Tech Innovations in Manufacturing Workforce Planning | RES
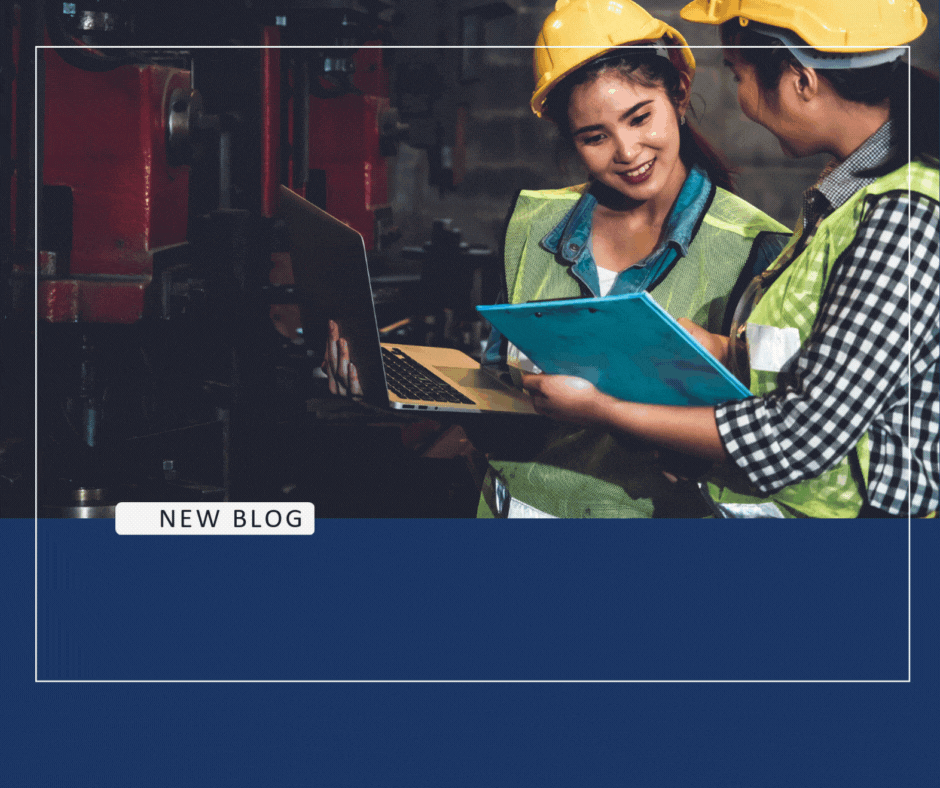
Technology is transforming workforce planning in manufacturing, helping companies streamline operations and boost efficiency. With the rise of data analytics, manufacturers can now predict workforce needs with greater accuracy, making informed staffing decisions. Automation is also reshaping the industry, requiring employees to reskill and upskill as traditional roles shift. Additionally, remote collaboration tools are enhancing communication and flexibility, allowing teams to work together more seamlessly, regardless of location. As these innovations evolve, it’s crucial for manufacturers to adapt their workforce strategies to stay competitive and meet changing market demands. Embracing these technological advancements is key to building a skilled workforce ready for the future of manufacturing. Book your consultation with Resource Employment Solutions today!
In today’s rapidly evolving manufacturing landscape, technology is not just an accessory; it’s a cornerstone of effective workforce planning. As companies strive to optimize production, streamline operations, and enhance employee engagement, leveraging advanced technologies has become essential. At Resource Employment Solutions, we understand these technological trends are crucial in delivering the right talent to meet the demands of the industry. This article will explore three key ways technology is reshaping workforce planning in manufacturing: data analytics, automation, and remote collaboration tools.
1. Data Analytics: Driving Informed Decisions
Data analytics has emerged as a game-changer in workforce planning. By harnessing large volumes of data, manufacturers can gain insights into various aspects of their operations, from production schedules to employee performance. Advanced analytics tools allow companies to forecast workforce needs based on historical data and market trends, enabling them to make informed decisions about hiring, training, and resource allocation.
For instance, consider a large automotive manufacturer that utilizes predictive analytics to determine the optimal staffing levels during peak production periods. By analyzing data from past sales, production cycles, and labor trends, the company can identify when to ramp up hiring and when to scale back. This proactive approach not only reduces labor costs but also ensures that the workforce is adequately prepared to meet customer demands.
2. Automation: Redefining Job Roles and Skills
Automation technology is revolutionizing manufacturing processes, but it also brings significant changes to workforce planning. As machines and software take over repetitive tasks, the nature of work is shifting. Manufacturers must now consider how to reskill and upskill their employees to meet new demands in the workplace.
Take, for example, a food processing plant that has implemented robotic systems for packaging. While these robots improve efficiency, they also require a new set of skills from the human workforce. Workers are now tasked with monitoring the robots, performing maintenance, and ensuring quality control. Consequently, workforce planning must incorporate training programs to equip employees with the skills needed to thrive in an automated environment.
Moreover, as some roles become obsolete, others will emerge, demanding a fresh approach to talent acquisition. Staffing companies play a pivotal role in helping manufacturers identify candidates with the right skill sets and in designing training programs that prepare existing employees for future roles.
3. Remote Collaboration Tools: Enhancing Communication and Flexibility
The rise of remote collaboration tools has also transformed workforce planning in manufacturing. These platforms facilitate seamless communication among teams, regardless of their physical location. With the advent of cloud-based software, manufacturing companies can easily share data, track project progress, and coordinate efforts across multiple sites.
