The Future of Temporary Staffing in Manufacturing: Key Trends & Insights| RES
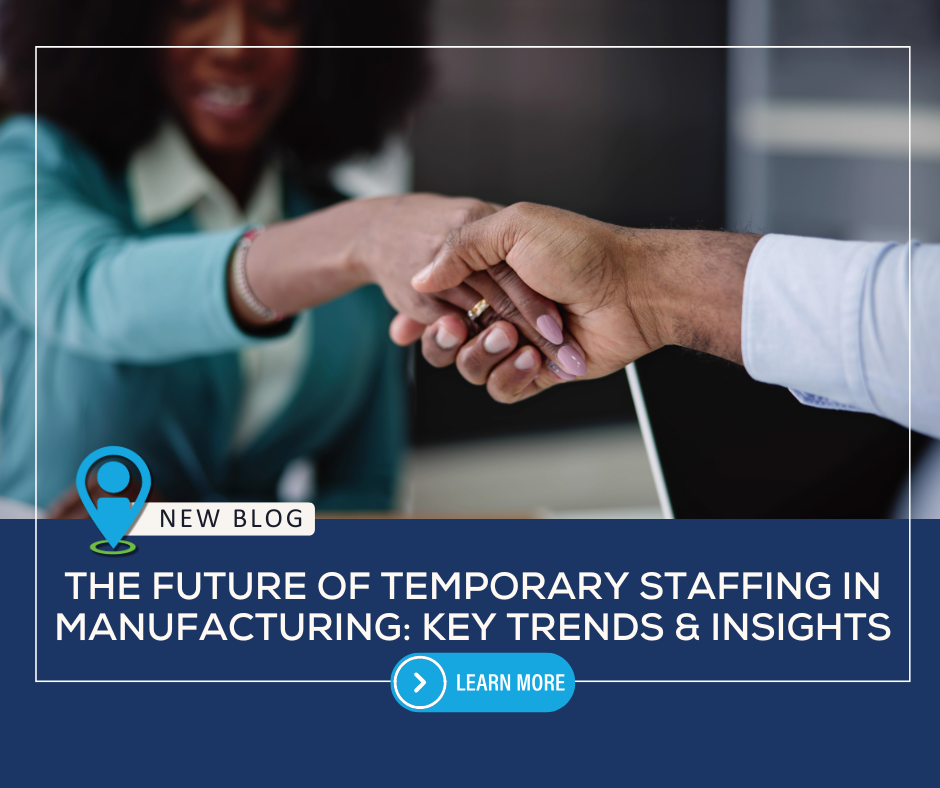
The future of temporary staffing in manufacturing is crucial as the industry adapts to changing economic and technological landscapes. Temporary staffing provides the flexibility manufacturers need to manage market fluctuations and seasonal demands efficiently. Integrating technology, such as workforce management platforms and AI-driven analytics, streamlines the sourcing, onboarding, and management of temporary staff, improving productivity and compliance. Additionally, modern temporary workers seek meaningful work, clear communication, and opportunities for skill development. Companies that prioritize these needs benefit from higher retention rates, enhanced morale, and increased performance. Embracing these strategies positions manufacturers to remain competitive and agile, ensuring that they are prepared to face future industry challenges effectively. Book your consultation with Resource Employment Solutions today!
The manufacturing industry is no stranger to change. From the advent of assembly lines to the current surge in automation and smart technologies, adaptability has always been key. One critical component that has seen significant evolution is the use of temporary staffing. With the global landscape continually shifting due to economic factors, technological advancements, and workforce dynamics, understanding the future of temporary staffing in manufacturing is essential for companies aiming to remain competitive and agile.
The Increasing Demand for Flexible Workforce Solutions
Manufacturers face an ever-changing production landscape, influenced by market fluctuations, seasonal demands, and technological developments. In response, many are turning to temporary staffing solutions to maintain flexibility. The demand for a flexible workforce allows companies to scale operations up or down as needed without the long-term commitments associated with permanent hiring.
Example: A mid-sized manufacturing firm specializing in consumer electronics often experiences surges in demand during holiday seasons. By leveraging temporary staff, they can efficiently handle these peaks without overextending their permanent workforce. This approach helps them meet production goals while keeping operational costs manageable.
Temporary staffing provides a bridge that supports manufacturers in balancing productivity and cost management. This workforce strategy offers companies the ability to respond swiftly to changes, minimizing downtime and maximizing output when it counts the most.
The Role of Technological Integration in Temporary Staffing
Technology is reshaping the way temporary staffing is approached in manufacturing. Digital platforms and automation are making it easier to source, onboard, and manage temporary employees with greater efficiency. The use of advanced workforce management systems ensures seamless integration of temporary workers, enabling manufacturers to optimize shift schedules, monitor productivity, and maintain compliance with labor regulations.
Example: A large automotive parts manufacturer implemented a workforce management platform that facilitated real-time scheduling and shift management for temporary staff. This allowed them to align staff allocation precisely with production needs, significantly reducing scheduling conflicts and enhancing overall productivity.
Furthermore, the integration of AI-driven analytics helps in predicting workforce needs, thereby supporting strategic planning and reducing the time spent on recruitment and training. This not only saves resources but also enhances the overall employee experience by ensuring better onboarding and clearer role expectations.
Adapting to the Evolving Workforce Expectations
The modern workforce, including temporary staff, has evolving expectations that manufacturing companies must consider. Temporary workers today seek more than just a paycheck—many value meaningful work experiences, clear communication, and opportunities for skills development. Companies that acknowledge these expectations tend to see higher retention rates, better morale, and improved performance.
