The Impact of Automation on Manufacturing Staffing and Workforce Needs
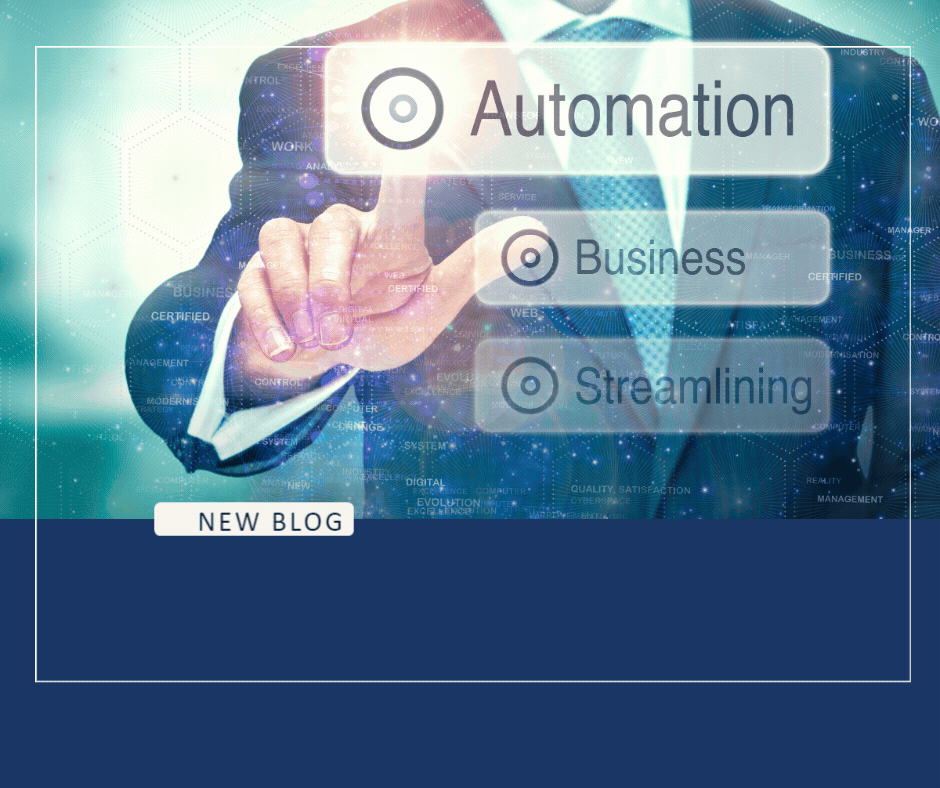
Automation is transforming the manufacturing sector, significantly impacting staffing needs and reshaping workforce dynamics. As machines take over routine tasks, the demand for advanced technical skills is rising, necessitating a shift in workforce competencies. Upskilling and reskilling existing employees have become essential strategies, enabling workers to adapt to new technologies and continue contributing meaningfully to the organization. While automation enhances efficiency and precision, human expertise remains indispensable, particularly in areas requiring intuition, creativity, and complex problem-solving. Balancing automation with human labor is crucial for maintaining high productivity, safety, and quality. Manufacturers must thoughtfully integrate these changes to build a resilient and adaptable workforce, ensuring long-term success in an increasingly automated and competitive industry.
In the manufacturing sector, the rise of automation has brought about significant changes, revolutionizing the way products are made and how workforces are managed. Automation promises increased efficiency, precision, and scalability, but it also presents new challenges, particularly in terms of staffing. As machines and artificial intelligence take over more tasks, the demand for certain types of labor decreases, while the need for new skills and roles emerges. Understanding the impact of automation on staffing is crucial for manufacturers who want to stay competitive and effectively manage their workforce.
At Resource Employment Solutions, we recognize that the integration of automation requires a strategic approach to workforce management. Our goal is to help manufacturers navigate these changes, ensuring they have the right talent in place to meet both current and future demands. Whether it’s upskilling existing employees, finding new talent with specialized skills, or balancing the human-machine interface, our tailored staffing solutions are designed to support manufacturers in this evolving landscape.
Shift in Skill Requirements
One of the most profound impacts of automation on manufacturing staffing is the shift in skill requirements. As routine, manual tasks are increasingly performed by machines, the demand for low-skilled labor decreases. However, this does not mean that human workers are no longer needed. Instead, there is a growing demand for employees with advanced technical skills who can operate, maintain, and troubleshoot automated systems.
Example: A food processing plant that recently automated its packaging line found that it no longer needed as many workers for repetitive manual tasks. However, they needed to hire new employees with expertise in robotics and machine maintenance. Additionally, existing employees had to be retrained to work alongside the new technology, learning how to monitor the automated systems and intervene when necessary.
The Role of Upskilling and Reskilling
As automation reshapes the manufacturing landscape, upskilling and reskilling have become critical strategies for workforce development. Rather than replacing employees, many manufacturers are choosing to invest in their existing workforce by providing training programs that equip them with the skills needed to work with new technologies.
Example: A mid-sized automotive parts manufacturer implemented a comprehensive upskilling program to prepare its employees for the introduction of automated assembly lines. Workers who previously performed manual assembly were trained in areas such as programming, robotics, and data analysis. This not only allowed the company to retain its workforce but also improved overall productivity and efficiency, as employees were able to take on more complex and valuable tasks.
Balancing Automation with Human Expertise
While automation can significantly enhance production processes, it is not a complete replacement for human expertise. There are still many areas in manufacturing where human intuition, creativity, and problem-solving skills are irreplaceable. The challenge for manufacturers is to strike the right balance between automation and human labor, ensuring that both are leveraged effectively.