For example, a global electronics manufacturer can utilize remote collaboration tools to manage its workforce spread across different countries. Through virtual meetings, real-time updates, and shared digital platforms, teams can collaborate on product development and troubleshooting without the need for constant in-person interactions. This flexibility not only enhances productivity but also allows companies to tap into a broader talent pool, including remote workers who can contribute their expertise from anywhere in the world.
As the manufacturing sector increasingly embraces remote collaboration, workforce planning must adapt to include strategies for managing remote teams effectively. This includes developing strong communication protocols and ensuring that remote workers have access to the necessary resources and support.
In conclusion, technology is fundamentally reshaping workforce planning in the manufacturing sector, providing innovative tools and strategies to address the challenges of a dynamic industry. From leveraging data analytics for informed decision-making to embracing automation and remote collaboration, manufacturers are better positioned to navigate market complexities and enhance productivity.
As these technological advancements continue to evolve, staying ahead of the curve will be essential for manufacturers looking to optimize their operations and workforce. Understanding the implications of these changes is crucial for fostering a skilled and adaptable workforce ready to meet the demands of the future. Embracing this transformation not only benefits companies but also contributes to a more resilient and responsive manufacturing ecosystem. Book your consultation to get started with Resource Employment Solutions.
Written on behalf of RES.
The RES Onboarding Process
Our commitment to you is deeper than just providing a list of potential candidates. We are committed to designing and implementing the most effective staffing strategy for you. Here is what you can expect when you choose Resource Employment Solutions as your recruiting and staffing partner.
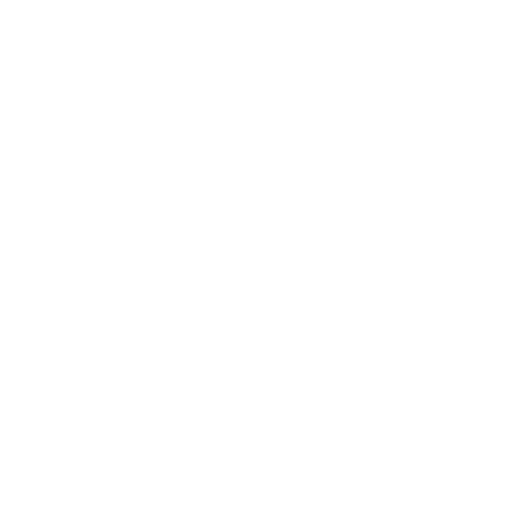
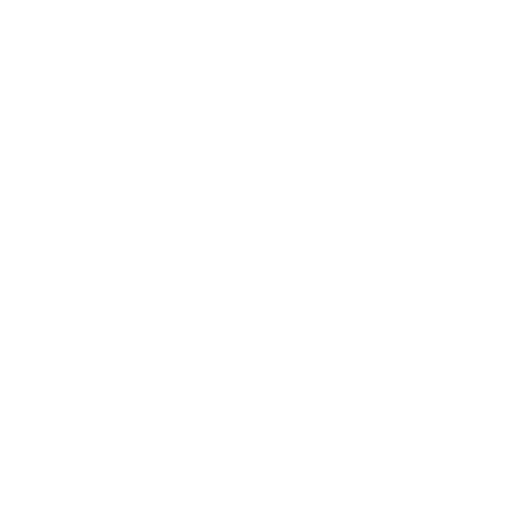
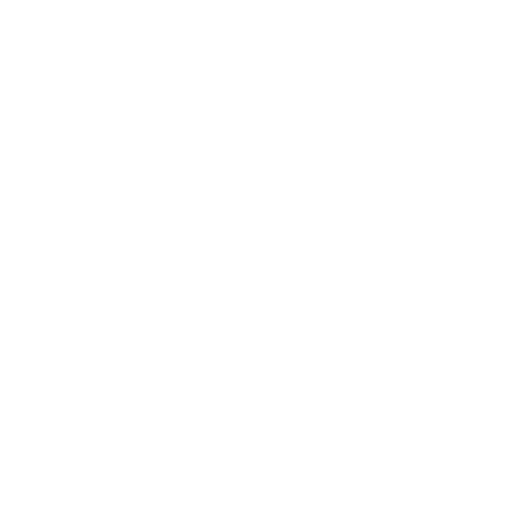
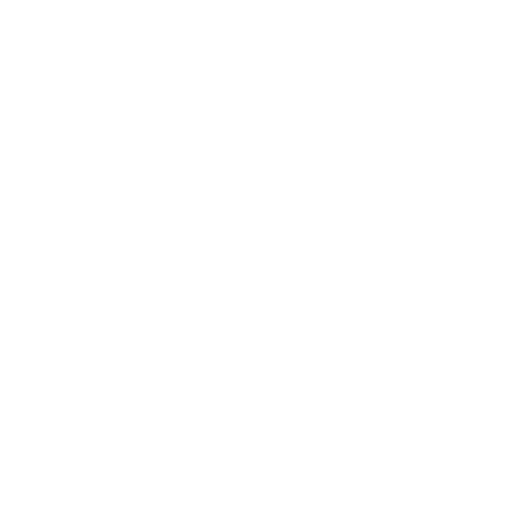
When you connect with Resource Employment Solutions, you will be matched with an account management team who specializes in placing top talent within your industry. You will have a dedicated recruiter or recruiting team assigned and they will remain your point of contact to understand your business and address all your staffing needs.
Frequently Asked Questions
Data analytics helps manufacturers forecast workforce needs by analyzing historical data and market trends, enabling informed hiring and resource allocation.
Automation changes job roles by taking over repetitive tasks, requiring workers to develop new skills for monitoring and maintaining automated systems.
These tools enhance communication and flexibility, allowing teams to collaborate effectively across different locations, thus improving productivity and project management.