The Role of Continuous Learning in Advancing Manufacturing Careers
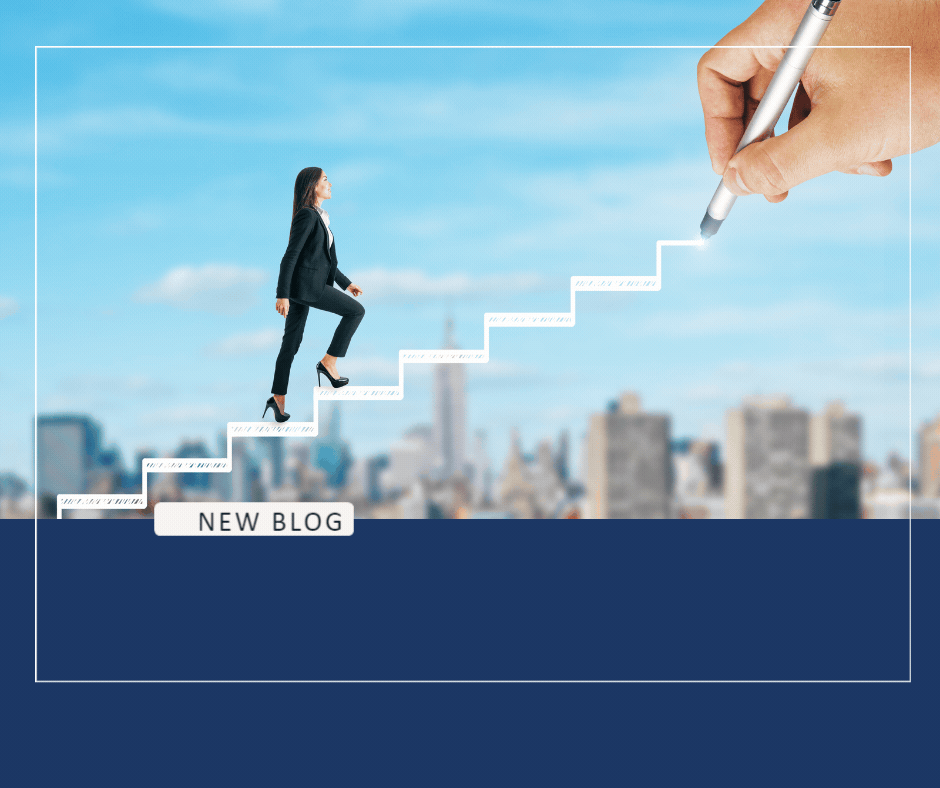
Continuous learning is essential in the manufacturing industry, where rapid technological advancements demand an adaptable, skilled, and continuously evolving workforce. This article explores the critical role of ongoing education in keeping pace with new technologies, enhancing employee versatility, and promoting long-term career growth. By investing in continuous learning, employees can stay relevant and competitive, while employers benefit from a more agile, capable, and future-ready workforce. Examples include companies that have successfully implemented training programs to help workers operate advanced machinery or transition into new roles seamlessly. Ultimately, continuous learning is vital for sustaining long-term success in a constantly evolving industry, ensuring that both employees and organizations are well-prepared to meet the challenges of the future.
In the rapidly evolving manufacturing industry, the importance of continuous learning cannot be overstated. As technology advances and production processes become more sophisticated, the skills required for manufacturing careers are constantly changing. For workers to stay relevant and competitive, ongoing education and skill development are essential. Continuous learning is not just a pathway to career growth but also a critical factor in maintaining the efficiency and innovation that modern manufacturing demands.
At Resource Employment Solutions, we recognize that continuous learning is the cornerstone of career advancement and industry success. We are committed to helping both employers and employees navigate the challenges of an ever-changing landscape by providing access to the training and resources necessary to stay ahead. Our mission is to empower manufacturing professionals to enhance their skills, adapt to new technologies, and achieve their career goals through lifelong learning.
