The Pros and Cons of Outsourcing vs. In-House Staffing in Manufacturing
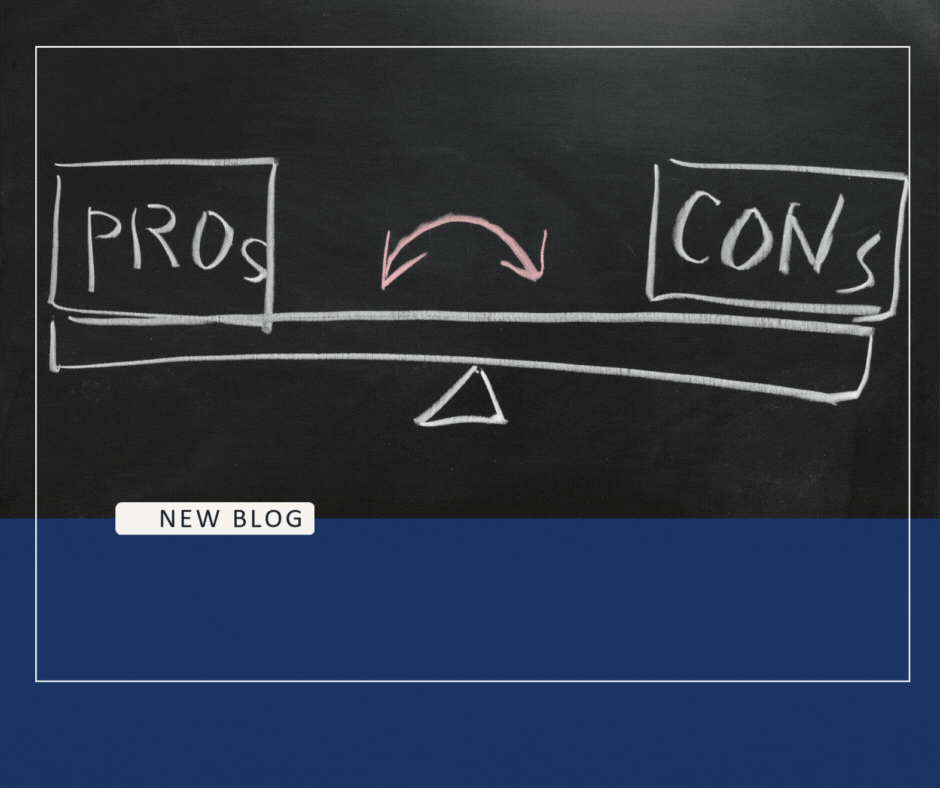
Struggling to decide between outsourcing or in-house staffing for your manufacturing needs? Both options have their perks—and their challenges. Whether you're in Illinois, Texas, or Florida, finding the right staffing approach can impact your bottom line, flexibility, & overall productivity. Outsourcing offers cost savings, scalability, and access to specialized expertise, while in-house staffing provides greater control, stronger team culture, and better communication. But which option suits your business best? This blog breaks down the pros and cons of each, helping manufacturers make informed decisions to meet their specific goals. If you’re looking to optimize your staffing strategy, this guide will help you choose the path that sets your business up for long-term success. Book your consultation with Resource Employment Solutions today!
In the manufacturing sector, staffing plays a critical role in meeting production goals, ensuring quality, and maintaining smooth operations. As the industry evolves, manufacturers in states like Illinois, New Jersey, North Carolina, Florida, Ohio, Texas, Georgia, Nevada, and Pennsylvania face a crucial decision: Should they outsource certain roles or continue to rely on in-house staffing? Both options offer distinct advantages and disadvantages, and choosing the right approach depends on a variety of factors, including cost, control, expertise, and long-term business goals.
The Pros of Outsourcing in Manufacturing
Cost Savings
One of the biggest advantages of outsourcing is cost savings. Manufacturers can reduce overhead by outsourcing tasks to third-party providers. This is particularly useful for roles that are seasonal, temporary, or highly specialized. For example, instead of hiring full-time staff for temporary needs during peak production times, manufacturers in states like Ohio or Georgia can use outsourced labor to save on wages, benefits, and training costs.
Access to Specialized Expertise
Outsourcing provides manufacturers with access to specialized skills and expertise that may not be available in-house. For instance, if a manufacturer in Florida needs help with a specific piece of machinery or technology, outsourcing to a team of experts can help resolve issues more quickly and efficiently. By partnering with a staffing agency or a service provider, manufacturers can tap into a broader talent pool and bring in experts as needed.