Example: In a high-tech electronics manufacturing facility, automation is used for precision tasks such as soldering and assembling small components. However, quality control and final inspection are still performed by skilled human workers who can identify subtle defects and make judgment calls that machines are not yet capable of. By combining the strengths of automation with the unique capabilities of human employees, the company achieves high levels of efficiency and product quality.
The impact of automation on manufacturing staffing needs is undeniable and requires a thoughtful and strategic approach to workforce management. As manufacturers continue to integrate automation into their processes, it's essential to recognize and address the evolving skills required for this new landscape. Upskilling and reskilling initiatives play a crucial role in helping employees transition to more complex roles, ensuring that they remain valuable contributors to the business.
Moreover, finding the right balance between automation and human expertise is key to maintaining efficiency and quality in production. While machines can handle many tasks with precision and speed, human intuition and problem-solving remain irreplaceable in certain areas. By thoughtfully combining technology with human skills, manufacturers can create a more robust and adaptable workforce, ready to meet the demands of the future.
Written on behalf of RES.
The RES Onboarding Process
Our commitment to you is deeper than just providing a list of potential candidates. We are committed to designing and implementing the most effective staffing strategy for you. Here is what you can expect when you choose Resource Employment Solutions as your recruiting and staffing partner.
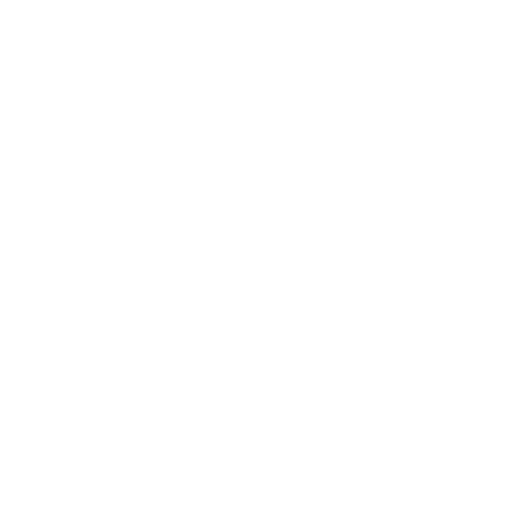
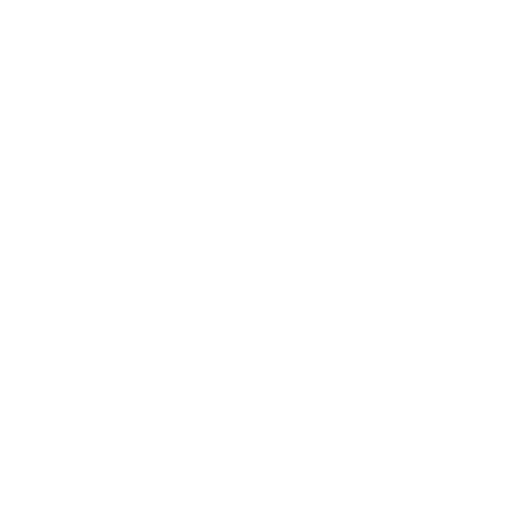
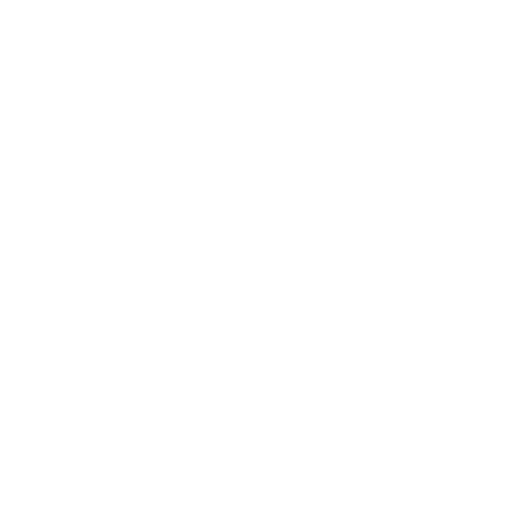
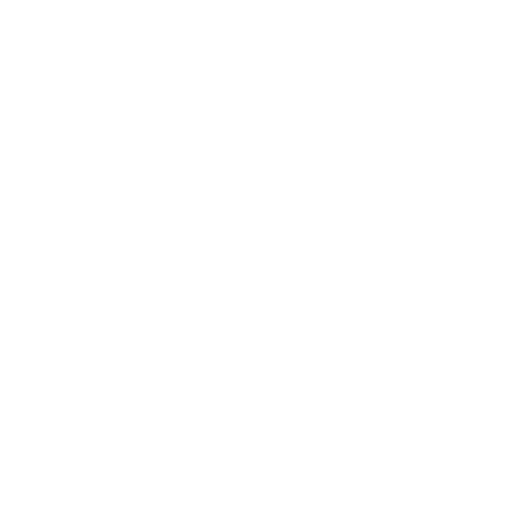
When you connect with Resource Employment Solutions, you will be matched with an account management team who specializes in placing top talent within your industry. You will have a dedicated recruiter or recruiting team assigned and they will remain your point of contact to understand your business and address all your staffing needs.
Frequently Asked Questions
Automation is reducing the demand for routine manual labor while increasing the need for employees with advanced technical skills. As machines take over repetitive tasks, manufacturers require workers who can operate, maintain, and troubleshoot automated systems, necessitating a shift in workforce competencies.
As automation becomes more prevalent, there is a growing demand for skills in robotics, machine maintenance, programming, and data analysis. Employees who can work alongside automated systems and ensure they run smoothly are highly sought after in the manufacturing industry.
Manufacturers can support their workforce by investing in upskilling and reskilling programs. These programs provide employees with the training they need to develop new technical skills, enabling them to transition into more advanced roles and continue contributing to the company’s success.