Keeping Up with Technological Advancements
One of the most significant drivers of continuous learning in manufacturing is the rapid pace of technological advancements. From automation and robotics to advanced data analytics and artificial intelligence, new technologies are transforming how manufacturing processes are designed and executed. Workers need to be well-versed in these technologies to operate and maintain the equipment, as well as to leverage data for decision-making.
Example: A manufacturing company recently introduced a new automated assembly line that significantly increased production speed and accuracy. However, the success of this new technology depended on the workforce's ability to understand and operate it. The company invested in continuous learning programs, offering courses in robotics, programming, and data analysis to ensure that employees could fully utilize the new equipment. This not only improved operational efficiency but also provided employees with valuable skills that enhanced their career prospects.
Enhancing Employee Adaptability and Versatility
In the manufacturing industry, versatility is a key asset. Workers who can adapt to new roles and responsibilities are more valuable to employers, especially in times of change or when dealing with unexpected challenges. Continuous learning enables employees to expand their skill sets, making them more adaptable and versatile in their careers.
Example: During a period of economic uncertainty, a manufacturing plant faced fluctuating demand and needed to reassign workers to different tasks to maintain production levels. Employees who had engaged in continuous learning were able to transition smoothly into new roles, whether it was learning how to operate different machinery or taking on responsibilities in quality control. Their versatility allowed the company to remain agile and responsive to market changes, highlighting the importance of ongoing skill development.
Promoting Career Growth and Job Satisfaction
Continuous learning not only benefits employers but also has a profound impact on employees' career growth and job satisfaction. When workers have access to ongoing education and training opportunities, they are more likely to feel valued and motivated. This investment in their development leads to higher job satisfaction, increased loyalty, and better retention rates.
Example: A mid-sized manufacturing firm implemented a career development program that included continuous learning opportunities, such as certifications, workshops, and mentorship. Employees were encouraged to pursue training in areas that interested them, whether it was leadership, technical skills, or project management. As a result, many employees were able to advance into higher positions within the company, leading to increased job satisfaction and a stronger, more capable workforce. This program not only benefited individual careers but also helped the company develop a pool of talented leaders who were well-equipped to drive future growth.
The importance of continuous learning in manufacturing careers cannot be overstated. It plays a vital role in keeping pace with technological advancements, enhancing employee adaptability, and promoting long-term career growth. As the manufacturing industry continues to evolve, those who prioritize ongoing education and skill development are better positioned to thrive and contribute meaningfully to their organizations. For employers, fostering a culture of continuous learning helps build a workforce that is resilient, innovative, and prepared for the challenges ahead.
Ultimately, embracing continuous learning benefits both employees and the broader industry, ensuring that the workforce remains competitive and capable in a rapidly changing landscape. In an era where technological progress is constant, the commitment to lifelong learning is a key factor in sustaining success and driving future growth in manufacturing.
Written on behalf of RES.
The RES Onboarding Process
Our commitment to you is deeper than just providing a list of potential candidates. We are committed to designing and implementing the most effective staffing strategy for you. Here is what you can expect when you choose Resource Employment Solutions as your recruiting and staffing partner.