Flexibility and Scalability
Manufacturers often experience fluctuations in demand, which can make staffing needs unpredictable. Outsourcing offers flexibility, allowing companies to scale their workforce up or down based on production requirements. For example, manufacturers in Nevada or Texas experiencing a seasonal spike in demand can outsource labor to meet short-term needs without the long-term commitment of hiring full-time employees.
Focus on Core Business Functions
Outsourcing allows manufacturers to focus on their core business functions by delegating non-essential tasks to external providers. This means more attention can be given to product development, innovation, and improving production processes. In industries where staying competitive is critical, outsourcing can help companies in Illinois or Pennsylvania remain agile and responsive to market changes.
The Cons of Outsourcing in Manufacturing
Loss of Control
One of the major drawbacks of outsourcing is the potential loss of control. When certain functions are outsourced, manufacturers may have less oversight over the quality and consistency of the work being done. This can be a concern for companies that require strict adherence to specific standards, particularly in sectors where quality control is paramount, such as pharmaceuticals or automotive manufacturing.
Communication Challenges
Outsourcing to third-party providers, especially those located in different states or countries, can lead to communication barriers. Manufacturers in North Carolina or New Jersey may experience delays or misunderstandings when working with outsourced teams, which can impact production timelines and cause frustration.
Potential Security Risks
When outsourcing, manufacturers may need to share sensitive information with third-party providers, which can pose security risks. Ensuring that data, intellectual property, and other confidential materials are properly protected is critical. In states like Florida and Texas, where cybersecurity regulations are increasingly stringent, manufacturers need to be vigilant about outsourcing relationships that involve access to proprietary information.
The Pros of In-House Staffing in Manufacturing
Greater Control and Oversight
In-house staffing allows manufacturers to maintain full control over their workforce. Managers can directly oversee production, ensure quality standards are met, and quickly address any issues that arise. For companies in highly regulated industries, such as those in New Jersey or Ohio, having direct oversight of employees can be a major advantage.
Stronger Company Culture and Employee Loyalty
In-house staff are typically more invested in the company’s success and are more likely to align with the company’s culture and values. By fostering a strong sense of loyalty, manufacturers in Illinois or Pennsylvania can build a dedicated workforce that is committed to the company’s long-term growth. Additionally, employees who feel valued and engaged are more likely to stay with the company, reducing turnover rates.
Better Communication and Collaboration
When employees are part of an in-house team, communication and collaboration are often more seamless. Teams can work together more closely, address issues in real-time, and share knowledge more effectively. For manufacturers in Georgia or North Carolina, having a cohesive in-house team can help improve efficiency and productivity across the board.
The Cons of In-House Staffing in Manufacturing
Higher Costs
One of the most significant drawbacks of in-house staffing is the cost. Hiring full-time employees comes with a range of expenses, including wages, benefits, training, and overhead. For manufacturers in states like Texas or Nevada, where labor costs can be high, maintaining an in-house staff for every role may not always be financially feasible.
Limited Access to Specialized Skills
Manufacturers relying solely on in-house staff may struggle to find employees with the specialized skills needed for certain tasks. For example, a manufacturer in Florida might not have the in-house expertise to handle the latest automation technology, forcing them to invest heavily in training or hiring consultants.
Difficulty Scaling Quickly
In-house staffing can also make it more challenging to scale quickly during periods of high demand. Hiring new employees takes time, and onboarding and training processes can slow down production. Manufacturers in Ohio or Georgia who need to ramp up production quickly might find it difficult to meet deadlines with a fully in-house team.
Conclusion
When it comes to staffing in manufacturing, both outsourcing and in-house staffing have their advantages and drawbacks. Outsourcing offers cost savings, flexibility, and access to specialized expertise, but it may come at the cost of control and communication. In-house staffing provides greater oversight, stronger company culture, and better communication, but it can be more expensive and harder to scale quickly.
For manufacturers in Illinois, New Jersey, North Carolina, Florida, Ohio, Texas, Georgia, Nevada, and Pennsylvania, the decision ultimately depends on the specific needs and goals of the business. Many companies find that a hybrid approach, combining the benefits of both outsourcing and in-house staffing, offers the best of both worlds. By carefully weighing the pros and cons, manufacturers can create a staffing strategy that supports both immediate and long-term success. Book your consultation to get started with Resource Employment Solutions.
Written on behalf of RES.
