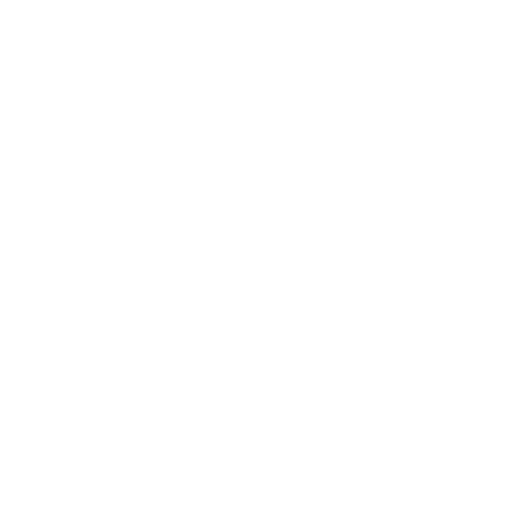
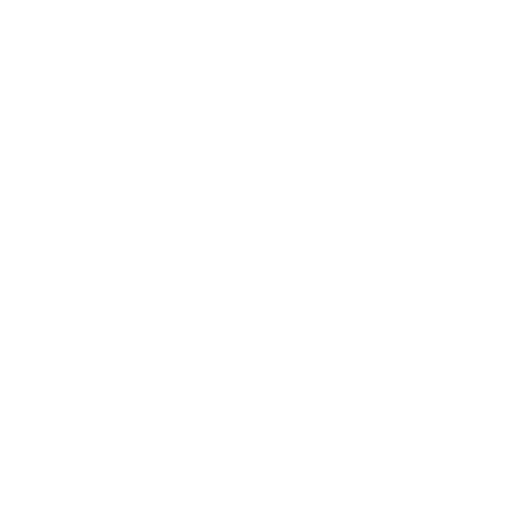
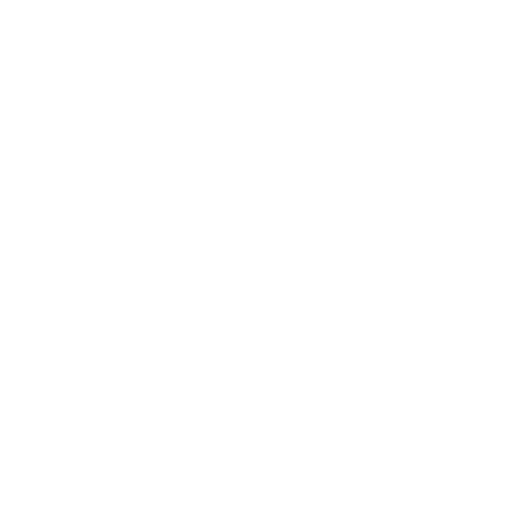
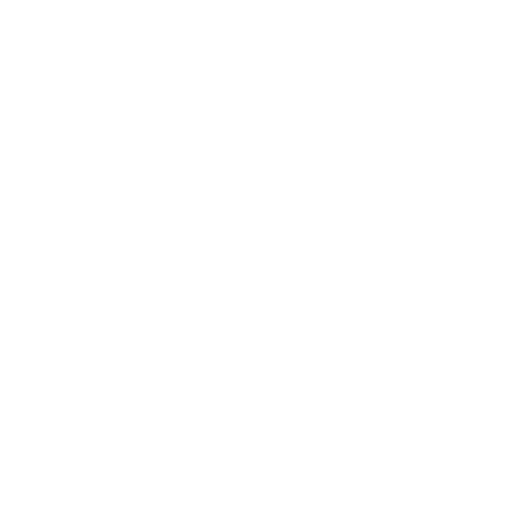
When you connect with Resource Employment Solutions, you will be matched with an account management team who specializes in placing top talent within your industry. You will have a dedicated recruiter or recruiting team assigned and they will remain your point of contact to understand your business and address all your staffing needs.
Frequently Asked Questions
Data analytics involves the process of collecting, analyzing, and interpreting data to make informed decisions. In manufacturing staffing, data analytics can help predict workforce needs, identify factors contributing to employee turnover, and provide real-time insights for agile decision-making. By leveraging data, companies can optimize their staffing processes, ensuring they have the right talent in place to meet production demands efficiently.
Predictive analytics uses historical data, industry trends, and algorithms to forecast future workforce needs. For manufacturing companies, this means being able to anticipate periods of high demand or slowdowns and adjusting staffing levels accordingly. This proactive approach minimizes the risks of under or overstaffing, ensuring that production targets are met without compromising quality or incurring unnecessary labor costs.
Yes, data analytics can significantly improve employee retention by identifying the factors that contribute to turnover. By analyzing employee data—such as performance reviews, tenure, and feedback—companies can detect patterns that lead to dissatisfaction and turnover. Interventions such as improving onboarding processes or providing career development opportunities can then be implemented to address these issues, ultimately leading to higher employee retention rates.