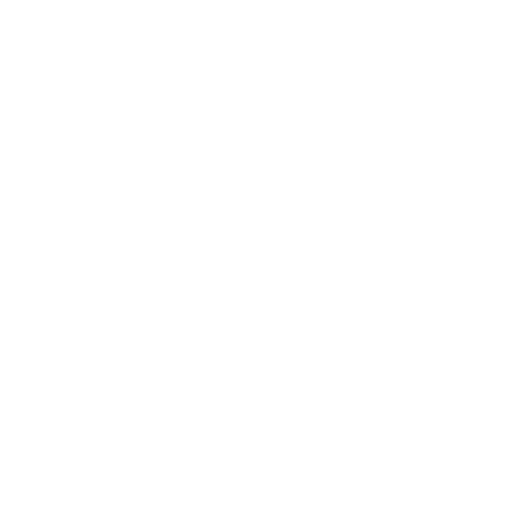
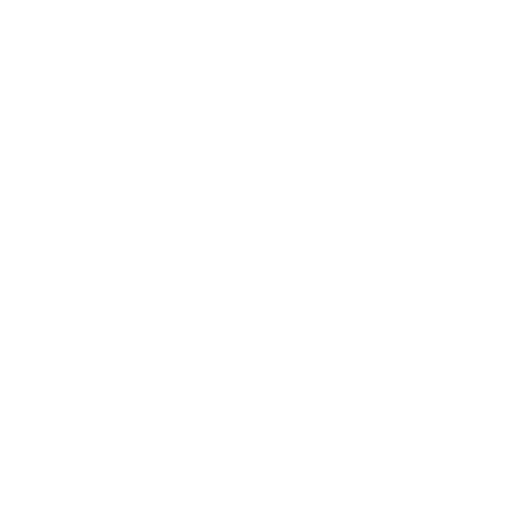
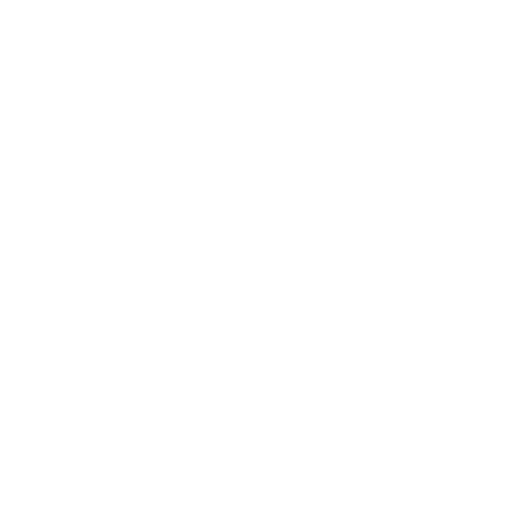
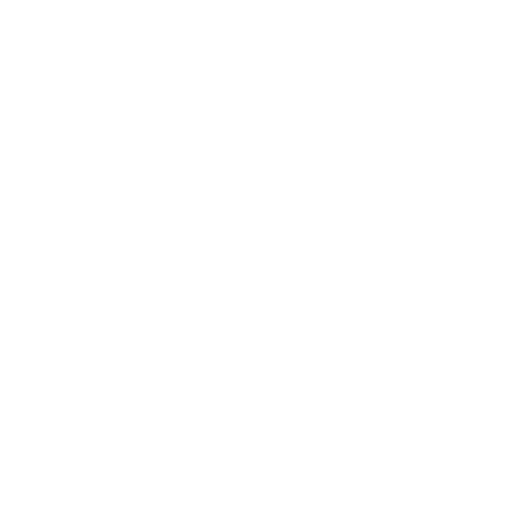
When you connect with Resource Employment Solutions, you will be matched with an account management team who specializes in placing top talent within your industry. You will have a dedicated recruiter or recruiting team assigned and they will remain your point of contact to understand your business and address all your staffing needs.
Frequently Asked Questions
Continuous learning is crucial in the manufacturing industry because it helps workers stay up-to-date with rapidly evolving technologies and processes. As new machinery, automation, and software are introduced, ongoing education ensures that employees remain skilled, adaptable, and capable of operating advanced equipment efficiently.
Continuous learning benefits employees by enhancing their skill sets, making them more versatile and valuable in the workplace. It also opens up opportunities for career advancement, increases job satisfaction, and improves their ability to adapt to new roles and responsibilities as the industry evolves.
A manufacturing company introduced a continuous learning program that included training in robotics, programming, and data analysis for its employees. This allowed workers to effectively operate new automated assembly lines, improving production efficiency and enabling them to acquire valuable skills that enhanced their career prospects.