The RES Onboarding Process
Our commitment to you is deeper than just providing a list of potential candidates. We are committed to designing and implementing the most effective staffing strategy for you. Here is what you can expect when you choose Resource Employment Solutions as your recruiting and staffing partner.
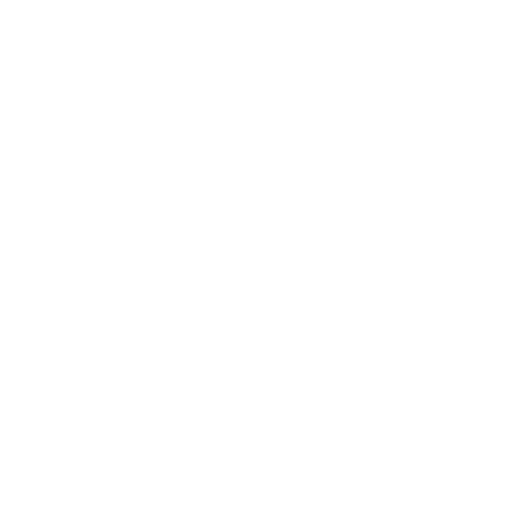
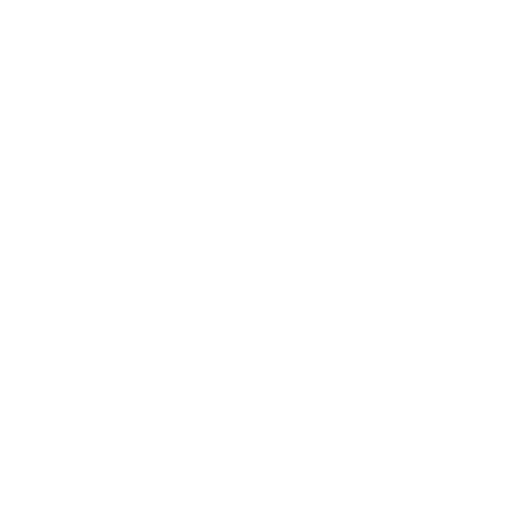
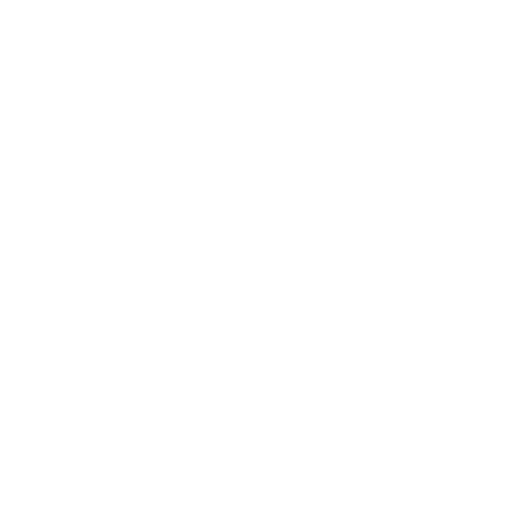
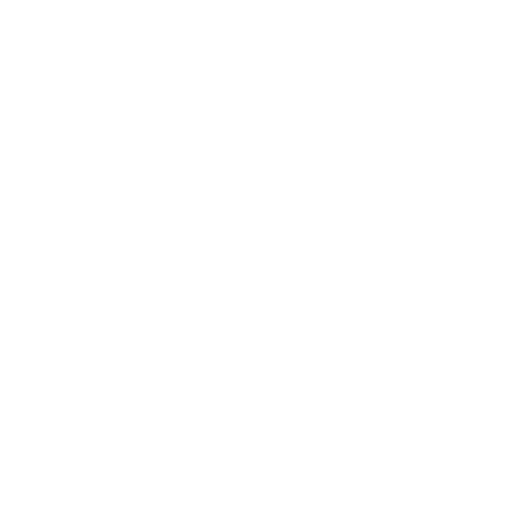
When you connect with Resource Employment Solutions, you will be matched with an account management team who specializes in placing top talent within your industry. You will have a dedicated recruiter or recruiting team assigned and they will remain your point of contact to understand your business and address all your staffing needs.
Frequently Asked Questions
Yes, in-house staffing typically involves higher costs, including wages, benefits, training, and overhead, making it more expensive than outsourcing.
A hybrid approach allows businesses to outsource specialized or temporary tasks while maintaining control over core operations with in-house staff. Book a consultation to learn more!
Outsourcing can lead to a loss of control, communication challenges, and potential security risks, especially when sensitive information is shared.