Example: A manufacturing company specializing in packaging found that offering short-term training programs for their temporary staff improved job satisfaction and efficiency. Workers felt more engaged and confident, which led to fewer errors on the production line and greater overall output. This initiative also fostered a more cohesive workplace culture, where both permanent and temporary staff felt part of the team.
Manufacturers looking to stay ahead must adapt their strategies to create an environment that recognizes the contributions of temporary employees and aligns with modern workforce trends. Prioritizing well-being, communication, and opportunities for learning helps build a more resilient and motivated workforce, even on a temporary basis.
Temporary staffing in the manufacturing industry is set to play an increasingly vital role as companies seek ways to navigate a dynamic market landscape. The push for flexibility, integration of technology, and adapting to new workforce expectations are all central to this evolving trend. By staying proactive and embracing these changes, manufacturing companies can maintain a competitive edge, ensuring they remain agile and well-equipped to face future challenges. Book your consultation to get started with Resource Employment Solutions.
Written on behalf of RES.
The RES Onboarding Process
Our commitment to you is deeper than just providing a list of potential candidates. We are committed to designing and implementing the most effective staffing strategy for you. Here is what you can expect when you choose Resource Employment Solutions as your recruiting and staffing partner.
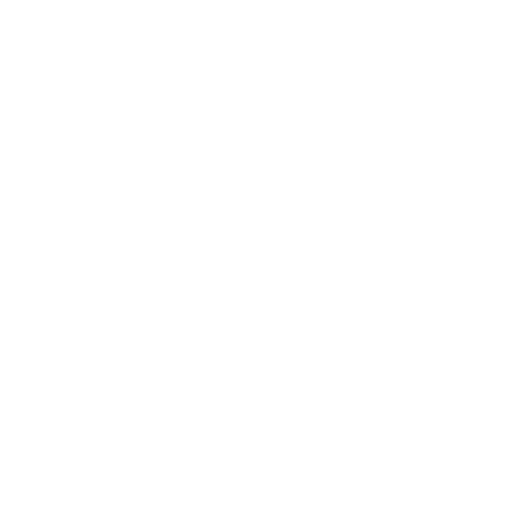
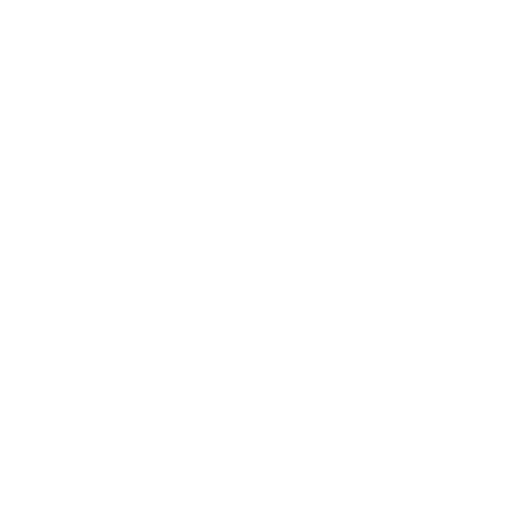
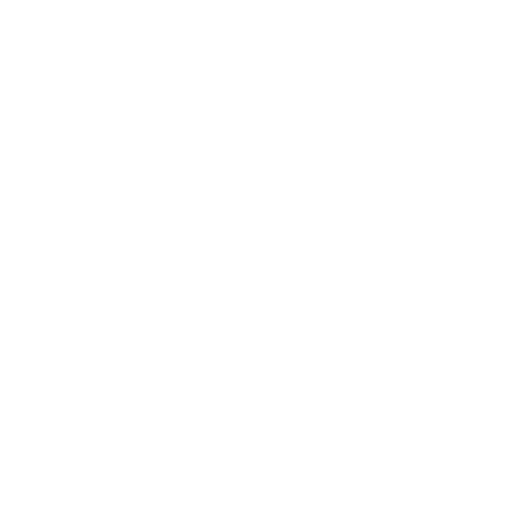
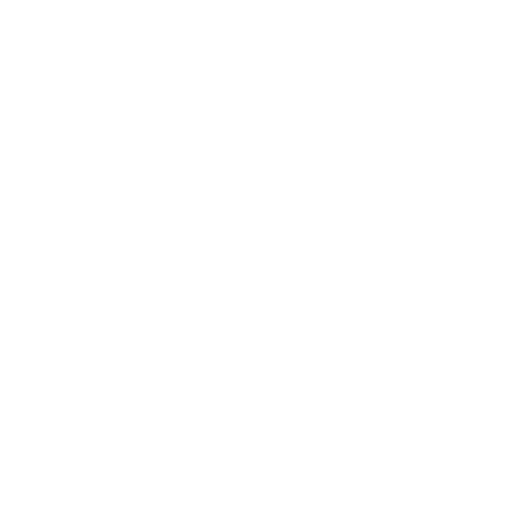
When you connect with Resource Employment Solutions, you will be matched with an account management team who specializes in placing top talent within your industry. You will have a dedicated recruiter or recruiting team assigned and they will remain your point of contact to understand your business and address all your staffing needs.
Frequently Asked Questions
Temporary staffing is increasingly important in manufacturing due to the need for flexibility in response to market fluctuations, seasonal demands, and economic changes. It allows companies to scale operations without long-term commitments, balancing productivity and cost efficiency.
Technology, such as workforce management platforms and AI-driven analytics, streamlines the recruitment and management of temporary staff. This improves onboarding, scheduling, and compliance, ultimately enhancing productivity and reducing conflicts.
Workforce management systems help align staffing with production needs, optimize shift schedules, and ensure real-time monitoring of productivity, leading to better efficiency and fewer scheduling issues.